Suprem expands thermoplastic capabilities
A tailored combination of fiber reinforcement and high-performance thermoplastics can now be processed with this technology to fulfill applications from marine to aerospace.
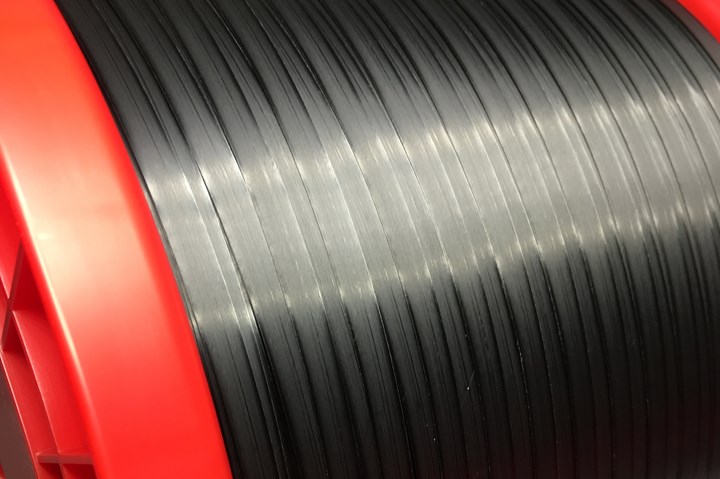
Photo Credit: Suprem
Suprem’s (Yverdon-les-Bains, Switzerland) thermoplastic towpreg technology will now support large-scale, automated additive manufacturing of composite parts.
According to Suprem, machinery and process innovations have been industrialized to produce an important quantity of high-quality unidirectional (UD) tapes and profiles.
Suprem says its continuous fiber0reinforced thermoplastic tapes and profiles are dedicated to tape winding for the manufacture of pipes and tanks with high burst pressure, tape placement of parts with in-situ consolidation and 3D printing of complex and light components.
A tailored combination of fibers (carbon, glass and aramid) and high-performance thermoplastics (from PA to PEEKs) can now be processed with this technology to fulfill customers’ needs in applications from marine to aerospace.
Dr. Anatole Gilliot, CEO of Suprem, says, “I am glad we could implement Suprem’s ideas into our thermoplastic towpreg technology. This allows us to ramp up our manufacturing capacity while still offering our customers high-quality products for automated processing. I am thankful to Suprem’s shareholders and our partners [and] suppliers who have been supporting our evolution over the years.”
Related Content
-
Multi-material, self-sensing, 3D-printed scoliosis braces
Startup Fited and Brightlands Materials Center have developed a lighter weight, thinner CFRP corrective brace, including pressure sensors made from continuous carbon fibers.
-
Combining multifunctional thermoplastic composites, additive manufacturing for next-gen airframe structures
The DOMMINIO project combines AFP with 3D printed gyroid cores, embedded SHM sensors and smart materials for induction-driven disassembly of parts at end of life.
-
Hybrid process marries continuous, discontinuous composites design
9T Labs and Purdue applied Additive Fusion Technology to engineer a performance- and cost-competitive aircraft bin pin bracket made from compression-molded continuous and discontinuous CFRTP.