Matsumoto Fine Chemical unveils solution for efficient infusion process with one-part epoxy resins
New one-part epoxy resin X-1366R shows very low viscosity and can be easily impregnated to reinforcing fibers at room temperature without resin/hardener mixing process.
Figure 1. Impregnation results comparing commercially available two-part epoxy resins for RTM and X-1366R. Photo Credit, all images: Matsumoto Fine Chemical
(Ichikawa, Japan) has developed a novel one-part thermosetting epoxy resin X-1366R for composite infusion processes. It does not require pre-mixing and can impregnated fibers quickly due to its low viscosity at room temperature. These attributes lead to better quality stability and processability when compared to two-part thermoset resins.
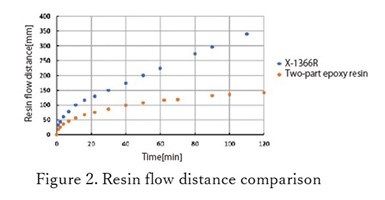
Figure 2. Resin flow distance comparison.
Tests show that X-1366R exhibited more than twice the resin flow distance of commercially available two-part epoxy resins for RTM, as well as high impregnation properties. Fig. 1 above illustrates impregnation results comparing commercially available two-part epoxy resin for RTM and X-1366R. In a +45/-45 carbon fiber/T700S laminate configuration, viscosity of the two-part epoxy resins was 295 mPaï½¥s (23.6ºC), while the X-1366R was 93.3 mPaï½¥s (24.6ºC). Fig. 2 at right compares their resin flow distance.
A comparison of the carbon fiber-reinforced polymer (CFRP) properties with X-1366R or commercially available two-part epoxy resins showed no significant differences and comparable performance, as seen below.
CFRP with available two-part epoxy resin for RTM |
CFRP with X-1366R |
|
Tensile strength [MPa] |
2100 |
2070 |
Tensile modulus [GPa] |
119 |
112 |
Breaking strain [-] |
1.83 |
1.73 |
Based on these results, Matsumoto says its novel one-part resin can be applied as a matrix resin for large CFRP/GFRP structural parts made by the infusion method.
In order to expand X-1366R’s application, the company plans to obtain additional engineering data such as the possibility of curing at lower temperatures and in shorter time, and material properties like flexural modulus, which will be reported on in the future.
Related Content
-
Low-cost, efficient CFRP anisogrid lattice structures
CIRA uses patented parallel winding, dry fiber, silicone tooling and resin infusion to cut labor for lightweight, heavily loaded space applications.
-
A new era for ceramic matrix composites
CMC is expanding, with new fiber production in Europe, faster processes and higher temperature materials enabling applications for industry, hypersonics and New Space.
-
Combining multifunctional thermoplastic composites, additive manufacturing for next-gen airframe structures
The DOMMINIO project combines AFP with 3D printed gyroid cores, embedded SHM sensors and smart materials for induction-driven disassembly of parts at end of life.