Mito Material Solutions cuts ribbon on new facility in Indianapolis
The graphene additive developer, which serves sporting goods and other composites markets, grows its capabilities with a new facility that includes in-house R&D and testing space.
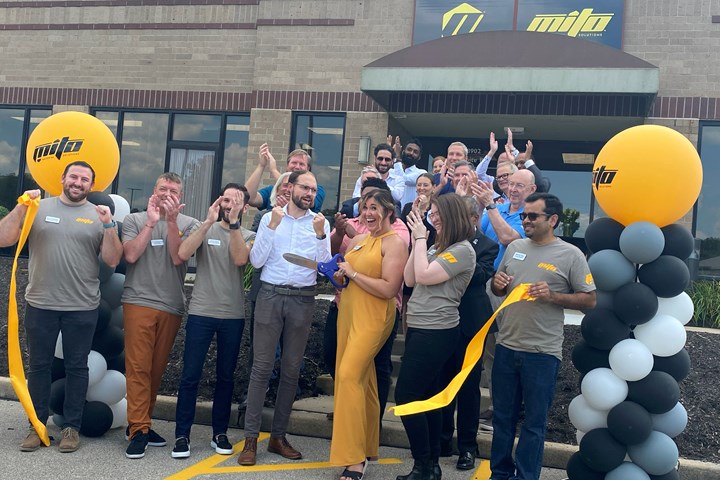
The Mito Materials Solutions team cut the ribbon on their new Indianapolis-based headquarters on Aug. 24, 2022. Photo Credit: CW
On Wednesday, Aug. 24, Mito Material Solutions (Indianapolis, Ind., U.S.) held a ribbon-cutting ceremony and open house to celebrate the recent opening of its new headquarters in Indianapolis.
The company, originally started in Oklahoma, develops additives to enhance performance of composites and plastics, including its flagship graphene oxide-based additive E-GO.
Within composites, Mito’s E-GO product is used to decrease weight and increase mechanical properties such as strength, electrical conductivity and thermal conductivity in composite sporting goods applications such as skis and fishing rods. E-GO and Mito’s other additives can be dispersed directly into a resin in amounts as small as 0.1% concentration for composites fabrication, or come in a spray format to be applied to a prepreg.
To answer your questions, the new building is 7,000 sq ft and we currently have a FT team of 7 and 4 PT remote team members bringing our total size to 11 with 6 open FT positions and internship opportunities available.

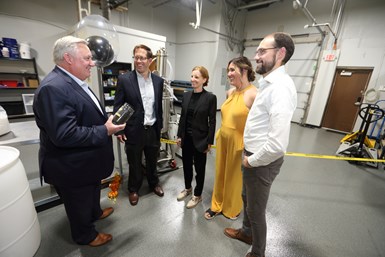
At the new, 7,000 square-foot facility, Mito houses its staff offices, commercial-scale graphene functionalization and dispersion equipment, an R&D laboratory with where the company can fabricate sample parts with its materials and an in-house analytical room for testing material properties. The R&D lab includes capabilities for hand layup, vacuum infusion and waterjet cutting with more equipment to come, and the testing room includes equipment to test a sample part’s flexure and tensile strength, interlaminar toughness, compression strength, as well as thermal, electrical and vibrational properties.
Mito’s team now includes 7 full-time and 4 part-time remote team members, with full-time and internship opportunities available.
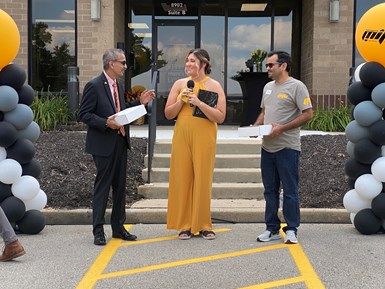
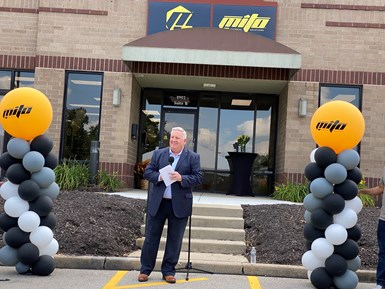
Speakers at the Aug. 24 ribbon-cutting event included Haley Keith, CEO of Mito Material Solutions, as well as partners Kip Frey, executive VP of new ventures at The Heritage Group (Indianapolis); Julie Heath, VP of entrepreneurial ecosystems at the Indiana Economic Development Corp. (Indianapolis); Dale Brosius, interim CEO of IACMI (Knoxville, Tenn., U.S.); and Keith Blakely, chairman and CEO of OnCore Golf Technology Inc. (Buffalo, N.Y., U.S.).
