Magnomatics designs air-cooled propulsion motor for UAM
Carbon ThreeSixty will be evaluating composite materials use to further reduce weight and increase torque for the 86-kilowatt magnetic gear motor.
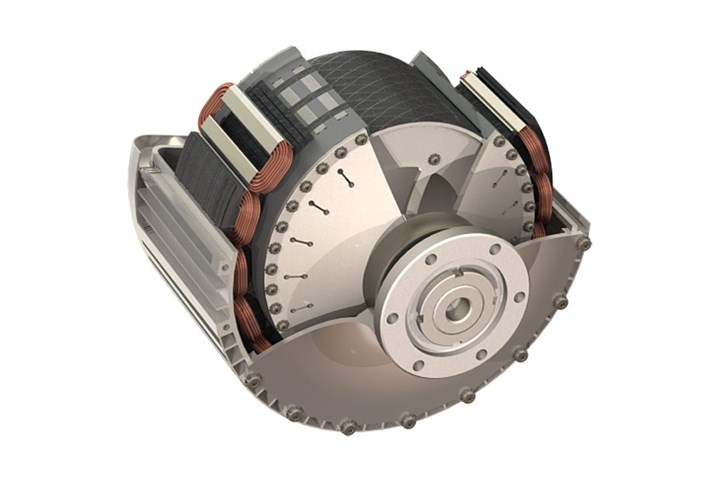
Magnomatics' lightweight, air-cooled propulsion motor. Photo Credit: Magnomatics
Magnetic gear technology company (Sheffield, U.K.) has designed a lightweight, air-cooled propulsion motor suitable for the rapidly growing urban air mobility (UAM) sector. The 86-kilowatt motor with a torque density of 30 newton-meters per kilogram (Nm/kg) will, it says, challenge other established motors in the market.
The company has recently started a NATEP (National Aerospace Technology Exploitation Programme) grant-funded project to investigate further light-weighting of this motor and is collaborating with (Chippenham, U.K.) to see how composite materials can be used to further reduce the mass and potentially enhance performance to provide an increase in torque density to greater than 30 Nm/kg. The motor will be manufactured and tested to meet DO-160G specifications.
NASA (Washington, D.C., U.S.) has identified magnetic gears as being a potential technology for electric aircraft. In 2018, it embarked on a two-and-half-year program described in the paper “.” NASA’s original focus was on pure magnetic gears but in the 2020 paper, “,” they concluded that the concentric combination of a magnetic gear and a permanent magnet motor would be ideal for an electric vertical takeoff and landing (eVTOL) UAM aircraft.
Magnomatics spun out of the University of Sheffield in 2006 to commercialize this technology based on magnetic gears. Among its patented products is the pseudo direct drive (PDD), which is an outer stator magnetically geared motor (OMSGM). The first commercial priorities for the PDD were for relatively large machines for applications such as wind power, marine propulsion and rail. In 2019, Magnomatics built and tested the largest PDD to date, with a 200,000 newton-meter rating. This was subsequently tested at the Offshore Renewable Energy Catapult at Blyth in the U.K.. Based on the results, a large global engineering company is now evaluating the PDD technology for a number of sectors.
The UAM motor designed is based upon PDD technology, identified by NASA as being “roughly two times greater than the specific torque expected of a direct drive electric motor for the same application.”
Magnomatics says that key features of the motor include: Highest continuous torque density; less than 60% size and mass of a PM machine; high efficiency; fault tolerance; built-in passive torque fuse (protecting drivetrain); low maintenance; and high reliability.
“We are delighted to receive support from NATEP for this project. The market for eVTOL motors for UAM is forecast to be substantial and we believe we can provide motors that will deliver a significant advantage,” David Latimer, CEO of Magnomatics, says. “Our long-term intention is to manufacture these motors here in Sheffield. A contribution not just to leveling up, but also to achieving net zero.”
Related Content
-
The potential for thermoplastic composite nacelles
Collins Aerospace draws on global team, decades of experience to demonstrate large, curved AFP and welded structures for the next generation of aircraft.
-
Plant tour: Airbus, Illescas, Spain
Airbus’ Illescas facility, featuring highly automated composites processes for the A350 lower wing cover and one-piece Section 19 fuselage barrels, works toward production ramp-ups and next-generation aircraft.
-
Industrializing additive manufacturing in the defense/aerospace sector
GA-ASI demonstrates a path forward for the use of additive technologies for composite tooling, flight-qualified parts.