Markforged launches software to scale additive manufacturing
Called Eiger Fleet, new cloud-based software enables more control and automation in connection with Markforged 3D printers.
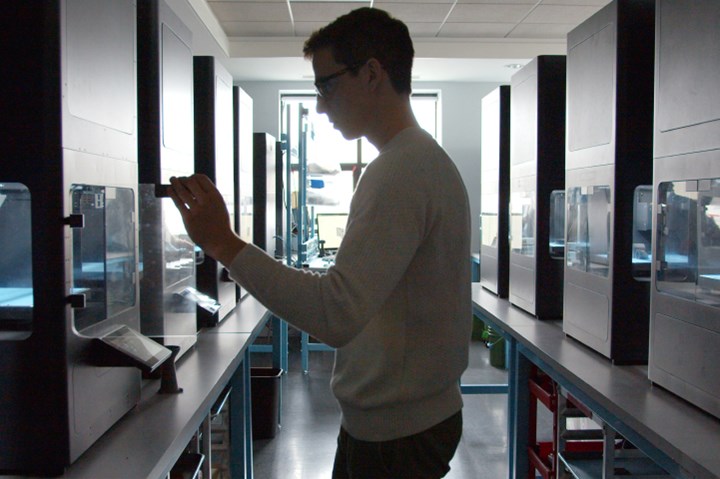
Eiger Fleet, part of Markforged’s (Watertown, Mass., U.S.) Eiger software portfolio, is a cloud-based software solution designed to help companies scale up additive manufacturing (AM) operations.
Available as a paid subscription on all Markforged printers, Eiger Fleet is said to help automate business processes through integrations with a company’s existing enterprise systems to expand access to Markforged’s Digital Forge platform across their entire business. For organizations looking to scale their AM capabilities, Eiger Fleet offers enterprise level features to manage users, devices and data with greater control and efficiency to print parts on demand at the point of need.
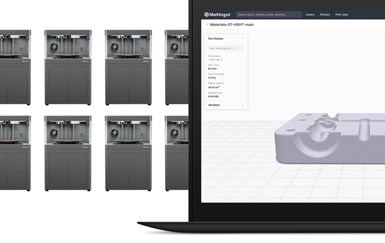
Eiger Fleet is designed to enable customers to:
- Control which part, build, devices, print operations and data are accessible to users according to job responsibilities and privileges by leveraging role-based access control (RBAC)
- Provide frictionless user and administrator experience through SAML Single Sign-On (SSO), where automated account provisioning reduces IT costs and easily and consistently enforces strong access policies with identity protection
- Connect, simplify and automate workflows with Eiger API, connecting their AM processes to their existing enterprise software systems
- Seamlessly manage their entire digital inventory of parts, leveraging batch operations and organization-wide presets
- Easily track, analyze and share key performance indicators of time and cost savings from AM.
According to Markforged, Vestas Wind Systems A/S (Aarhus, Denmark) uses Eiger Fleet to manage the production of parts and tools for their global fleet of wind turbines using Markforged 3D printers.
Related Content
-
Industrializing additive manufacturing in the defense/aerospace sector
GA-ASI demonstrates a path forward for the use of additive technologies for composite tooling, flight-qualified parts.
-
Sulapac introduces Sulapac Flow 1.7 to replace PLA, ABS and PP in FDM, FGF
Available as filament and granules for extrusion, new wood composite matches properties yet is compostable, eliminates microplastics and reduces carbon footprint.
-
Bladder-assisted compression molding derivative produces complex, autoclave-quality automotive parts
HP Composites’ AirPower technology enables high-rate CFRP roof production with 50% energy savings for the Maserati MC20.