CAMX 2021 exhibit preview: A&P Technology
A&P Technology’s new product offerings include slit tape thermoplastic fabrics that can be braided into fabrics up to 60 inches wide.
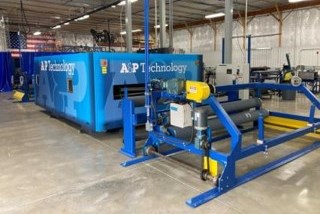
A&P Technology (Cincinnati, Ohio, U.S.) showcases new product offerings that enable rapid cycle times, including slit tape thermoplastic fabrics, powder coating and lamination capabilities.
Slit thermoplastic tapes can be braided into fabrics up to 60” wide, the company says. These fabrics can have biaxial or triaxial architectures, or a combination of the two, to selectively locate reinforcement. Braided thermoplastic tape options include PEEK, PAEK, PEKK and PPS, and are also available as sleevings and preforms.
To provide additional value to its braided products, A&P says it has dedicated a Value Added Processes (VAP) building with powder coating capabilities, which reportedly provides better handling, improved cutting and easier preforming. A&P is currently powder coating materials for automotive applications.
In addition to a powder coater, A&P installed a laminator at VAP enabling the application of films such Spunfab veils, and the combination of multiple layers of fabric.
A&P Technology brands its 0°, ±45° fabric offerings as Triax45. Triax45 offers both bending stiffness provided by the 0° fibers and in-plane shear response due to the 45° orientation. Similar to A&P’s other fabric offerings, the Triax45 architecture can be produced using a variety of carbon fiber types and the percentage of axial or off-axis 45° content can vary to optimize the mechanical requirements for specific applications.
Related Content
-
AGY, A+ Composites launch fiberglass thermoplastic tape line
Unidirectional S2 glass fiber reinforced with LM-PAEK and PEI boosts mechanical and thermal and sustainability properties for wrapped and layered composite applications.