Edge Solutions, Ineos Styrolution armourEDGE shield protects against leading-edge erosion
Onshore and offshore operational wind farms’ interactions with a range of environmental factors often lead to blade damage. ArmourEDGE improves wind blade aerodynamics, durability and reduces downtime.
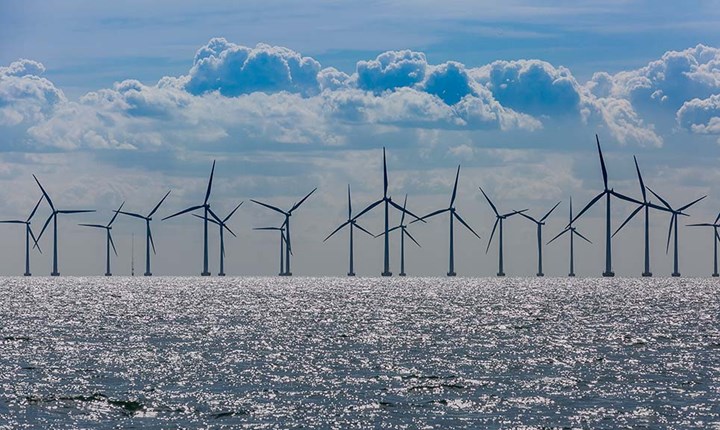
Photo Credit: Ineos Styrolution
Styrenics company (Frankfurt, Germany) and Edge Solutions (Dundee, Scotland) an innovator dedicated to the optimization of wind energy generation, announce the development of armourEDGE to protect against leading-edge erosion on wind turbine blades. The shield solution is based on a customized version of Ineos Styrolution’s Luran SC material, which is comprised of blended acrylonitrile styrene acrylate (ASA) with polycarbonate (PC), making it inherently robust, stiff, strong, oxidation-stable and resistant to high heat.
Leading-edge erosion, common with large commercial wind turbine blades —and more so with offshore windfarms as installations increase — is caused by a variety of environmental factors including rain, hail, ice, salt and UV light. Such damage to the blade surface can lead to increased drag and ultimately to reduced energy production, Ineos says. It also drives operating cost up due to increased maintenance, regular blade replacement and downtime of the generator.
Ineos Styrolution says it specifically developed its Luran SC product based on specifications defined by Edge Solutions. The basis for the armourEDGE shield, it aids in reducing downtown and maintenance cost. It also results in an increase in annual energy production.
The armourEDGE system is currently being installed on an operational offshore wind farm in northern Europe.
Related Content
-
Polar Technology develops innovative solutions for hydrogen storage
Conformable “Hydrogen in a Box” prototype for compressed gas storage has been tested to 350 and 700 bar, liquid hydrogen storage is being evaluated.
-
Trends fueling the composites recycling movement
Various recycling methods are being considered for composites, from novel dismantling and processing, to building capacity and demonstrating secondary use applications.
-
SRI develops scalable, infiltration-free ceramic matrix composites
Work in two DOE projects is demonstrating C/C-SiC produced in 3-5 days with <5% shrinkage, <10% porosity and 50% the cost of conventional C/C and C/C-SiC.