SGL Carbon to build composite battery enclosures for North American automaker
The company will produce carbon and glass fiber-based composite top and bottom layers for battery enclosures.
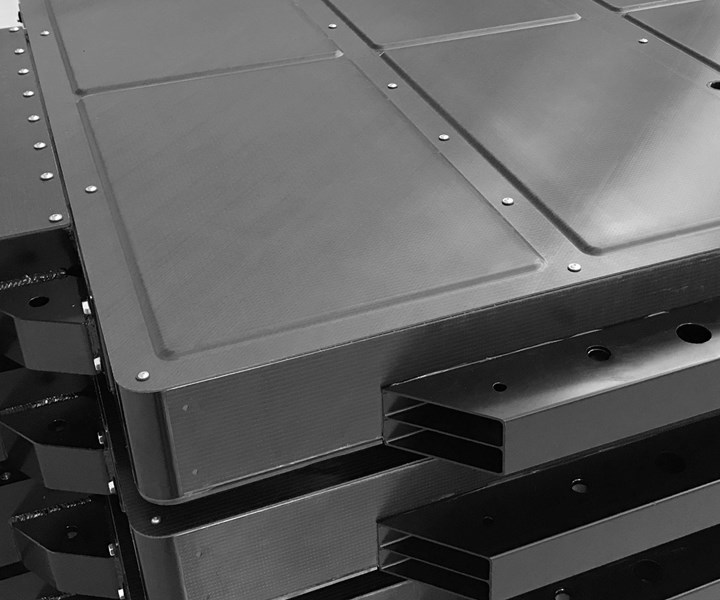
Source | SGL Carbon
SGL Carbon (Wiesbaden, Germany) reported on Jan. 13 that it has received a contract from a North American automaker for high-volume serial production of carbon and glass fiber-based composite top and bottom layers for battery enclosures, with production expected to begin the end of this year. The carbon fibers and fabrics, and the assembled components, will come from SGL Carbon’s fully integrated value chain.
The battery enclosure is a key part of an electric car’s chassis platform, the company says. Typically, this enclosure occupies most of the space in the underfloor of the chassis, and has specific requirements for weight, stiffness, impact protection, thermal management, fire protection, and water and gas impermeability. SGL Carbon says composite materials meet these requirements better than any other materials.
This contract follows the successful production of composite battery case prototypes for Chinese automotive manufacturer NIO announced last year.
The company says there is also the potential for more orders with this manufacturer for even more substantial volumes. In addition, SGL Carbon announces that it has also won a smaller volume contract from a European sports car manufacturer to serially produce bottom layers made of composite, to begin mid-2020, with more potential customers in electric car manufacturing in development.
“Driven by the increasing need for [electric cars] worldwide and thus for new flexible chassis platforms, our composite battery enclosures are a very promising new application in our product portfolio,” says Sebastian Grasser, head of the automotive segment at the Composites – Fibers & Materials business unit at SGL Carbon. “The recent contract wins show that our approach of developing custom-made solutions based on our integrated value chain offers an excellent value proposition.”
Related Content
-
Revisiting the OceanGate Titan disaster
A year has passed since the tragic loss of the Titan submersible that claimed the lives of five people. What lessons have been learned from the disaster?
-
Hybrid process marries continuous, discontinuous composites design
9T Labs and Purdue applied Additive Fusion Technology to engineer a performance- and cost-competitive aircraft bin pin bracket made from compression-molded continuous and discontinuous CFRTP.
-
Low-cost, efficient CFRP anisogrid lattice structures
CIRA uses patented parallel winding, dry fiber, silicone tooling and resin infusion to cut labor for lightweight, heavily loaded space applications.