Impossible Objects, Ricoh 3D partner to produce high-strength 3D-printed composite parts
New material options for industrial customers across Europe to remove barriers to printing parts for drones, aircraft, automobiles, athletic gear and more.
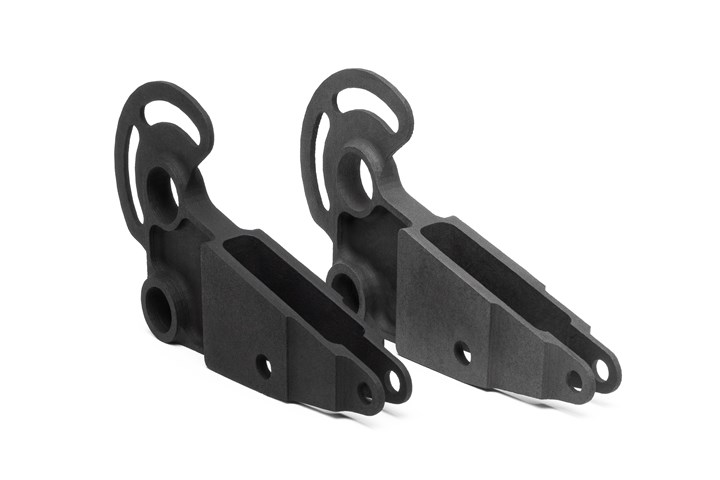
A bell crank created with Impossible Objects’ CBAM process. Photo Credit: Impossible Objects
A new partnership between 3D printer and materials company (Northbrook, Ill., U.S.) and 3D printing specialist Ricoh 3D (Shropshire, U.K.) will reportedly make strong and lightweight printed composite parts available to Ricoh 3D’s customers in Europe for the first time.
According to Impossible Objects, its composite-based additive manufacturing (CBAM) process enables the production of stronger parts at costs lower than alternative 3D printing processes. Composites boast key advantages for 3D-printed parts, the company says, including superior strength-to-weight ratios, fewer geometric restrictions, superior high-temperature performance and greater chemical resistance.
“Composites are set to be an area of huge growth in additive manufacturing [AM] in the coming years. These new materials will change the game across a number of industries,” says Mark Dickin, Additive Manufacturing and Molding engineering manager at Ricoh 3D. “Impossible Objects’ CBAM process is nothing short of a revolution in the way composites are manufactured, so we are proud to be working with the company to be at the forefront of the European movement.”
Composites including carbon fiber polyetheretherketone (PEEK) and carbon fiber PA12 are available through Ricoh 3D’s AM service bureau immediately.
“Our CBAM process represents a significant leap forward in 3D printing, with faster speeds, better material properties and wider material selection,” says Robert Swartz, chairman and founder of Impossible Objects. “Fortune 100 companies, government agencies and more have already put it to work to create everything from car and aircraft parts to athletic gear. By collaborating with the team at Ricoh 3D who recognizes the transformative potential of AM, together we will bring these competitive advantages to more organizations across Europe.”
Impossible Objects’ proprietary CBAM technology can produce parts up to ten times faster than conventional fused deposition modeling (FDM) 3D printing. By combining high-performance polymers like Nylon and PEEK with carbon fiber and fiberglass sheets, parts printed with Impossible Objects machines are said to be stronger, lighter have better dimensional accuracy, and maintain better temperature performance than what’s possible with conventional 3D printing methods. The CBAM process can create strong and resilient fine or flat parts, which is important for applications like drones; these have been impossible with FDM and FFF technologies due to the short, chopped fiber formation and lamination between layers, which cause parts to fall apart under force.
Ricoh 3D is the latest industry partner to join forces with Impossible Objects to drive additive manufacturing forward. Other collaborators include chemical giant (Ludwigshafen, Germany) and (Wels, Austria).
Related Content
-
In oil and gas, an additive manufacturing standard (API 20T) will aid adoption of composites
Polymer AM equipment maker Roboze sees how the oil and gas industry’s way forward with additive is like that of another high-stakes industry, aerospace, and also different in important aspects.
-
Hitachi Rail chooses Roboze printers, materials including carbon fiber/PEEK for railway spare parts
The Roboze ARGO 500 will be used at Hitachi Rail factories in Naples, Italy and Maryland, U.S. to reduce cost and delivery times for prototypes and spare parts.
-
Formula 1 team adopts Roboze 3D printed composites
The Visa Cash App RB Formula 1 team is collaborating with Roboze to reduce weight and create parts with complex geometries via carbon fiber/PEEK.