Vertical Aerospace partners with GKN Aerospace on wing structure for VA-X4 eVTOL
GKN will deliver wing structures and wiring systems for the composites-intensive, zero-emissions aircraft.
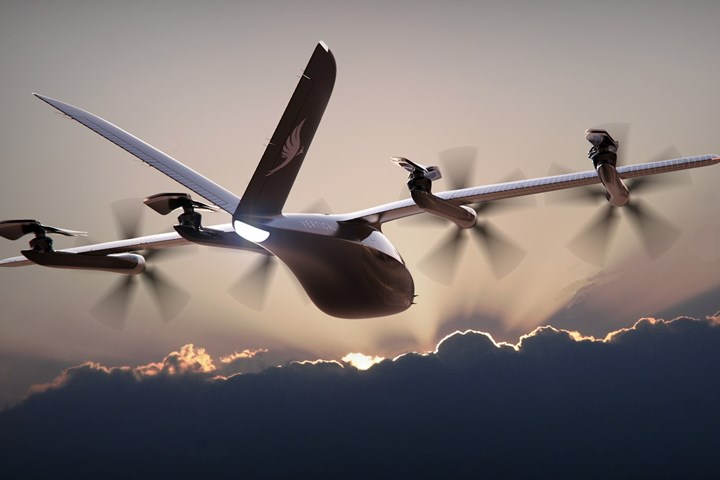
A rendering of the VA-X4. Photo Credit: Vertical Aerospace
On Sept. 17, electric vertical takeoff and landing (eVTOL) vehicle manufacturer Vertical Aerospace (Bristol, U.K.) announced a developed and production agreement with GKN Aerospace (Redditch, U.K.) for the wing structures and wiring system on Vertical’s aircraft. The zero-emissions VA-X4 is said to have a carbon fiber composite airframe and custom-designed wings.
Vertical plans to benefit from GKN Aerospace’s experience in aerostructures design and manufacture for leading commercial and defense aircraft, track record with safety and certification and 41 manufacturing locations across 13 countries. GKN Aerospace’s wing structures and wiring are expected to lead to a VA-X4 aircraft with higher performance; lower manufacturing costs, weight and emissions; a secure path to certification; global production; and shorter production times and lower unit costs.
GKN Aerospace joins Vertical’s ecosystem of partners including Solvay (Brussels, Belgium), Rolls-Royce (London, U.K.), Honeywell (Phoenix, Ariz., U.S.) and Microsoft (Redmond, Wash., U.S.).
Stephen Fitzpatrick, founder and CEO at Vertical, says, “We are delighted that [GKN Aerospace is] joining our unrivalled partner ecosystem. Their expertise in producing aerospace systems and structures will help the VA-X4 to meet the stringent safety standards mandated by the CAA and EASA, an essential step forward in our efforts to electrify flight.”
John Pritchard, president of GKN Aerospace’s Civil business, says, “The rapid progress being made towards electric aircraft is a game-changer for the industry. GKN Aerospace has decades of experience as a leader in both aerostructures and EWIS and we are excited to use that expertise to accelerate the transition to more sustainable aviation. Vertical has a great vision and we are proud that our technology can help bring that to reality and shape the future of flight.”
Related Content
-
Al Seer Marine, Abu Dhabi Maritime unveil world’s largest 3D-printed boat
Holding the new Guinness World Record at 11.98 meters, the 3D-printed composite water taxi used a CEAD Flexbot to print two hulls in less than 12 days.
-
Partners recycle A350 composite production waste into adjustable-length rods for MFFD
Herone, Spiral RTC, Teijin Carbon Europe and Collins Aerospace Almere recycle A350 thermoplastic composite clips/cleats waste into rods for the all-thermoplastic composite Multifunctional Fuselage Demonstrator’s crown.
-
Natilus announces Horizon blended wing body CFRP aircraft for 200-passenger narrowbody market
Following its Kona cargo aircraft with 460 pre-orders, this larger all-CFRP model responds to airlines’ request to fill Boeing and Airbus gap with 25% less weight, 40% greater capacity and 50% less carbon emissions, to enter service by early 2030s.