Reactivated Israel Aerospace Industries production line resumes F-16 wing deliveries
With the 1980s assembly line fully reopened and refurbished, IAI continues production of the military aircraft’s wings and composite vertical fin.
Share
Read Next
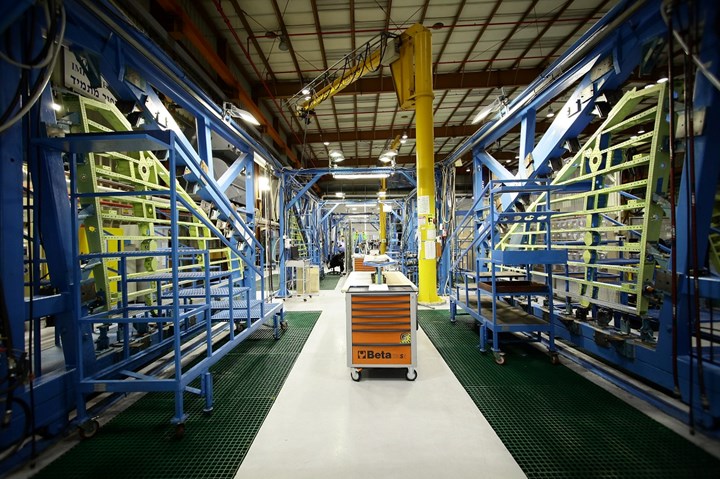
IAI’s F-16 production line. Photo Credit: IAI
Announced by , (IAI, Lod, Israel) has delivered the first F-16 military aircraft wing and composite vertical fin —comprising hand-laid, unidirectional (UD) carbon fiber prepreg and autoclave cure — (Bethesda, Md., U.S.), following the reopening of the F-16 wing assembly line in . As a result of increased worldwide demand for the F-16 Block 70/72, IAI reopened the assembly lines that had been established in the 1980s to continue production of the F-16 aerostructures assembled at the company’s facility. The wings and vertical fins will be shipped to the F-16 production and final assembly line in Greenville, South Carolina.
Prior to reopening the lines, IAI invested in modernizing infrastructure, improving the work environment, and introducing new tools to produce fully compliant F-16 aerostructures. IAI also successfully reestablished the supply chain of hardware suppliers to support the assembly lines, checked and verified tooling, carried out necessary first article inspections and conducted training programs for the F-16 team.
The F-16 wing and vertical fin assembly lines were the first of IAI and Lockheed Martin's collaborations. In addition to wings and vertical fins, IAI also produces the F-16 conformal fuel tanks.
“Built on the newly refurbished and technologically advanced assembly line, the F-16 wing and vertical fins represent over 40 years of cooperation between IAI and Lockheed Martin,” notes Boaz Levy, IAI president and chief executive officer (CEO). “The reactivated F-16 assembly lines join IAI’s aerostructures center of excellence for fighter aircraft.”
Related Content
-
Syensqo composites demonstrate titanium replacement on Boeing MQ-25 Stingray
Validation of integrating Cycom 5250-4HT prepreg into the UAV’s exhaust nozzle structure underpins the material system’s use in other high-temperature aerospace applications.
-
From the CW Archives: Airbus A400M cargo door
The inaugural CW From the Archives revisits Sara Black’s 2007 story on out-of-autoclave infusion used to fabricate the massive composite upper cargo door for the Airbus A400M military airlifter.
-
The AAMMC Tech Hub: Ramping U.S. production of large thermoplastic composite aerostructures
CW talks with Syensqo, Spirit AeroSystems and other consortia members about current funding, specification of the next world’s largest press, organizational structure and projects to support U.S. companies in the race to deliver >40,000 sustainable and efficient aircraft over the next 20 years.