NCC reaches milestone in composite cryogenic hydrogen program
The National Composites Centre is testing composite cryogenic storage tank demonstrators with increasing complexity, to support U.K. transition to the hydrogen economy.
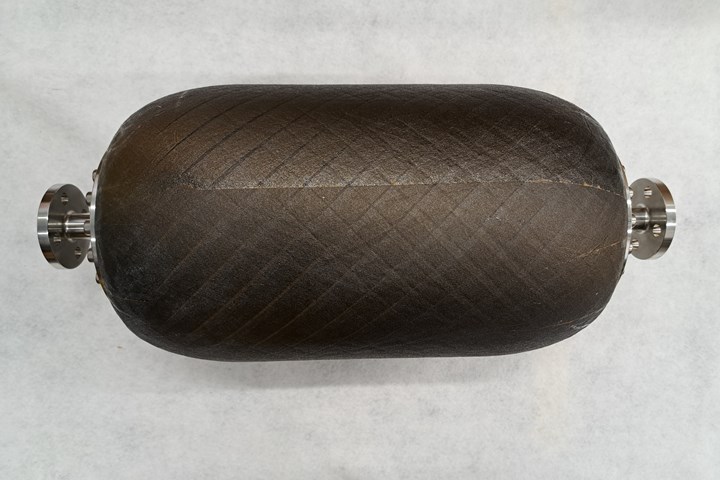
The (NCC, Bristol, U.K.) has announced a U.K.-based composite cryogenic storage tank testing program that will validate and accelerate design, manufacture and test capabilities, starting with a linerless carbon fiber tank for storing liquid hydrogen (LH2).
Cryogenic storage tanks will be essential components in hydrogen-powered aircraft due to come into service in the mid-2030s. Most designs for storing LH2 have centered around metallic tanks, which are relatively heavy. Composite tanks developed in the space industry tend to be suited only for single-use (low-cycle) applications. However, commercial hydrogen aircraft will need fuel tanks to be as light as possible, filled and emptied numerous times (high cycle), and last for several decades.
To support the U.K.’s transition to a low-carbon economy, the NCC is developing underpinning knowledge for composite cryogenic storage tanks and testing by developing product demonstrators with increasing complexity. Its team of specialist engineers have also created and built a range of comprehensive cryogenic concepting and design tools to help UK organizations overcome known engineering challenges critical to accelerating hydrogen development.
With no clear existing industry standards for aerospace cryogenic tanks, the ability to analyze a range of designs is essential. This led to the development of a range of concepting tools covering tank design space exploration, permeability, microcracking, thermal and mechanical stresses. These tools form a baseline toolset that can be used by industry for cryogenic tank projects, enabling detailed design and manufacturing risk identification and analysis. Understanding cryogenics at this fundamental level will enable the NCC to support a wide range of industries and applications, each facing separate but overlapping challenges.
Testing is a crucial part of the cryogenic tank development program, which currently requires access to specialist testing facilities. For example, LH2 requires well-insulated cryogenic storage vessels to maintain it at a temperature of -253°C, and handling requires specialist knowledge and equipment.
To develop a U.K.-based testing capability for its customers, the NCC has partnered with (FSE), a Bristol-based SME specializing in fluid system engineering, that owns and operates a hydrogen test facility capable of both gaseous and liquid hydrogen testing. Working in partnership with FSE, the NCC has developed a tank-testing program that uses an LH2 vacuum test chamber and cryo-rated testing instrumentation. As a world-leading composites research and development center, the NCC has designed and manufactured five linerless carbon fiber demonstrator tanks, using a mix of automated fiber placement (AFP), tape winding, and hand lay-up composite processes. The tanks will be used for the liquid hydrogen testing program, starting at the end of April 2023, with results expected summer 2023.
Daniel Galpin, Advanced Research Engineer, NCC, says, “The cross-sector capability we’ve developed will enable U.K. industry to accelerate and advance engineering expertise in composite cryogenic storage, and secure future commercial competitiveness. Our comprehensive program will enable us to support customers on their journey to design, validate, manufacture, and test high-cycle composite cryogenic tanks.”
The NCC Hydrogen team is collaborating with partners and the supply chain to advance engineering expertise in composite cryogenic storage systems that will help the U.K. to achieve its net-zero ambitions. This builds on NCC’s investment in capability development for hydrogen pressure vessels and hydrogen smart pipes: two other areas that will help establish a strong H2 supply chain as the Government implements its U.K. Hydrogen Strategy to kick-start a vibrant hydrogen economy by 2030. Expertise and knowledge developed through the focus on cryogenics has enormous potential for numerous cross sector applications and will guide technology development.
Related Content
Composites end markets: Energy (2024)
Composites are used widely in oil/gas, wind and other renewable energy applications. Despite market challenges, growth potential and innovation for composites continue.
Read MoreInfinite Composites: Type V tanks for space, hydrogen, automotive and more
After a decade of proving its linerless, weight-saving composite tanks with NASA and more than 30 aerospace companies, this CryoSphere pioneer is scaling for growth in commercial space and sustainable transportation on Earth.
Read MoreZEBRA project demonstrates closed-loop wind recycling system
Consortium partners have proven the complete recycling of thermoplastic wind turbines via two manufactured wind blades, featuring reduced operating cost, CO2 emissions.
Read MoreComposite bipolar plates provide 81% improvement to hydrogen fuel cell power density
Ultra-thin CFRTP plates developed by Hycco achieve a 7.5 kilowatt/kilogram power density, high durability for fuel cells in long-flight drone and heavy-mobility applications.
Read MoreRead Next
VIDEO: High-volume processing for fiberglass components
Cannon Ergos, a company specializing in high-ton presses and equipment for composites fabrication and plastics processing, displayed automotive and industrial components at CAMX 2024.
Read MorePlant tour: Daher Shap’in TechCenter and composites production plant, Saint-Aignan-de-Grandlieu, France
Co-located R&D and production advance OOA thermosets, thermoplastics, welding, recycling and digital technologies for faster processing and certification of lighter, more sustainable composites.
Read MoreAssembling the Multifunctional Fuselage Demonstrator: The final welds
Building the all-thermoplastic composite fuselage demonstrator comes to an end with continuous ultrasonic welding of the RH longitudinal fuselage joint and resistance welding for coupling of the fuselage frames across the upper and lower halves.
Read More