Clemson Composites Center leads research in low-cost composite tooling
Innovative technology approach to use additive manufacturing and artificial intelligence to produce tools faster, at a lower cost and with less environmental impact.
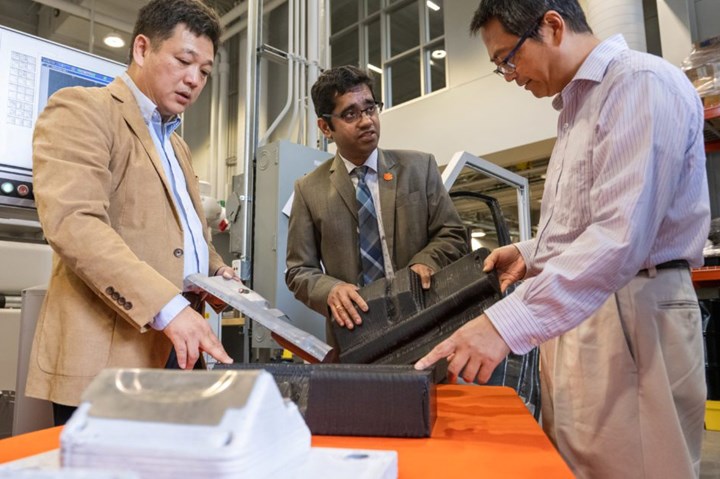
Srikanth Pilla (center) talks about manufacturing tools with Gang Li (left) and Feng Luo (right). Photo Credit: Clemson Composites Center
Clemson University’s (CCC, Greenville, S.C., U.S.) team is leading a new study — the development of new ways to 3D print low-cost manufacturing tools — that could help manufacturers save time and money while reducing their environmental impact.
The research, to be based at the CCC’s Greenville, S.C., facility, is funded with $5.16 million from the U.S. Department of Energy’s (DOE) Advanced Manufacturing Office and industry partners. Collaborators on the project include Ohio-based Honda Development & Manufacturing of America, Ohio State University (Athens) and Additive Engineering Solutions LLC (Akron).
Since its founding in 2017, the CCC has built its reputation for developing new ways of making ultralight and recyclable automotive components out of composite materials. The project will add to the center’s fast-growing portfolio of industry-guided automotive and advanced manufacturing research.
With the new funding, the center’s researchers are said to be using some of the same techniques to create not the components themselves but the tools that would be used to stamp sheets of metal or composites into components, says Srikanth Pilla, the project’s principal investigator, founding director of the CCC and the Jenkins Endowed Professor of Automotive Engineering. According to Pilla, the research could help lower the cost of tools, which are often expensive to develop and produce.
“The composite tool is a low-cost technology,” Pilla says. “At the same time, you can recycle the tools we will be creating. That’s why we decided to repurpose innovations that happened in the Clemson Composite Center for these kinds of applications.”
Researchers expect that at the end of the project they will have technology that OEMs could rapidly commercialize and put into use in a real-world factory.
A big part of what makes the research unique is that the team will be using innovative techniques, including artificial intelligence (AI), applied by Feng Luo, the Marvin J. Pinson, Jr. ’46 Distinguished Professor in Clemson’s School of Computing and founding director of the Clemson Artificial Intelligence Research Institute for Science and Engineering (AIRISE). Researchers will start with the desired performance of the tool they want to create, and AI will help determine the ideal composite material architecture and optimal manufacturing process, an approach called inverse design.
Gang Li, a Clemson mechanical engineering professor and CCC associate director, will use computational modeling and analysis simulation to help answer important questions, such as whether the tools researchers are trying to develop meet design requirements. The approach is said to enable researchers to test their ideas even before building a prototype, helping save time and money.
For Li, the project is an extension of his previous work with the CCC. He has also worked to help develop an ultra-lightweight vehicle door, advance 3D printing, modernize manufacturing machinery and reduce the weight of an SUV part that is interchangeably called the body-in-white or glider. “Our research is looking at the entire development and design of the vehicle, and that excites me a lot,” he says. “We’re not just looking at one small part, we’re looking at everything we can.”
The project is the CCC’s latest collaboration with Honda Development & Manufacturing of America. Both partners previously worked together on other projects, including the glider and the ultralight door, which recently was .
Ryan Hahnlen, a principal engineer at Honda Development & Manufacturing of America, says he looks forward to collaborating with the Clemson team again.
“This project brings new opportunities to develop new products for our customers more quickly and efficiently, while saving costs up and down the supply chain,” Hahnlen notes. “With this new research we will be better positioned to reduce carbon emissions and be more flexible to changing market conditions.”
The research is also the CCC’s latest collaboration with Ohio State University, led by Farhang Pourboghrat, professor and chair of the Integrated Systems Engineering Department. Andrew Bader, vice president and co-founder of Additive Engineering Solutions, expects to meet the project’s needs with the company’s experience in large-format additive manufacturing services for tooling, end-use parts and large-scale prototyping.
Related Content
Norco GFRP molds meet high-quality cast concrete beam production needs
A project with P&M successfully achieved manufacture of six 20-meter-long architectural beams for an R&D facility with near-seamless surfaces and on a tight production schedule.
Read MoreLaser cleaning in composites manufacturing
Laser cleaning technologies for cleaning production molds for composites offer alternatives to harsher, less-friendly methods with features like automation and higher power cleaning.
Read MoreJamco America partners with Airtech for 3DP tool recycling
Aerospace manufacturer joins forces with composite materials company to achieve sustainable manufacturing practices that overcome traditional composite layup tooling.
Read MoreBase Materials introduces BE890 epoxy tooling board
Base Materials introduces a high-performance, toughened epoxy tooling board designed for thermoforming and vacuum forming processes, direct-to-part applications and more.
Read MoreRead Next
Digitizing tools for composites production
Alpex Technologies focuses on industrialization, process and part intelligence and biocomposites in its next generation of tooling systems.
Read MoreVestas implements composites 3D printing to increase efficiency for blade alignment tools
A Markforged digital repository and multi-material 3D printers enable faster, more accurate and less costly manufacture of a variety of tools and blade components across Vestas sites.
Read MoreComposites end markets: New space (2025)
Composite materials — with their unmatched strength-to-weight ratio, durability in extreme environments and design versatility — are at the heart of innovations in satellites, propulsion systems and lunar exploration vehicles, propelling the space economy toward a $1.8 trillion future.
Read More