Kisling epoxy adhesive improves carbon fiber bonding performance in automotive applications
The 2K-Epoxy ergo 7440 offers the removal of the bond-line read-through, attain high temperature resistance, avoids contact corrosion and enables quick turnaround during production.
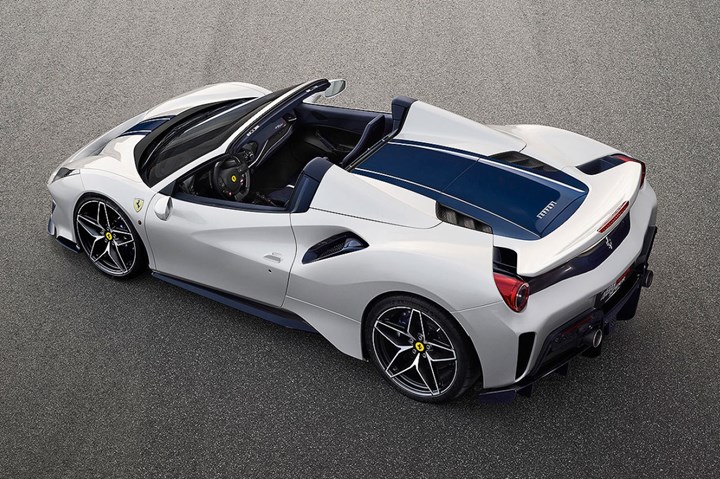
Kisling’s 2K-Epoxy adhesive ergo 7440 applied to the new Ferrari F488 Pista Spider. Photo Credit: Kisling
Swiss-based adhesives manufacturer, (Wetzikon), has reportedly added 2K-Epoxy ergo 7440 to its ergo product structural portfolio. The new structural adhesive product is said to improve the bonding performance of carbon fiber parts for a variety of applications in the automotive industry. Due to several of its advantageous features, Kisling says, it has aided the Italian sports car manufacturer Ferrari in solving a current adhesive issue for a new automobile development.
For example, Kisling contends that ergo 7440 provides almost invisible composite bonding by removing the bond-line read-through (BLRT) — a visible distortion of the substrate over a cured adhesive bond-line — due to low shrinkage capabilities. An almost-invisible glue line was additionally accomplished by the black coloring of the epoxy adhesive.
This product is also said to attain high temperature resistance of 180 °C. This performance criteria was proven by a 2,000-hour test. As can be seen from the graphic below, the Kisling ergo 7440 adhesive provides exceptionally high bonding strength after 2,000 hours of testing at 200 °C.

Photo Credit: Kisling
Further, a defined bonding gap is ensured via additives incorporated into the epoxy adhesive, avoiding contact corrosion in metal-carbon connections, and a 40-minute process time ensures that there is enough time for the bonding process, even with high ambient temperatures during the warmer months. Additionally, says Kisling, the ergo 7440 delivers a fast build-up of handling strength after 3.5 hours for quick turnaround during production.
Related Content
-
From the CW Archives: Airbus A400M cargo door
The inaugural CW From the Archives revisits Sara Black’s 2007 story on out-of-autoclave infusion used to fabricate the massive composite upper cargo door for the Airbus A400M military airlifter.
-
RWC delivers composite frac plugs for downhole environments
Filament-wound fiberglass/epoxy frac plug billets, developed as part of a contract with an oilfield service company, address the very demanding performance needs of oil and gas.
-
From the CW Archives: Fast-cure epoxies for automotive fabrication
Sara Black’s 2015 report on the development of snap-cure epoxies for automotive manufacturing still resonates today.