New book covers practical issues associated with resin infusion processes
Author details the mechanics of materials for the construction of laminates manufactured with the aid of pressure, computer simulations and infusion strategies and more.
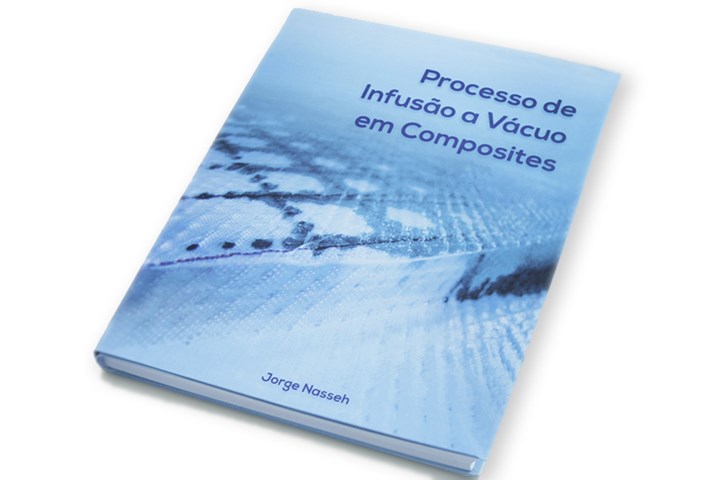
Photo Credit: Barracuda Group
Jorge Nasseh, CEO of Barracuda Group (Bellaire, Texas) is launching the first edition of “Resin Infusion Processing in Composites” (Processo de Infusão a Vácuo em Composites). As the recipient of numerous international scientific awards and the author of several books in the field of composite engineering, the author draws on an extensive technical background, combined with insight into the practical issues associated with state-of-the-art resin infusion processes.
Jorge Nasseh specifies, in more than 400 pages, the details of material selection for vacuum-assisted composite construction, the physics and history of the process, computer simulation and infusion strategies, permeability testing and calculation. The first edition of this volume is preceded by two prefaces: the first, written by SAMPE Global Technical Director, Dr. Scott Beckwith, and the second by Owens Corning Global Composite President, Marcio Sandri (Toledo, Ohio, U.S.)
Jorge Nasseh is also the author of “Boat Construction Manual in Composites,” “Advanced Methods in Composite Construction” and “Theory and Practice of Composite Construction.” All books were written in Brazilian Portuguese.
Paper back copies are available at . The e-book can be downloaded via and previewed at Google Books.
Related Content
-
Low-cost, efficient CFRP anisogrid lattice structures
CIRA uses patented parallel winding, dry fiber, silicone tooling and resin infusion to cut labor for lightweight, heavily loaded space applications.
-
Carbon fiber satellite arm reduces weight, simplifies assembly onto naval vessels
Satcom developer EM Solutions partnered with ACS Australia to replace an aluminum arm design with a 65% lighter, one-piece, corrosion-resistant carbon fiber/epoxy alternative.
-
Clean Sky 2 outer wing box demonstrator validates OOA LRI, shimless assembly and SHM
Full-scale wing box project achieves TRL 5 with 2% weight reduction and 4% reduction in recurring production costs through improved manufacturing efficiency and assembly processes.