Shellfish inspire chemists to develop stronger, more sustainable adhesives
Purdue University’s Jonathan Wilker studies the natural underwater adhesion of animals like shellfish to develop adhesives that are strong, sustainable, are made from food products and work underwater.

Wilker notes that not everyone in his lab has a chemistry degree; some of the lab members are shellfish — about 1,000 of them. The shellfish play a valuable role by demonstrating how they make adhesives so that scientists can build upon their biological strategies. Photo Credit: Purdue University, Rebecca McElhoe
Purdue University’s (Lafayette, Ind., U.S.) Jonathan Wilker, professor of chemistry and materials engineering, is pursuing a study on shellfish to help develop new adhesives that work underwater, are stronger, and more sustainable, are made from food products and that can be un-stuck when needed. The professor was initially inspired by the shellfish that have been clinging to the ocean rocks for eons, reportedly by a natural adhesives that tends to be stronger and more durable than anything developed by humans.
“We start by looking at animals that make adhesives,” Wilker says. “We’re still working to understand the fundamentals of how animals like mussels and oysters do what they do, how the chemistry and engineering work together. We are even seeing how the environment around them and the surface they’re sticking to influences what they do.”
Critters such as barnacles, mussels and oysters live in places where they are continually battered by waves and wind and pried at by potential predators. Their very lives depend on being able to cling to rocks and their neighboring shellfish.
Further, sutures, screws and staples are all widely used to close wounds, bind tissues and set bones, but they are all very damaging and extremely painful. If doctors had a chemical adhesive that they could use instead, Wilker believes, healing would increase and collateral damage would decrease. However, the body is a challenging environment for adhesives: wet and constantly in motion. A lot like the sea.
Scientists in Wilker’s lab — which includes two postdoctoral researchers, five graduate students, four undergraduate researchers and 1,000 shellfish — have been studying how shellfish create materials, what components of the adhesives play active roles in bonding and test new synthetic and biomimetic glues to determine their efficacy, feasibility and performance. Within the same lab, Wilker and his team are also working to make glues out of .
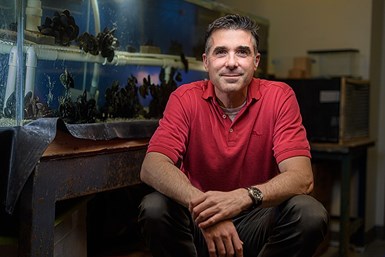
Jonathan Wilker, professor of chemistry, studies shellfish to develop adhesives that are more sustainable and stronger, and work in a wider range of environments than current adhesives. Photo Credit: Purdue University photo, Rebecca McElhoe.
“We’re making adhesives with new functionalities,” Wilker says. “We can add in new chemical groups to target all sorts of properties, be that wet bonding, rubber-like flexibility or the ability to bond and then de-bond. One of our systems can even be stronger than what the animals make underwater. In that case, we are using chemistry that is inspired by the shellfish but, overall, our system is a simplification of what the animals produce.”
Overall, increasing the sustainability and the functionality of adhesives may improve human life in a myriad of ways, by limiting exposure to harmful chemicals, by making healing more comfortable and by making products more sustainable and more recyclable to preserve resources and the planet.
“Almost every common glue is petroleum-based and not degradable,” Wilker says. “When your laptops or cell phones, shoes or furniture are no longer needed, most of them go straight to a landfill. Even materials like cardboard often do not get recycled because of the adhesives.”
Adhesion is a rapidly evolving field with huge potential, according to the university. It’s a field in which , thanks to a stray thread of curiosity encountered in the ocean.
“The core ideas in our lab come from spending time underwater,” Wilker says. “I was scuba diving, saw shellfish sticking to rocks and thought, ‘I wonder how that works.’ When I got back into the lab, I was surprised to learn about what remained unknown. There are so many exciting possibilities and applications to pursue if we can figure it all out.”
As both a professor of chemistry in the College of Science and a professor of materials engineering, Wilker is said to bridge the worlds of science and engineering in his efforts to tap the natural world for innovative solutions to adhesion problems. The Office of Naval Research and the National Science Foundation help fund his research.
Wilker has worked with the Purdue Research Foundation Office of Technology Commercialization to apply for patents on his adhesives from the U.S. Patent and Trademark Office. He is starting to make them commercially available through commercial ventures including a startup, . (Bethlehem, Penn., U.S.).
Related Content
Watch: A practical view of sustainability in composites product development
Markus Beer of Forward Engineering addresses definitions of sustainability, how to approach sustainability goals, the role of life cycle analysis (LCA) and social, environmental and governmental driving forces. Watch his “CW Tech Days: Sustainability” presentation.
Read MoreComposites end markets: Sports and recreation (2025)
The use of composite materials in high-performance sporting goods continues to grow, with new advancements including thermoplastic and sustainability-focused materials and automated processes.
Read MorePlant tour: Arris Composites, Berkeley, Calif., U.S.
The creator of Additive Molding is leveraging automation and thermoplastics to provide high-volume, high-quality, sustainable composites manufacturing services.
Read MoreBladder-assisted compression molding derivative produces complex, autoclave-quality automotive parts
HP Composites’ AirPower technology enables high-rate CFRP roof production with 50% energy savings for the Maserati MC20.
Read MoreRead Next
Easy-to-use kits enable infield repair of composite structures
Portable kit enables patch repairs using UV-cure glass fiber/vinyl ester or room-temp stored carbon fiber/epoxy prepregs and battery-powered curing equipment.
Read MorePurdue University to establish Thermwood LSAM research laboratory
Industry-funded research to pursue large-scale composite thermoplastic additive manufacturing, with the goal of providing services to enhance, encourage and expand the adoption of large-scale AM for diverse industrial applications.
Read MoreComposites end markets: New space (2025)
Composite materials — with their unmatched strength-to-weight ratio, durability in extreme environments and design versatility — are at the heart of innovations in satellites, propulsion systems and lunar exploration vehicles, propelling the space economy toward a $1.8 trillion future.
Read More