Scheurer Swiss supports ETH Zürich composite hybrid rocket motor development
Company supports the university focus project with its composite engineering know-how and networking capabilities for the production of a third-generation rocket motor that aims to reach an altitude of 30,000 feet.
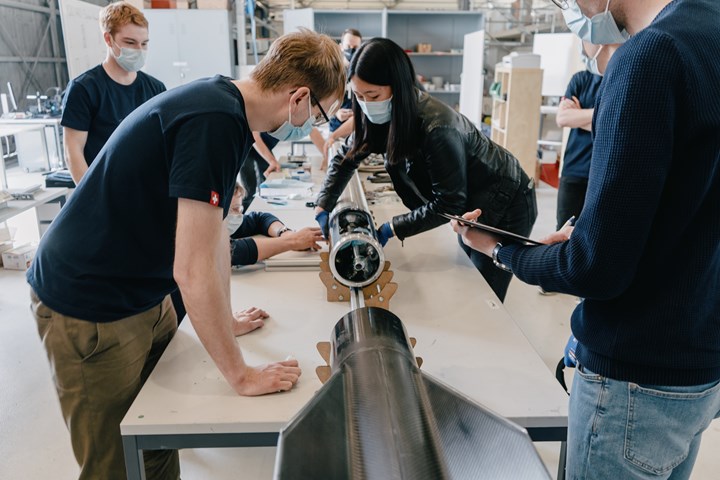
Daedalus team. All photo credit: ARIS
Scheurer Swiss GmbH (Volketswil, Switzerland), a composite company, reported on July 5 that it has supported the , a concept pursued by six mechanical engineering students from public research university ETH Zürich (Switzerland) to produce a lightweight, third-generation hybrid rocket motor for this year’s ARIS Piccard sounding rocket, a launch vehicle designed to take measurements and perform scientific experiments during its suborbital flight. In addition to providing its high-performance composite engineering expertise, Scheurer Swiss helped network the project team with the appropriate companies.
ARIS is a multi-project organization founded in 2017 by students at ETH Zürich to promote spaceflight in Switzerland. Together, budding engineers, scientists and economists have since been developing systems for aerospace with the goal of advancing humanity. The Daedalus project, specifically, aims to use a hybrid rocket motor — which combines a solid fuel with a liquid oxidizer, preventing unintentional ignition — to reach an altitude of 30,000 feet (about 9,150 meters) and win the 2021 Spaceport America Cup in New Mexico, said to be the largest academic rocket engineering competition in the world. The team also expects to compete at EuRoc, said to be the first university rocket launch competition in Europe.
The project kicked off in September 2020, and after the concept and design phase, which is said was supported by valuable input from industry and research experts, the final design of the hybrid rocket motor was in place by December 2020. According to the team, the major challenge of the project has been the integration of the engine into the Piccard rocket, which placed stringent requirements for the engine design. For this reason, the six-member project team worked closely with experts in lightweight construction. To achieve their ambitious goals, Scheurer Swiss, with its many years of experience in composites, was felt to be ideally suited for collaboration.
After an extensive two-month test campaign, during which the performance of the engine in the rocket was tested, the ETH Zürich team reports that its hybrid rocket engine has successfully completed static field testing and is ready for the first hybrid flight.
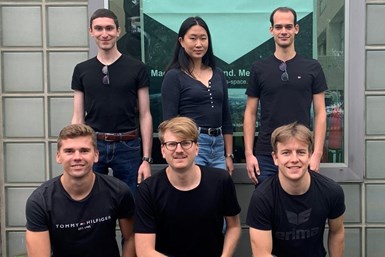
Daedalus team: Julian Frei (top left); Leona Gui (top middle); Severin Meyer (top right); Alex Brandes (bottom left); Adrian Fuhrer (bottom middle); and Aaron Ehrat.
“The course of the entire test campaign was successful and the data collected shows that we are ready for the flight of our engine in the rocket,” says Adrian Fuhrer, hybrid rocket engineer. “The great support that Scheurer Swiss provided us, especially at the beginning of the project, in the field of composite engineering and the networking with other competent partners for lightweight construction and fiber composite technology, was very valuable for us and made the project possible in the first place.”
According to Scheurer Swiss CEO, Dominik Scheurer, the Daedalus project exemplifies how highly efficient technical systems with great potential for success can be developed with the use of fiber-reinforced composite materials and lightweight construction technologies. “We congratulate the Daedalus team on the successful test series and are pleased that we were able to support the team with our engineering expertise and network it with our partner companies in a target-oriented manner,” Scheurer says.
The hybrid rocket motor is expected to perform its first maiden flight in July.
Related Content
Corebon induction heating
This sidebar to CW’s August 2024 feature article reviews this technology for more efficient composites manufacturing and why it aligns with Koridion active core molding.
Read MoreTesting to support composite bolted joint analysis
An overview of ASTM Standard Guide D8509, and its coupon-level mechanical testing of design properties for analyzing composite bolted joints.
Read MoreAurora reveals latest SPRINT X-Plane design concept
An Aurora and Boeing team advances its high-speed, vertical lift concept to the preliminary design phase, which features three lift fans, a more refined composite exterior and an uncrewed cockpit.
Read MoreImproving carbon fiber SMC simulation for aerospace parts
Simutence and Engenuity demonstrate a virtual process chain enabling evaluation of process-induced fiber orientations for improved structural simulation and failure load prediction of a composite wing rib.
Read MoreRead Next
Autonomous agricultural robot supported by composite components
3D-printed carbon fiber-filled composite components enable a robotic weeding system prototype intended to replace use of chemical herbicides.
Read MorePlant tour: Daher Shap’in TechCenter and composites production plant, Saint-Aignan-de-Grandlieu, France
Co-located R&D and production advance OOA thermosets, thermoplastics, welding, recycling and digital technologies for faster processing and certification of lighter, more sustainable composites.
Read MoreAssembling the Multifunctional Fuselage Demonstrator: The final welds
Building the all-thermoplastic composite fuselage demonstrator comes to an end with continuous ultrasonic welding of the RH longitudinal fuselage joint and resistance welding for coupling of the fuselage frames across the upper and lower halves.
Read More