Thermwood's LSAM 1010 offers lower-cost, walled large-scale additive option
The LSAM 1010 uses the walls from the company’s larger LSAM systems with the gantry, control and sub-systems from the similarly-sized LSAM MT.
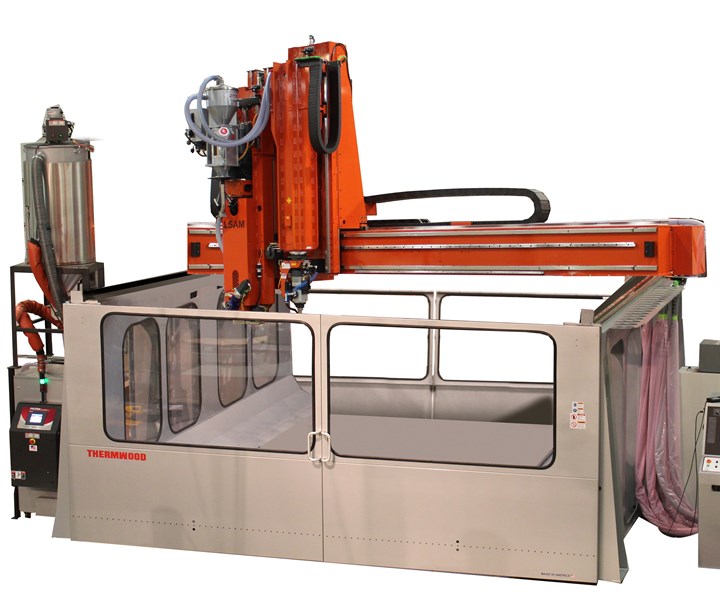
LSAM 1010. Source | Thermwood
Based on demand from customers, CNC machinery manufacturer Thermwood (Dale, Ind., U.S.) has developed the LSAM 1010, a lower-cost enclosed version of its large scale additive manufacturing (LSAM) system. The LSAM 1010 uses the walls from the company’s larger LSAM systems with the gantry, control and sub-systems from the similarly-sized LSAM MT.
The LSAM 1010 features a fixed 10- by 10-foot table. A single moving gantry carries both the print and trim heads as on the MT and, like the MT, it can both print and trim, though not at the same time. The print and trim heads on all Thermwood LSAMs are the same, and are said to be able to process virtually any reinforced composite thermoplastic materials.
Although the LSAM 1010 is slightly higher in price than the MT, it is lower in price than the larger LSAMs and generally less than the cost and complexity of trying to add an external enclosure to the MT, Thermwood says.
In addition, even though the LSAM 1010 is slightly wider than the larger LSAMs to accommodate mounting both the print and trim heads on the same gantry, the overall footprint of the 1010 is slightly smaller than required for the MT. Like the MT, the 1010 can be purchased as a print only machine.
Thermwood believes that, since it is enclosed like the larger LSAMs, the LSAM 1010 can be built to meet European CE requirements, like its larger machines.
Related Content
-
Bladder-assisted compression molding derivative produces complex, autoclave-quality automotive parts
HP Composites’ AirPower technology enables high-rate CFRP roof production with 50% energy savings for the Maserati MC20.
-
Plant tour: Spirit AeroSystems, Belfast, Northern Ireland, U.K.
Purpose-built facility employs resin transfer infusion (RTI) and assembly technology to manufacture today’s composite A220 wings, and prepares for future new programs and production ramp-ups.
-
Hybrid process marries continuous, discontinuous composites design
9T Labs and Purdue applied Additive Fusion Technology to engineer a performance- and cost-competitive aircraft bin pin bracket made from compression-molded continuous and discontinuous CFRTP.