SGL Carbon delivers composite materials for Airbus Helicopter rotor blades
SGL Carbon’s glass fiber noncrimp fabrics enable the composite rotor blades for the 5 blade Airbus H145 rotor configuration.

Source | Airbus
In August 2019, SGL Carbon (Wiesbaden, Germany) began delivering two special glass fiber noncrimp fabrics for the new version of Airbus Helicopters’ (Marignane, France) model H145. The materials are used in the new helicopter’s five-blade rotor. Developed in close collaboration with Airbus Helicopters, the material has been qualified for the application for the foreseeable future.
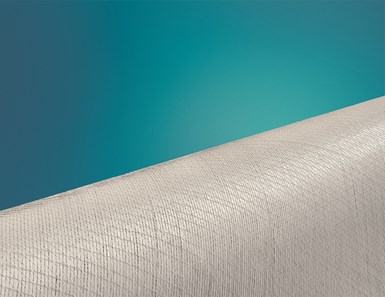
SGL Carbon’s glass fiber noncrimp fabrics enable the composite rotor blades for the 5 blade H145 rotor configuration. Source | SGL Carbon
Because of their unidirectional fiber orientation, the fabrics offer good resistance and support for the new geometry of the especially long H145 rotor blades. The fabrics are manufactured at the SGL Carbon site in Willich near Düsseldorf in a multi-stage process and delivered to Airbus Helicopters in Paris.
“The order emphasizes our growing presence in the aerospace business. With the fabrics for Airbus Helicopters, we have realized, qualified, and started serial production for a material concept for primary structural components for the first time,” says Dr. Andreas Erber, head of the aerospace segment in the business unit Composites – Fibers & Materials at SGL Carbon.
The current deliveries are part of a framework contract with Airbus Helicopters, intended to gradually intensify collaboration.
The new composite 5 blade rotor configuration for the H145 is said to offer 150 kilograms of additional useful load while also enhancing in-flight comfort, simplicity and connectivity.
Related Content
-
Co-molding SMC with braided glass fiber demonstrates truck bed potential
Prepreg co-molding compound by IDI Composites International and A&P Technology enables new geometries and levels of strength and resiliency for automotive, mobility.
-
The potential for thermoplastic composite nacelles
Collins Aerospace draws on global team, decades of experience to demonstrate large, curved AFP and welded structures for the next generation of aircraft.
-
Carbon fiber, bionic design achieve peak performance in race-ready production vehicle
Porsche worked with Action Composites to design and manufacture an innovative carbon fiber safety cage option to lightweight one of its series race vehicles, built in a one-shot compression molding process.