Epic Aircraft receives FAA type certification for E1000 GX aircraft
The new E1000 GX is equipped with the Hartzell five-blade composite propeller, offering improved performance, safety, comfort and versatility.
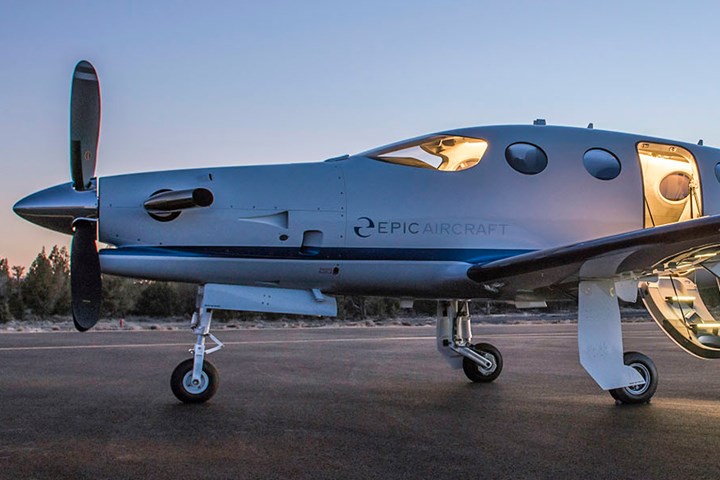
Private aviation company (Bend, Ore., U.S.) announced it has received FAA type certification(TC) for its E1000 GX model. The new E1000 GX is equipped with the Garmin GFCTM 700 automated flight control system and a (Piqua, Ohio, U.S.) five-blade composite propeller, offering improved performance, safety, comfort and versatility.
“We are seeing benefits from the Hartzell five-blade, including improved speed, climb, range, payload and take-off performance. Plus, we are experiencing quieter operations inside and outside the cabin,” comments Epic CEO, Doug King. Hartzell’s composite propeller is said to provide stronger, composite resin-injected blades that allow for a thinner, wider airfoil, reportedly optimizing flight performance and offering faster take-off acceleration.
Epic Aircraft received FAA TC for its original E1000 model in November 2019. Powered by the Pratt & Whitney (East Hartford, Conn., U.S.) 1,200-horsepower PT6A-67A engine, the all-carbon fiber single-engine turboprop delivers cruise speeds over 333 knots, climbs at 4,000 feet per minute and operates up to 34,000 feet, with a maximum payload that is more than 2,200 pounds and a full fuel payload of 1,100 pounds.
The Epic E1000 reportedly received Flying Magazine’s 2020 Flying Innovation Award, which recognizes the most innovative product to have reached the general aviation market in the previous year. The E1000 was also selected by Plane & Pilot Magazine as its 2020 Plane of the Year.
The E1000 GX, which replaces the original E1000 model, is priced at $3.85 million. Customer deliveries will begin this month.
Related Content
-
Carbon fiber composite pallet revolutionizes freight industry
LOG Point Pallet fuses advanced materials with innovative design and manufacturing to improve supply chains worldwide.
-
Bladder-assisted compression molding derivative produces complex, autoclave-quality automotive parts
HP Composites’ AirPower technology enables high-rate CFRP roof production with 50% energy savings for the Maserati MC20.
-
Sulapac introduces Sulapac Flow 1.7 to replace PLA, ABS and PP in FDM, FGF
Available as filament and granules for extrusion, new wood composite matches properties yet is compostable, eliminates microplastics and reduces carbon footprint.