Oribi, Energetic Solutions partner for commercialization of thermoplastic components
The partnership will work together with specification holders within the U.S. DoD to tailor thermoplastic composite materials and components into body armor and vehicle armor systems.
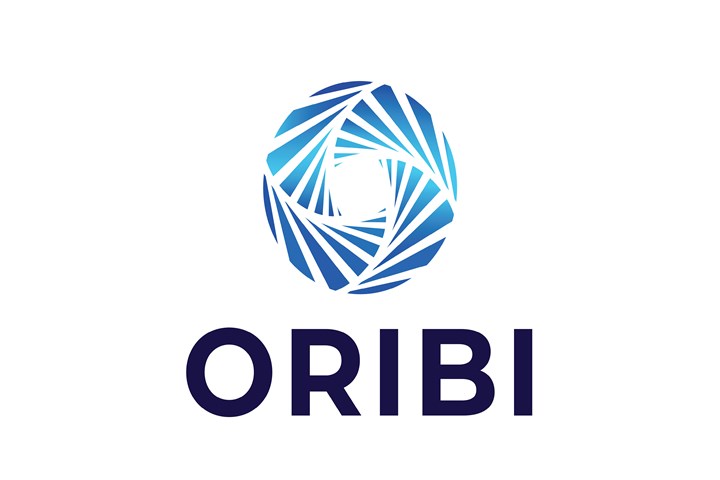
Photo Credit: Oribi
On Oct. 27, Oribi Mfg. (Denver, Colo., U.S.) announced a strategic partnership with Energetic Solutions Inc. (Phoenix, Ariz., U.S.) to develop and commercialize thermoplastic composite components for the U.S. Department of Defense (DoD) law enforcement protective equipment and armor systems. This partnership will focus on engaging with armor system designers and developers to tailor advanced thermoplastic composite materials and components to reduce weight and improve performance of body armor and vehicle armor systems.
Oribi has a steady history of producing a wide range of components for U.S. DoD and law enforcement protective equipment applications. To date, it is reported that the company has produced more than 500,000 structural helmet shells, backing structures, load carriage frames and explosive ordinance disposal suit structures using glass- and carbon fiber-reinforced thermoplastic materials.
“We believe that the work we have done in the protective equipment and armor market over the last 10 years has only scratched the surface on what is possible to accomplish in this market with advanced thermoplastic materials, and with the high speed, automated production processes developed at Oribi,” comments Oribi’s President, Steven Mead. “Energetic Solutions brings armor and protective equipment design expertise, along with a strong understanding of the end-use of these products and is a key partner for Oribi in driving further adoption of thermoplastic materials in this growing segment.”
Scott Stover, Principal at Energetic Solutions, is equally enthusiastic about the application and opportunities for structural thermoplastic materials in this market. “We see tremendous opportunity to help our warfighters, first responder, and law enforcement professionals by improving the durability, reducing the weight and addressing more of the human-factors elements of their protective equipment.”
Oribi and Energetic Solutions will be working closely with the specification holders within DoD, and within the various protective equipment and vehicle OEMs, to introduce continuous fiber-reinforced thermoplastic materials and parts, specifically focusing on improving durability, reducing weight, and optimizing ergonomics for a wide range of hard and soft armor programs.
Contact Scott Stover at Energetic Solutions for technical information at scott@energetic.solutions.
Related Content
-
Plant tour: Teijin Carbon America Inc., Greenwood, S.C., U.S.
In 2018, Teijin broke ground on a facility that is reportedly the largest capacity carbon fiber line currently in existence. The line has been fully functional for nearly two years and has plenty of room for expansion.
-
Plant tour: Airbus, Illescas, Spain
Airbus’ Illescas facility, featuring highly automated composites processes for the A350 lower wing cover and one-piece Section 19 fuselage barrels, works toward production ramp-ups and next-generation aircraft.
-
Carbon fiber, bionic design achieve peak performance in race-ready production vehicle
Porsche worked with Action Composites to design and manufacture an innovative carbon fiber safety cage option to lightweight one of its series race vehicles, built in a one-shot compression molding process.