GE Aerospace awarded demonstration contract for NASA HyTEC project
Turbofan engine small core technology development with CMC-coated components targets enhanced fuel efficiency in single-aisle aircraft by mid-2030s.
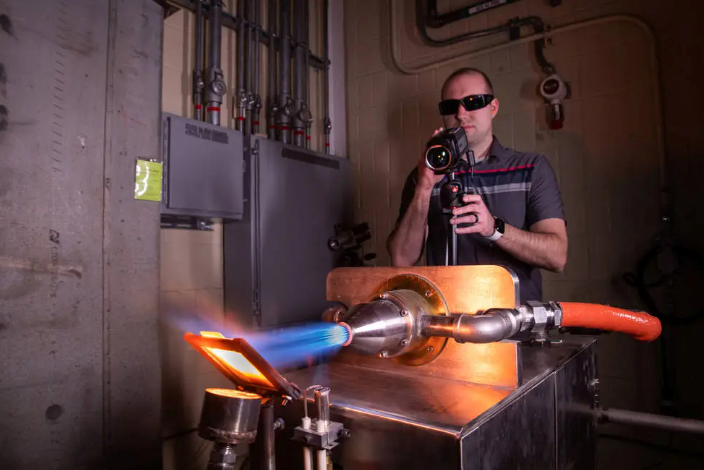
Michael Presby, a research materials engineer at NASA’s Glenn Research Center in Cleveland, adjusts an infrared thermal imaging camera used to monitor the temperature profile of a NASA-developed, high-temperature environmental barrier coating deposited on a CMC in support of the agency’s HyTEC project. The composite’s environmental barrier coating surface temperature is 3,000ºF. Photo Credit:
(Washington, D.C., U.S.) has selected (Cincinnati, Ohio, U.S.) to work with the agency’s Hybrid Thermally Efficient Core () project, which is aiming to develop more fuel-efficient engines for single-aisle aircraft. As part of the project, HyTEC will be implementing ceramic matrix composite (CMC) materials in some engine components with environmental barrier coatings.
The HyTEC’s Phase 2 Integrated Core Technology Demonstration is a cost-sharing contract with a maximum value of approximately $68.1 million and a 5-year performance period that begins Feb. 15, 2024. The contract is awarded with a 50% minimum GE Aerospace cost share during the contract period.
Part of NASA’s Advanced Air Vehicles program, HyTEC was established in June 2021 to accelerate the development of turbofan engine small core technologies. The project also includes work on hybridization — developing methods to pull more electrical power from this engine to power other systems aboard the aircraft, which could increase fuel efficiency in much the same way a hybrid car does. In a on the subject, Anthony Nerone, who leads the HyTEC project from NASA’s Glenn Research Center in Cleveland, said that “with the small-core engine in specific, we are targeting a 5-10% fuel burn reduction,” though he notes that, combined with other initiatives, this estimation could increase.

This cross-section of a turbofan jet engine shows the components of the HyTEC project’s smaller engine core, with the compressor, combustor, and turbine noted. By shrinking the engine core, better fuel efficiency can be achieved. Photo Credit: NASA
The first phase of the project focused on developing several key engine core technologies, including high-pressure compressors, high-pressure turbines, advanced materials, electric hybridization and compact combustors, through subsystem or component tests. To meet the goal of HyTEC Phase 2, GE Aerospace will integrate these technologies into an engine core to perform a compact, high-power density core ground demonstration by the end of September 2028. This next step is in line with NASA’s plan to “collaborate with engine companies to make small-core technologies available much sooner than planned … for use in aviation fleets around the mid-2030s.”
Related Content
Automated robotic NDT enhances capabilities for composites
Kineco Kaman Composites India uses a bespoke Fill Accubot ultrasonic testing system to boost inspection efficiency and productivity.
Read MorePlant tour: Airbus, Illescas, Spain
Airbus’ Illescas facility, featuring highly automated composites processes for the A350 lower wing cover and one-piece Section 19 fuselage barrels, works toward production ramp-ups and next-generation aircraft.
Read MoreFirst Airbus A350 crash confirmed in Haneda
Shortly after touch-down, a JAL A350-900 aircraft recently collided with a De Havilland Canada Dash 8. Exact circumstances are still unknown.
Read MoreCombining multifunctional thermoplastic composites, additive manufacturing for next-gen airframe structures
The DOMMINIO project combines AFP with 3D printed gyroid cores, embedded SHM sensors and smart materials for induction-driven disassembly of parts at end of life.
Read MoreRead Next
Airbus, CFM International collaborate on hydrogen combustion technology
A380 flying testbed will be equipped with liquid hydrogen (LH2) tanks and modified turbofan engine to take flight around the middle of this decade.
Read MoreGKN enhances aeroengine agreement with GE Aerospace
Extended deal sees new tech development and implementation for the GEnx, increased engine fan case supply and GKN’s addition to the repair network.
Read MoreNASA moves into next phase of high-speed supersonic travel project
Under the Advanced Air Vehicle’s Program, Boeing- and Northrop Grumman-led teams are charged with developing technology roadmaps with vehicle concepts that can operate at Mach 2+ speeds.
Read More