Bieglo Group thermoplastic polymer supports project to 3D print structures on the moon
High-performance Aurum resin, combined with regolith material, will be used to create a printing material mixture that holds up under the harsh lunar environment.
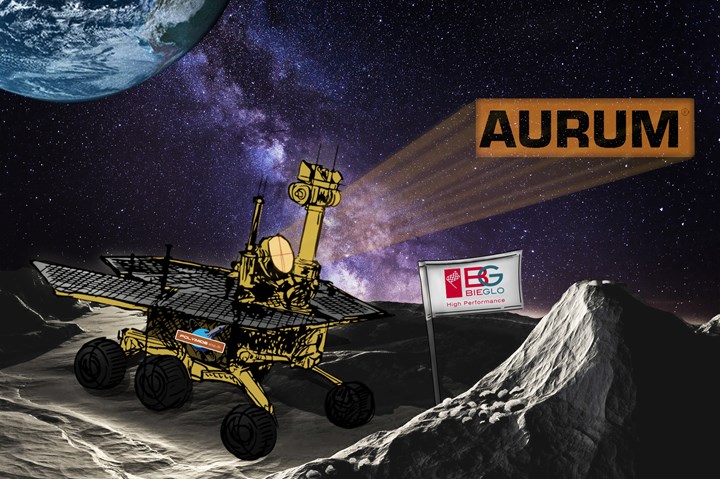
Photo Credit: Bieglo Group.
(Hamburg, Germany), with its U.S. subsidiary (Katy, Texas), is supporting a project by Engineering Polytechnique Montréal and HEC Montréal students to design and demonstrate the use of a 3D printer mounted on a lunar rover. Carried out in collaboration with the Canadian Space Agency and the Research Center for High Performance Polymer and Composite Systems (CREPEC), the 3D printer will be printing structures mainly using in-situ resources such as regolith, a layer of unconsolidated rocky material covering bedrock, as well as Bieglo Group’s high-performance thermoplastic polymer, . A combination of these two materials — regolith and Aurum — will be used to create the printing material mixture required under harsh lunar environment.
Aurum is a high-heat resistant thermoplastic resin produced by Mitsui Chemicals Inc. (Tokyo, Japan) and marketed and distributed by Bieglo in Europe and BARplast LLC in the U.S. Noteworthy features include high temperature stiffness with a glass transition temperature (Tg) of 245ºC —which Bieglo claims is the highest class of Tg of any thermoplastic resin — and excellent sliding properties. Aurum’s coefficient of expansion is also stable up to 245ºC and can be controlled at an equivalent level to aluminum. Aurum also exhibits resistance to radiation, and has a stable coefficient of friction and low friction wear, making it resistant to abrasion caused by lunar dust. Moreover, says Bieglo, Aurum has an exceptionally clean TPI with very small outgas properties.
Related Content
-
Plant tour: Collins Aerospace, Riverside, Calif., U.S. and Almere, Netherlands
Composite Tier 1’s long history, acquisition of stamped parts pioneer Dutch Thermoplastic Components, advances roadmap for growth in thermoplastic composite parts.
-
Plant tour: Sekisui Aerospace, Orange City, Iowa, Renton and Sumner, Wash., U.S.
Veteran composites sites use kaizen and innovation culture to expand thermoplastic serial production, 4.0 digitization and new technology for diversified new markets.
-
Plant tour: Airbus, Illescas, Spain
Airbus’ Illescas facility, featuring highly automated composites processes for the A350 lower wing cover and one-piece Section 19 fuselage barrels, works toward production ramp-ups and next-generation aircraft.