Advancing multifunctional composite wings and fuselage structures
Flexible printed circuits and the Advanced Concepts for Aero‑Structures with Integrated Antennas and Sensors (ACASIAS) consortium.
Flexible Printed Circuits in unlimited lengths
Earlier this year, (Gloucestershire, UK) shipped a 26-meter long multilayer flexible printed circuit (FPC) —believed to be the longest ever produced — for distributing power and control signals across the wings of a solar-powered, unmanned aerial vehicle (UAV). In fact, Trackwise supplied more than 50 FPCs for this vehicle, cutting weight by 60% versus using conventional wire harnesses for aircraft power and control.
This weight savings enables the US-made UAV to achieve higher payload and/or improved speed and range. Trackwise manufactures the FPCs using (IHT), a patented, reel-to-reel manufacturing technique. IHT overcomes conventional manufacturing limitations which have kept most FPCs below two meters in length, and enables Trackwise to produce FPCs in unlimited lengths.

A 5-meter long, 6-layer flex PCB manufactured by Trackwise.
The FPCs that Trackwise delivered for the 26-meter-wingspan UAV were based on a polyimide substrate. Their planar structure dissipates heat better than conventional wiring, enabling higher current carrying capacity for a given weight of copper conductor. Other benefits include:
- Printed manufacturing ensures circuit consistency
- Fewer connection points are needed so reliability is enhanced
- The FPC is easier to install than wire harnesses, reducing a vehicle’s assembly time and cost.
According to Trackwise CEO, Philip Johnston, many new aerospace and automotive applications are emerging for these long, lightweight flexible, multilayer, printed circuit boards (flex PCBs). Both industries are seeing a push toward electrification simultaneous with a need for more sensors and control.
FPCs in composites?
Curious to know if Trackwise was embedding this FPC into composites, I began a discussion with Neil Bartlett, Trackwise director of sales and marketing. “For the UAV application highlighted in our March press release, the flex [flexible PCBs] were not embedded into a composite,” he concedes. “However, their planar nature makes them entirely suited to embedding into composites and enabling multi-functional structures. We are in preliminary discussions regarding incorporating flex — both power and signal variants — across a broad range of possible applications including aerospace, defense and construction. Trackwise is also a member of Advanced Concepts for Aero‑Structures with Integrated Antennas and Sensors (ACASIAS) – a consortium of 11 partners which is developing innovative technologies for integrating antennas into composites and aircraft structures.” ()

A smart winglet with integrated blade VHF (Very High Frequency) antenna.
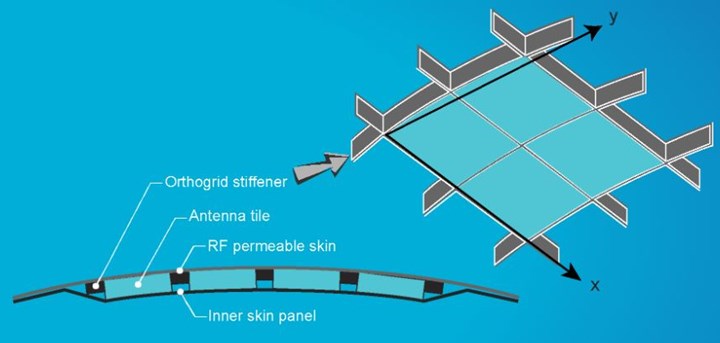
Stiffened orthogrid fuselage panel for the integration of a Ku-band SATCOM antenna array.

Active Structural Acoustic Control system for reduction of CROR cabin noise with minimal impact on weight. SOURCE | http://www.acasias-project.eu/files/Acasias_poster_v2.pdf
Bartlett says that flex PCBs made using IHT and composites are very synergistic in what they are offering the market and the advantages of combining/embedding them are compelling, including:
- Weight savings (elimination of fixing fixtures)
- Improved ruggedness/protection offered by composites = improved reliability/reduced maintenance
- Reduced space envelope = improved payload capability/structural efficiency
- Improved installation = less labor touch points (improved reliability), less time and cost.

This demonstrator flex antenna embedded into a glass fiber composite was manufactured by Trackwise in collaboration with Rockwood Composites and exhibited at JEC World 2019. SOURCE | Trackwise
Moving forward
IHT revenues are up 217% with customers and development opportunities increasing from 7 at the start of 2018 to 45 by March 2019. Trackwise has also installed two new process lines.
Several ACASIAS projects will be presented at the (EMuS, June 11-12, Barcelona, Spain), which is co-chaired by ACASIAS coordinator Dr. Harmen Schippers, Netherlands Aerospace Center (NLR, Marknesse). Highlights include:
- Airbus Defense and Space has explored embedding an electronic steerable SATCOM antenna operating at Ka band of a passenger aircraft. The project is partly funded under Clean Sky 2 and include partners GILAT, RAYSAT and FBM Composite Materials Ltd.
- NLR is exploring an into a composite fuselage, using a radio-transparent glass fiber skin and carbon fiber composite ribs.
- The German Aerospace Center (DLR) and China’s AVIC Beijing Institute of Aeronautical Materials (BIAM) have investigated the use of recycled carbon fibers to increase the mechanical strength and multifunctional aspects of bio-composites, looking at electrically conductive composites for electromagnetic interference (EMI) shielding and lightning strike protection (LSP) via the .
Related Content
Airbus video highlights RACER compound helicopter first flight
Launched as part of a Clean Sky 2 program, a compound design — rotor, split fixed-wing, propulsive propellers — uses composites to cut fuel consumption and emissions by 20%.
Read MorePlant tour: Aernnova Composites, Toledo and Illescas, Spain
RTM and ATL/AFP high-rate production sites feature this composites and engineering leader’s continued push for excellence and innovation for future airframes.
Read MoreThe potential for thermoplastic composite nacelles
Collins Aerospace draws on global team, decades of experience to demonstrate large, curved AFP and welded structures for the next generation of aircraft.
Read MoreMikrosam equips BTU Germany with single-tape AFP head for Type 5 pressure vessels
Delivery of upgraded placement head provides additional automated layup flexibility, quality control for the university’s latest projects advancing Type 4 and 5 hydrogen storage.
Read MoreRead Next
Assembling the Multifunctional Fuselage Demonstrator: The final welds
Building the all-thermoplastic composite fuselage demonstrator comes to an end with continuous ultrasonic welding of the RH longitudinal fuselage joint and resistance welding for coupling of the fuselage frames across the upper and lower halves.
Read MoreAll-recycled, needle-punched nonwoven CFRP slashes carbon footprint of Formula 2 seat
Dallara and Tenowo collaborate to produce a race-ready Formula 2 seat using recycled carbon fiber, reducing CO2 emissions by 97.5% compared to virgin materials.
Read More“Structured air” TPS safeguards composite structures
Powered by an 85% air/15% pure polyimide aerogel, Blueshift’s novel material system protects structures during transient thermal events from -200°C to beyond 2400°C for rockets, battery boxes and more.
Read More