IntegriCo Composites expands existing composite rail tie production into high-growth markets
Company bolsters existing product line into pipeline skids and construction matting parts while maintaining a continued focus on recycled plastic sustainability solutions.
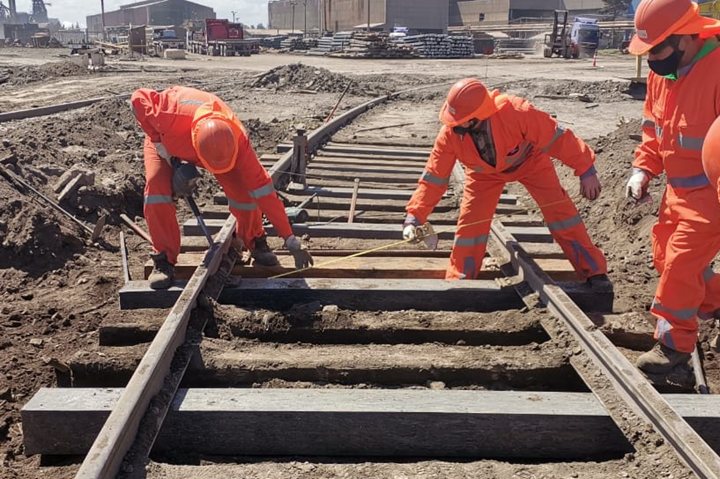
Photo Credit: IntegriCo Composites
(Sarepta, La., U.S.), a manufacturer of composite railway crossties and construction mats, announced on Feb. 11 a strategic expansion plan that includes entering two high-growth markets — pipeline skids, and construction matting parts — following a comprehensive review of key markets.
The expansion into new markets with strong growth potential reportedly builds on IntegriCo’s track record for manufacturing high-performance rail industry products that have a positive environmental impact. These new products will add to IntegriCo’s existing rail tie production, which mixes recycled landfill-bound plastic to create composite railroad ties. IntegriCo will continue to focus on driving sustainability solutions which includes over a decade of diverting and reusing approximately 80 million pounds of landfill bound plastics, to replace products that are traditionally made from wood with recycled plastics.
In tandem with the repositioning, Nicholas Singer has been named executive chairman and is responsible for day-to-day management of the company, with support from Daniel Lyons, who was appointed vice president of Corporate Development; Scott Stewart, who was appointed vice president of Operations; and Bryan Kelley, who serves as plant manager.
“We’re excited about our leading position in new markets with substantial future growth opportunities,” says Singer. “We have established trust with our vendors and customers, and positioned the business on strong financial footing that will serve as a springboard for continued growth while continuing to benefit the environment.”
According to the company, composite materials are rapidly gaining importance in the energy industry for their durability and benefit to the environment. Through IntegriCo’s specialized process and technology, the company’s pipeline skids and construction matting parts are highly resistant to rot, insect and chemical damage. Additionally, IntegriCo’s composite matting parts do not absorb construction site and drill site liquid contaminants, proving them easy to dispose of at end of life. IntegriCo’s products are made of 100% recycled plastic and are said to be easier to clean than wood products, which enables them to be transported across state lines without environmental concerns.
The strategic repositioning follows a recapitalization led by affiliates of Purchase Capital LLC, Singer’s family office, with participation from Acadia Woods Partners LLC.
Related Content
-
Bladder-assisted compression molding derivative produces complex, autoclave-quality automotive parts
HP Composites’ AirPower technology enables high-rate CFRP roof production with 50% energy savings for the Maserati MC20.
-
Hybrid process marries continuous, discontinuous composites design
9T Labs and Purdue applied Additive Fusion Technology to engineer a performance- and cost-competitive aircraft bin pin bracket made from compression-molded continuous and discontinuous CFRTP.
-
Plant tour: Collins Aerospace, Riverside, Calif., U.S. and Almere, Netherlands
Composite Tier 1’s long history, acquisition of stamped parts pioneer Dutch Thermoplastic Components, advances roadmap for growth in thermoplastic composite parts.