Vastek Industrial showcases tabletop infrared conveyor oven
Ideal for laboratory testing and low-volume production applications, the D-100 model is highly compact, and ensures edge-to-edge temperature uniformity.
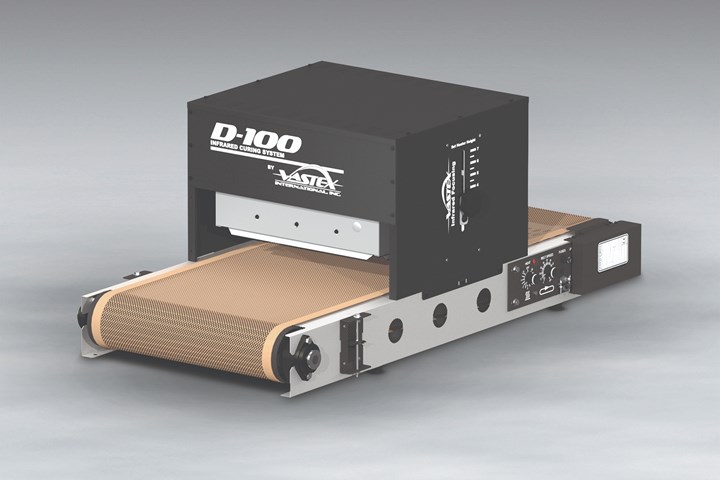
Photo Credit: Vastek Industrial
(Bethlehem, Penn., U.S.) showcases its D-100 model infrared conveyor oven for laboratory testing and low-volume production applications. At 46 in (117 cm) long x 24 in (61 cm) wide x 24 in (61 cm) high, the compact unit fits in tight spots and can be placed on tabletops or wheeled utility carts with tops as small as 24 in (61 cm).
Offered in 120V or 240V models, the oven is equipped with a 16 in (40 cm) square 1625-watt infrared heater that achieves temperatures up to 750°F (400°C). Heater shields maximize edge-to-edge temperature uniformity, while variable controls for both heat intensity and conveyor speed allow fine-tuning of the heating process.
The heating chamber has a fixed in-feed width of 19.5 in (49.6 cm), and an in-feed height that can be raised and lowered from 2-7 inches (5 to 17.7 cm). The heater can also be raised, lowered and pivoted using lock knobs on the sides of the heating chamber according to the shape of the items for uniform heating. Heater shields are included as standard to maximize edge-to-edge temperature consistency.
Further, the oven is equipped as standard with an 18 in-wide (45.8 cm) Teflon-coated fiberglass conveyor belt driven by a 50 lb motor, and aligned by a continuously variable tracking device patented by the company. Optional Kevlar and stainless steel mesh belts are offered for high-heat and/or sanitary applications.
Larger conveyor/tunnel models are available with belt widths up to 54 in (137 cm), chamber lengths up to 162 in (412 cm) and infrared heaters to 68,400 watts. A 3-year warranty against defects and a 15-year warranty on infrared heaters are standard.
Also offered are cabinet/batch ovens in three sizes with forced, filtered air, adjustable racks and stainless steel finned strip heaters up to 3,100 watts.
Related Content
-
Industrializing additive manufacturing in the defense/aerospace sector
GA-ASI demonstrates a path forward for the use of additive technologies for composite tooling, flight-qualified parts.
-
The next evolution in AFP
Automated fiber placement develops into more compact, flexible, modular and digitized systems with multi-material and process capabilities.
-
Hybrid process marries continuous, discontinuous composites design
9T Labs and Purdue applied Additive Fusion Technology to engineer a performance- and cost-competitive aircraft bin pin bracket made from compression-molded continuous and discontinuous CFRTP.