Blue Wind manufactures 1,000 nacelles in 28 months with one mold
Manufacturer combined speed and quality for composite wind turbine nacelles during the pandemic, producing 10 nacelles per week.
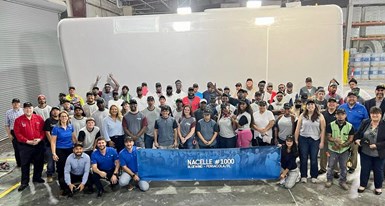
Blue Wind employees on the day the thousandth nacelle was manufactured. Photo Credit, all images: Blue Wind Technology
Specializing in the manufacture of composite parts, (Pensacola, Fla., U.S.) recently registered a significant milestone. With just one mold, the company says it was able to manufacture 1,000 nacelles in a period of 28 months. In other words, the number of nacelles that left its factory in less than three years would take twice as long to be produced in the normal market average (see its past milestones, “Brazilian-founded Blue Wind supplies more than 900 composite nacelles to U.S. wind energy market”).
The 1,000 nacelles manufactured via infusion by Blue Wind were part of a contract signed in late 2019 with (Paris, France). “In 90 days, we set up the factory from scratch to serve GE,” Jean Zolet, executive director of Blue Wind, recalls. With 9.1 meters in length, 2.9 meters in width and 3.6 meters in height, the nacelles are part of the 2X wind turbine.
In addition to the pandemic that had just erupted when it began its activities, Blue Wind’s biggest challenge in its first months of life was to hire enough manpower and train it. The company initially hired 120 employees.
Nacelle infusion process.
Even operating with only one set of molds, Blue Wind says it managed to reach the rhythm of 10 nacelles produced per week in four months. “Our production system combines speed and quality. In any case, keeping that pace with one mold means that everything must always work perfectly,” Zolet stresses.
From the quality point of view, the executive director of Blue Wind points out that the company holds, in addition to the ISO 9001:2015 certification, the APQP4Wind seal, a quality reference in the wind power generation industry. “We also had the plant and product certified by GE itself, which conducts a very strict program with its suppliers,” Zolet says.
In addition to expanding the supply of components to GE and starting partnerships with other wind turbine manufacturers, Blue Wind intends to expand its scope of action to different markets this year. The move will be supported not only by infusion, but also by other composite molding technologies.
Related Content
-
Engine vane demonstrates potential for gapped, unidirectional dry fiber for infusion
GKN Aerospace and its partners developed an aircraft demonstrator component made with TeXtreme’s latest Gapped UD material, proving out a dry, infusible tape meant to compare in performance to UD prepreg.
-
Sunreef Yachts completes 43-meter single-shot hull infusion project
Sunreef 43M Eco electric catamaran, with a composite surface of 1,700 square meters, is considered to have the world’s largest infused hull.
-
Infused sandwich window frame components help double-decker buses meet weight targets
Prototype GFRP parts were evaluated by Spanish bus manufacturer Carrocerías Ayats as an initial move toward lighter, more efficient, more automated parts and processes.