C12 Technology, Carbon Conversions launch products made with rCF
C12 Technology will offer rotomolded thermoplastic products reinforced with Carbon Conversions’ recycled carbon fiber (rCF) products.
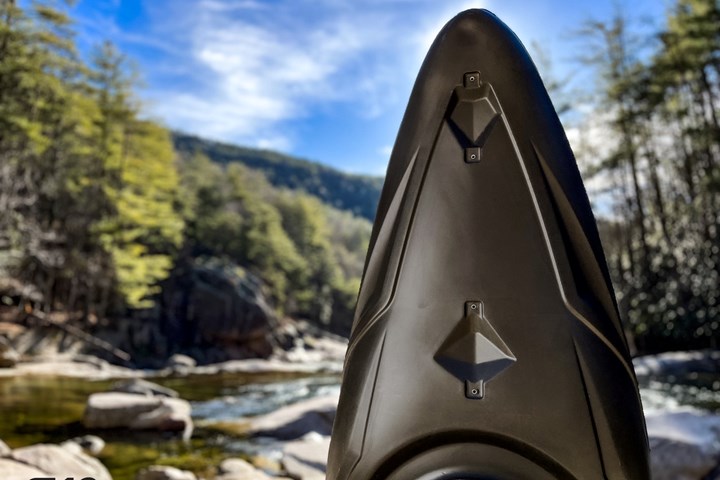
C12 Technologies kayak make with recycled carbon fiber from Carbon Conversions.
Photo Credit: Carbon Conversions
(Anderson, S.C., U.S.) and Carbon Conversions Inc. (CCI, Lake City, S.C., U.S.) reported on March 20 a partnership to innovate a novel technology and material to create what the companies say are the world’s first eco-friendly rotational-molded carbon fiber products. The companies completed a multi-year joint development agreement to produce a reinforced thermoplastic material that has the capability to be rotationally molded.
Combining C12’s rotomolding technology and CCI’s expertise in recycled carbon fiber, this new development enables production of large composite structures using low-cost tooling that produces parts with high mechanical properties in both stiffness and compressive strength. CCI’s recycled carbon fiber molding material, re-Evo RRC, is available now to support C12 customer-specific projects.
C12 offers rapid prototype development capabilities on a micro- and macroscale to trial new projects prior to production. Future applications could include, but are not limited to, ultra-lightweight recreational sporting goods including kayaks, industrial storage containers and pressure vessel liners.
Keith Graham, vice president of Carbon Conversions, says, “The utilization of our RRC product in Roto12’s technology is truly innovative. It is a strong statement which says they are committed to sustainable materials and continued environmental stewardship.”
According to C12 Technology CEO Oliver Wainwright, “Recycled rotomolded carbon products will not only bring the industry closer to the “closed-loop” green goal, but could truly change industry standards and allow companies the opportunities to grow into the future.”
Related Content
-
Otto Aviation launches Phantom 3500 business jet with all-composite airframe from Leonardo
Promising 60% less fuel burn and 90% less emissions using SAF, the super-laminar flow design with windowless fuselage will be built using RTM in Florida facility with certification slated for 2030.
-
Bladder-assisted compression molding derivative produces complex, autoclave-quality automotive parts
HP Composites’ AirPower technology enables high-rate CFRP roof production with 50% energy savings for the Maserati MC20.
-
Sulapac introduces Sulapac Flow 1.7 to replace PLA, ABS and PP in FDM, FGF
Available as filament and granules for extrusion, new wood composite matches properties yet is compostable, eliminates microplastics and reduces carbon footprint.