CEAD qualifies Airtech Dalhtram resins for use on all AM Flexbot platforms
Combination of the robot-based system with Airtech’s extensive resin line will enhance composites AM production and performance flexibility across multiple industries.
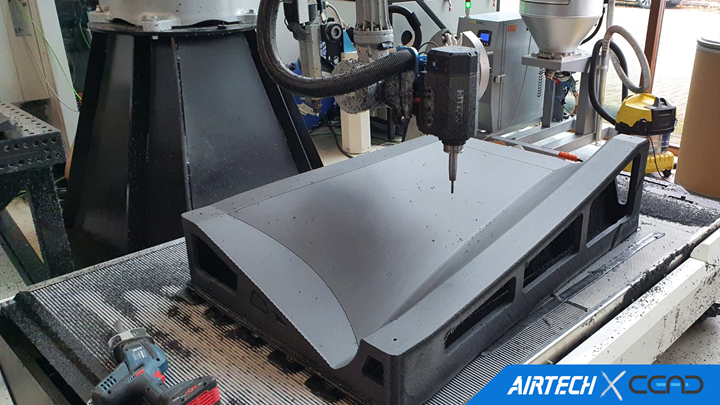
Photo Credit: Airtech, CEAD
In addition to expanded its offering of resins for use in additive manufacturing (AM) Airtech Advanced Materials Group’s (Huntington Beach, Calif., U.S.) Dalhtram resins have been qualified for use on all CEAD (Delft, Netherlands) robot-based AM Flexbot platforms. With exceptional process knowledge, application requirements and production performance, Airtech contends that this development offers breakthrough performance and unparalleled flexibility across industries.
The , one of CEAD’s solutions for large-scale composite AM, uses Comau (Turin, Italy) robots directly controlled by Siemens’ (Waltham, Mass., U.S.) Sinumerik operating system. It offers the option to combine 3D printing and milling into one automated process and provides multiple options which can be integrated to configure the system to specific needs. This versatility makes it ideal for moldmaking and tooling applications, for example, when needing to achieve a required surface finish.
Airtech Dahltram resins are suitable for multiple print platforms, offering production flexibility with end-use material validation. Airtech reports that it has continued to demonstrate efficacy in composites fabrication with extensive autoclave cycle testing across various platforms with all materials offered. Providing extensive mechanical characterization data, Dahltram resins are well suited for composites fabrication, as well as metal fabrication and direct-to-part applications.
This partnership is the latest gain in Airtech’s continued effort to drive innovation, development and testing in the AM market.
Related Content
-
Broetje-Automation demonstrates rCF placement via AFP
Through the ScrapSeRO project, the system integrator and machine builder successfully processed recycled composites, in addition to more traditional materials, via its highly flexible Staxx One system.
-
McClarin Composites partners with ExxonMobil to accelerate high-speed RTM
Multimillion-dollar investment to drive next-gen automated RTM technology will open new applications and markets for composites OEMs.
-
Mold 3D printing helps automate composite bathtub, shower production
As part of its efforts to automate as much of its production process as it can, Lyons Industries acquired a Massivit 10000 additive manufacturing system to quickly produce high-performance molds and support fixtures.