ELIOT Project finds solvolysis best method for aerospace biocomposites recycling
Aimplas and TNO study analyzed 12 methods for six different biocomposites. Solvolysis and pyrolysis proved the two most promising alternatives tested in large-scale production at a pilot plant.
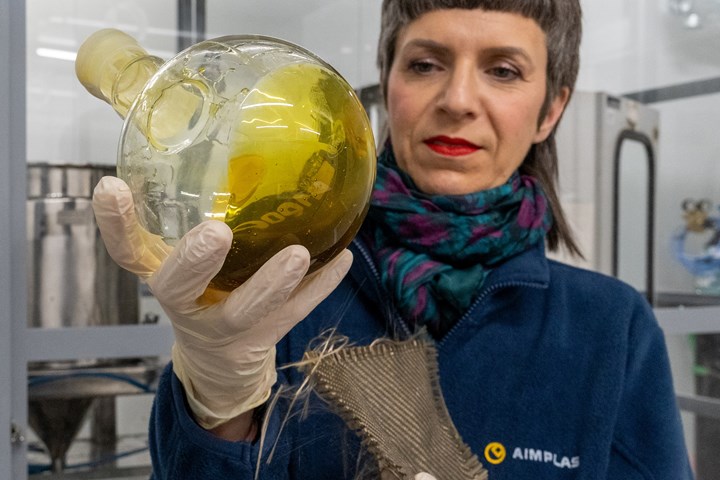
Photo Credit: Aimplas
Biocomposite materials are seeing increased use in the fabrication of aviation components in order to address environmental concerns. The materials use natural fibers for reinforcement and resins from renewable sources. However, the novelty and heterogeneous nature of biocomposite thermoset materials and the fact that they lack carbon fibers — which have a high market value — make it difficult to find an efficient management solution when these materials become waste at the end of their useful life.
Aimplas, the Plastics Technology Centre (Valencia, Spain), and the Dutch research centre TNO (Hague, Netherlands) have completed the , a study that involved an in-depth review of current recycling technologies for the composites and biocomposites used in the aeronautics sector and an analysis of the best alternatives on a pilot plant scale that are also technically and financially feasible. As a result of the study, solvolysis was found to be the best method of the 12 technologies analyzed for recycling six different biocomposite materials.
The study is targeted at searching for cost-effective recycling technologies that enable the aeronautics industry to guarantee the sustainability of its components in the search for new solutions aligned with the circular economy. The results show that pyrolysis emits 17% more carbon dioxide and consumes twice as much heat as solvolysis, which entails additional associated costs. Solvolysis uses solvents as a substitute for heat, but these solvents are recovered with great efficiency and reused in the process. The ELIOT project has also shown that solvolysis works even better on large biocomposites.
For both pyrolysis and solvolysis, additional purification steps are required to be able to use the pyrolysis liquid and the distilled product, respectively. These estimates were made based on a processing plant with a capacity of 10 kilotonnes of biocomposites per year.
Other technologies analyzed in the study included mechanical recycling, dissolution, enzymatic degradation, gasification and composting.
The ELIOT Project received funding from the European Union’s Horizon 2020 research and innovation program within the framework of the Clean Sky Joint Technology Initiative under grant agreement number 886416.
Related Content
-
Hybrid process marries continuous, discontinuous composites design
9T Labs and Purdue applied Additive Fusion Technology to engineer a performance- and cost-competitive aircraft bin pin bracket made from compression-molded continuous and discontinuous CFRTP.
-
Infinite Composites: Type V tanks for space, hydrogen, automotive and more
After a decade of proving its linerless, weight-saving composite tanks with NASA and more than 30 aerospace companies, this CryoSphere pioneer is scaling for growth in commercial space and sustainable transportation on Earth.
-
Welding is not bonding
Discussion of the issues in our understanding of thermoplastic composite welded structures and certification of the latest materials and welding technologies for future airframes.