“We want to celebrate our journey so far and also what’s to come,” Keith said at the event. “Our products don’t just exist in the lab; we have the ability to solve a wide variety of problems and provide solutions that redefine what’s possible.”
Mito Materials, led by husband and wife team Haley Keith and CTO Kevin Keith, began as a startup in 2015 based on nano-additive technology developed by Oklahoma State University and research funded by the National Science Foundation (NSF). The company went through Heritage Group’s Accelerator program, and earlier this year raised $4.5 million in a funding round that closed in January 2022.
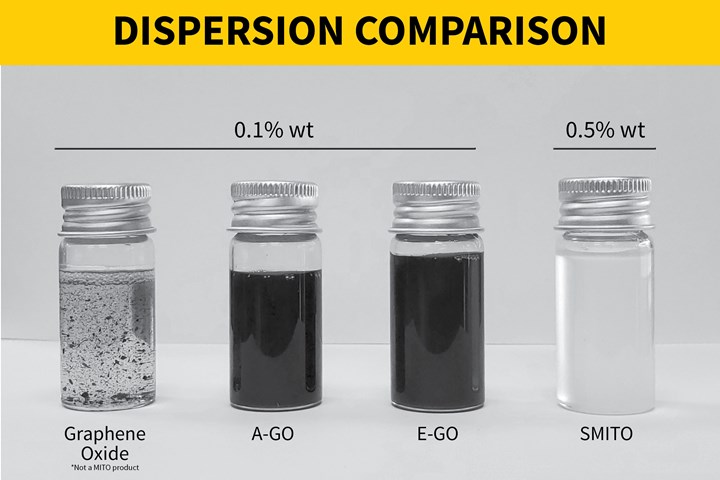
The move to Indiana brings the company closer to several of its partners and potential composites industry leaders. “In Indiana, there are a lot of opportunities to connect with composites companies and real opportunity to serve in new areas like EV battery boxes, hydrogen storage tanks especially cryogenic liquid hydrogen storage, wind turbines and more,” Brosius said at the event.
Looking to the future, the company plans to move into new composites markets and is currently aiming to grow its team, with six open positions.
Related Content
Canatu, Denso sign agreement to improve CNT performance
Denso, one of Canatu’s largest shareholders and an automotive supplier, will help height Canatu’s CNT performance, develop CNT reactors and advance its practical applications.
Read MoreAMD to open U.S. subsidiary for defense, aerospace nanotechnology
AMD Inc., based in Austin, Texas, has a broad license to all parent company IP and will continue to invest in R&D projects with the group’s existing university partners.
Read MoreFibreCoat develops radar-absorbing fiber-reinforced composite
Broadband, flexible material offers protection against radiation, heat and electromagnetic interference, and maintains performance across curved surfaces and slanted angles, outperforming existing materials by up to 100 times.
Read MoreHuntsman, AMD collaborate for functional composites development
Electrically enhanced, carbon nanotube-integrated composite materials will be supported by Advanced Material Development’s (AMD) nanomaterials expertise and Huntman’s chemical and material solutions.
Read MoreRead Next
VIDEO: High-volume processing for fiberglass components
Cannon Ergos, a company specializing in high-ton presses and equipment for composites fabrication and plastics processing, displayed automotive and industrial components at CAMX 2024.
Read MorePlant tour: Daher Shap’in TechCenter and composites production plant, Saint-Aignan-de-Grandlieu, France
Co-located R&D and production advance OOA thermosets, thermoplastics, welding, recycling and digital technologies for faster processing and certification of lighter, more sustainable composites.
Read MoreAssembling the Multifunctional Fuselage Demonstrator: The final welds
Building the all-thermoplastic composite fuselage demonstrator comes to an end with continuous ultrasonic welding of the RH longitudinal fuselage joint and resistance welding for coupling of the fuselage frames across the upper and lower halves.
Read More