CAMX 2021 exhibit preview: Airborne
Airborne’s integrated automated kitting system can pick composites plies directly from the conveyor cutter to sort, sequence and store them in a compact and fast buffer station.
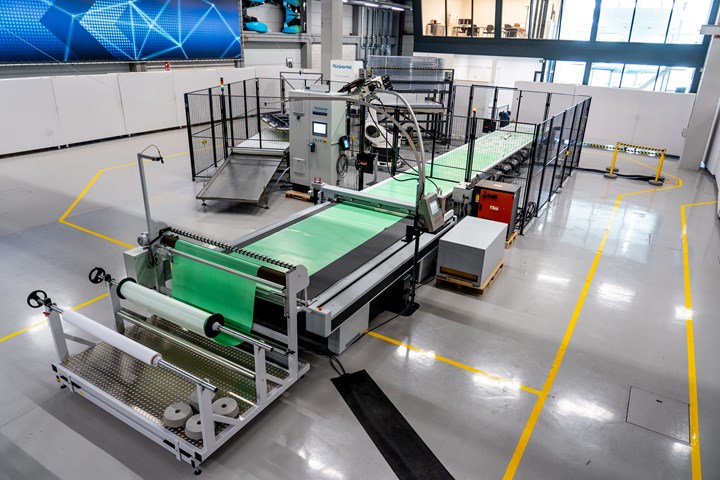
Airborne (The Hague, Netherlands) introduces its latest automated solution for composites manufacturing. The plug-and-play, integrated automated kitting system can pick composite plies directly from the conveyor cutter to sort, sequence and store them in a compact and fast buffer station. Airborne claims that the fully automated and digital system provides composite part producers a robust, flexible and efficient process to convert material rolls into sorted and sequenced ply kits.
A conveyorized ply cutter is integrated to accurately cut the plies to the required shape. The ply handling system comprises of an industrial robot and a proprietary pick-and-place technology to safely separate the plies from the nest without distortion. The system is capable of handling thermoset prepreg, thermoplastic prepreg, dry fibers and consumables (such as foils, resin films and more). The buffer station is capable of storing up to 1,200 plies of up to 2.5 x 1.27 m (98 x 50″) over 40 trays, providing compact storage.
The system also features Airborne’s automated programming technology that eliminates the need for programming the system. Rather, says the company, the system only needs the nesting file and kit information as input and creates all machine instructions automatically and on-the-fly. Airborne claims this enables dynamic nesting and ensures the system is adaptive to the operational needs and possible changes in the design of composite parts.
Related Content
-
Aerospace prepregs with braided reinforcement demonstrate improved production rates, cost
A recent time study compares the layup of a wing spar using prepreg with A&P’s TX-45 continuous braided reinforcement versus traditional twill woven prepreg.
-
Plant tour: Airbus, Illescas, Spain
Airbus’ Illescas facility, featuring highly automated composites processes for the A350 lower wing cover and one-piece Section 19 fuselage barrels, works toward production ramp-ups and next-generation aircraft.
-
Reducing accidental separator inclusion in prepreg layup
ST Engineering MRAS discusses the importance of addressing human factors to reduce separator inclusion in bonded structures.