GMI Aero enhances digital/physical twin network application for Anita hot bonder
EVOLVED-5G project seeks to test, validate and certify, in a vendor-agnostic experimentation 5G platform, Industry 4.0 network applications.
Photo Credit, all images: GMI Aero
, a provider of composite repair solutions, is joining 20 other European entities in , a Horizon2020 R&D project that seeks to test, validate and certify, in a vendor-agnostic experimentation 5G platform, Industry 4.0 Network Applications (NetApps). This is expected to shape a new and dynamic ecosystem in mobile networks from technology and marketing perspectives.
As a participant, GMI Aero has taken on an “Innovator SME,” role, supporting the development of case-tailored NetApps in order to compose a digitalized, secure and automated generation of industrial operations for process and machine control (i.e., Industry 4.0).
GMI Aero is specifically focused on further enhancing the digital/physical twin NetApp through the company’s Anita 4.0 hot bonder used to digitize composites repair. The remote (original) Anita 4.0 is locally connected via 5G to transmit real-time curing data to engineering centers and certification authorities. A second (replica) Anita 4.0 is then connected, following the actual curing cycle (i.e. “slaved” to the lowest thermocouple, or T/C) in order to produce a physical twin — eventually used for nondestructive testing, differential scanning calorimetry, mechanical testing, etc. — or a digital twin through channeling repair data to a computer running resin curing equations, and calculating the glass transition and degree of curing.
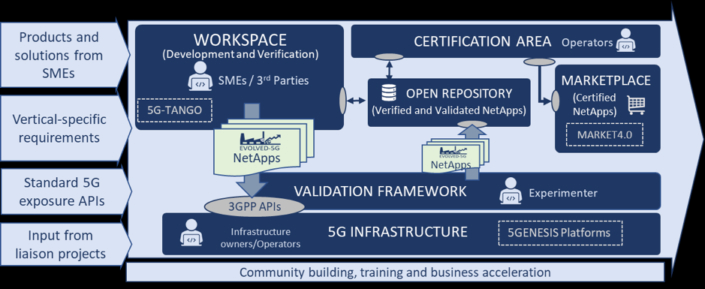
EVOLVED-5G objectives.
GMI Aero and EVOLVED-5G partners have developed NetApps taking advantage of the novel 5G network “services,” as follows:
- Quality of service: Providing 5G connection quality status. In case of degraded quality, only basic data is transmitted from the original to the replica Anita 4.0, while remaining information will be retransmitted automatically, as soon as the network recovers (buffering).
- Geo-localization: Calculates and indicates on the equipment screen the coordinates (longitude and latitude) of the exact position of the original Anita 4.0 hot bonder, thus permitting its continuous traceability by the engineering team and certification authority.
To learn more about this project, read the consortia’s recently published white paper, “,” and watch these on Anita 4.0 and EVOLVED-5G developments.
Related Content
-
How AI is improving composites operations and factory sustainability
Workforce pain points and various logistical challenges are putting operations resilience and flexibility to the test, but Industry 4.0 advancements could be the key to composites manufacturers’ transformation.
-
Siemens software chosen for JetZero BWB aircraft concept, launches Xcelerator updates
Aviation startup will use the Xcelerator platform to achieve its aircraft vision. Other Siemens collaborations deliver software additions to deliver, democratize industrial AI for small companies, startups.
-
SAM XL demonstrates closed-loop digital methodologies via full-size aerocomposite parts development
PeneloPe Project’s modular, zero-defect manufacturing deliverables are being highlighted in an upcoming video that demonstrates the resulting aerospace pilot line’s feasibility.