PRF Composite Materials announced as material supplier for ThrustWSH
ThrustWSH aims to set a new water speed record with an innovative, composites-intensive hydroplane design, targeting a 2025/26 run date.
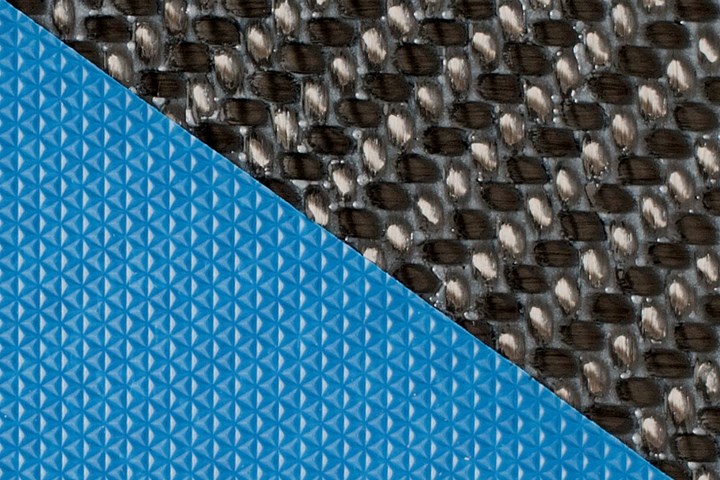
Photo Credit: PRF Composite Materials
PRF Composite Materials (Poole, Dorset, U.K.) announced that it is the prepreg supplier to . Led by Richard Noble OBE and Lorne Campbell, ThrustWSH aims to set a new water speed record, using pioneering research and an innovative design to create a safe and fast hydroplane. The company is targeting an officially ratified two-way average speed of 400+ miles per hour over a measured mile or kilometer.
PRF will be supplying prepreg materials for the fully instrumented data collection model test program portion of the project. This means supporting Supernatural-x in the construction of a concept model — which will be used to promote the project directly to educational and composites industry settings — and then the ¼ scale 240-mile-per-hour operational model. The model program is reported to be essential for building the research and testing to ensure the safety and performance of the full-scale hydroplane.
ThrustWSH hydroplane concept. Photo Credit: ThrustWSH
The build of the ¼-scale model will commence once the research reaches a point where the boat design team are happy to proceed with the design, or to evolve it further; ThrustWSH projects this to be early 2023.
“It is an honor to be selected as material supplier and to be particularly noted for our long-standing history of innovation and technical expertise,” Hannah Khusainova, marketing director at PRF, says. “Over our 40 years, we have led material development in composites, and we are looking forward to being part of a STEM educational project that will have global reach and help inspire the next generations of composite engineers.”
Related Content
-
Carbon fiber composite pallet revolutionizes freight industry
LOG Point Pallet fuses advanced materials with innovative design and manufacturing to improve supply chains worldwide.
-
Low-cost, efficient CFRP anisogrid lattice structures
CIRA uses patented parallel winding, dry fiber, silicone tooling and resin infusion to cut labor for lightweight, heavily loaded space applications.
-
Welding is not bonding
Discussion of the issues in our understanding of thermoplastic composite welded structures and certification of the latest materials and welding technologies for future airframes.