ZeroAvia begins U.S. 19-seat hydrogen-electric aircraft testing, demonstration program
The company will expand its U.S. base to test new components for the ZA600 hydrogen-electric powertrains, with second Dornier 228 aircraft to be retrofitted and tested in the coming months.
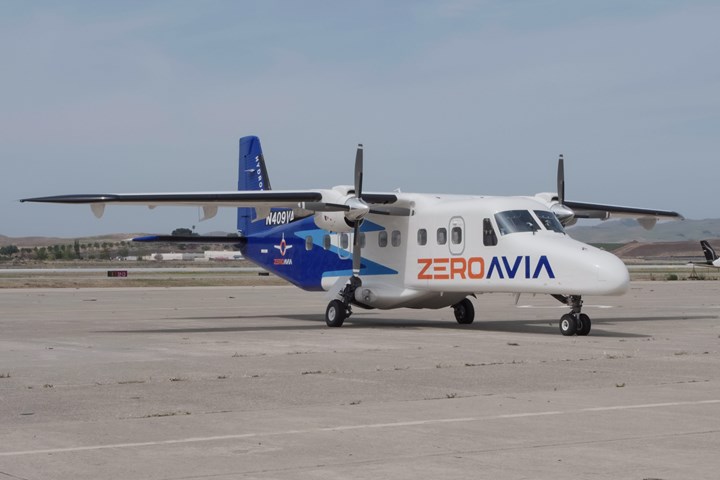
Dornier 228 aircraft. Photo Credit: ZeroAvia
(Hollister, Calif., U.S. and Kemble, U.K.) has received its second twin-engine 19-seat Dornier 228 aircraft at its headquarters in Hollister, Calif. The new U.S. initiative will take the system developed in the U.K. and integrate it into the same type of aircraft. According to the company, it will serve as the basis for testing new components and integrations, as well as a testbed for working with the Federal Aviation Administration (FAA) ahead of the ZA600 engine’s planned certification in 2024.
“This new project in California will enable us to use architectures from our Hyflyer II initiative, where we are working with the same aircraft, and apply those lessons as we further test and demonstrate the system across a number of different use cases,” Val Miftakhov, CEO and founder of ZeroAvia, says. “Ultimately, this will help us optimize our zero-emission powertrain design ahead of certification. This year, we will have two demonstration aircraft flying on two continents powered by our hydrogen-electric powertrains which will further help us secure partner and customer commitments across the worldwide aviation industry.”
ZeroAvia will work towards a hybrid engine configuration that incorporates both the company's hydrogen-electric powertrain and a conventional engine into the aircraft. The conversion is expected to take approximately three to four months to prepare the aircraft for test flights. After the engine is configured, it will enter into the flight testing and demonstration program, spanning passenger, cargo and industrial use cases with a number of to-be-announced partners.
Progressing the demonstrations of the two Dornier aircraft is said to be an important next step for ZeroAvia’s sequential R&D pathway to realizing transformational possibilities for aviation.
In addition to the launch of this program, ZeroAvia will be expanding its facility at Hollister to ensure adequate staff and resources to reach planned milestones. The company has added a new 15,000-square-foot hangar to its footprint at the airfield, enabling space for conducting engineering work on the aircraft and its HyperTruck test bed platform, as well as ample office space to support its growing operations.
“There is potential for Hollister Municipal Airport to become a hydrogen hub,” Renee Wells, executive director of the economic development corp. (EDC) San Benito County. “There will be significant demand and since California leads the world in adopting zero-emission vehicles, zero-emission flight infrastructure is the next natural frontier.”
Last fall, ZeroAvia conducted the first of its HyFlyer II program and successfully tested the flight-intent 600-kilowatt powertrain with its 15-ton HyperTruck mobile ground testing platform. The HyperTruck, developed based on heavy-duty military trucks, is sized to also support testing the company’s larger planned powertrain (ZA-2000, with shaft power over 1.8 megawatts) which can be used to test systems for 40-80 seat aircraft.
The HyFlyer II Project is co-funded by a £12.3 million ($16.3 million) grant through the UK Government’s ATI Programme. Progressing the demonstrations of the two Dornier aircraft is said to be an important next step for ZeroAvia’s sequential R&D pathway to realizing the transformational possibilities of moving from fossil fuels to zero-emission hydrogen as the primary energy source for commercial aviation.
In the last quarter of 2021, ZeroAvia secured partnerships and funding with major airlines Alaska Air Group and United Airlines to accelerate the development of its ZA2000 engine, the largest of ZeroAvia's powertrain platforms, capable of producing between 2,000 and 5,000 kilowatts. The company also recently announced its latest partnership with ZEV Station (see “ZeroAvia, ZEV Station gear up hydrogen refueling ecosystem at California airports”) where the two will collaborate to develop hydrogen refueling infrastructure at airports in California. ZeroAvia was also just named as a Bloomberg NEF Pioneer for its efforts to decarbonize aviation.
Related Content
Plant tour: Collins Aerospace, Riverside, Calif., U.S. and Almere, Netherlands
Composite Tier 1’s long history, acquisition of stamped parts pioneer Dutch Thermoplastic Components, advances roadmap for growth in thermoplastic composite parts.
Read MoreFirst Airbus A350 crash confirmed in Haneda
Shortly after touch-down, a JAL A350-900 aircraft recently collided with a De Havilland Canada Dash 8. Exact circumstances are still unknown.
Read MoreInfinite Composites: Type V tanks for space, hydrogen, automotive and more
After a decade of proving its linerless, weight-saving composite tanks with NASA and more than 30 aerospace companies, this CryoSphere pioneer is scaling for growth in commercial space and sustainable transportation on Earth.
Read MoreA new era for ceramic matrix composites
CMC is expanding, with new fiber production in Europe, faster processes and higher temperature materials enabling applications for industry, hypersonics and New Space.
Read MoreRead Next
Bye Aerospace all-electric eFlyer 800 program advances
Production backlog reaches 135 purchase deposits and option agreements, approaching a total of 900 units in backlog.
Read MoreAll-recycled, needle-punched nonwoven CFRP slashes carbon footprint of Formula 2 seat
Dallara and Tenowo collaborate to produce a race-ready Formula 2 seat using recycled carbon fiber, reducing CO2 emissions by 97.5% compared to virgin materials.
Read MoreVIDEO: High-volume processing for fiberglass components
Cannon Ergos, a company specializing in high-ton presses and equipment for composites fabrication and plastics processing, displayed automotive and industrial components at CAMX 2024.
Read More