Armacell expands PET foams production
Armacell has begun construction on expansion of its Thimister-Clermont PET Foam plant. This expansion will increase the site’s capacity to 180,000 cubic meters of eco-friendly engineered foam.
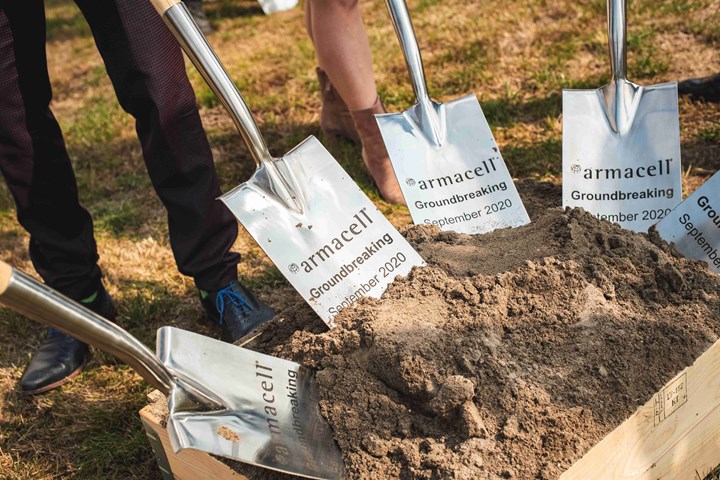
Armacell (Münster, Germany), a manufacturer of engineered foams for composite cores, reported on Sept. 14 that it has begun construction of two additional PET production lines at its PET foams headquarters in Thimister-Clermont, Belgium.
Armacell says this increase in production capacity, along with the company’s launch of a fourth PET production line in China earlier this year, will allow it to assert what it says is global market leadership in innovative, eco-friendly PET foam solutions for the composite industry.
The investment in Belgium will expand the existing facilities by one-third and include a production hall extension and new warehouse to accommodate output from four PET production lines.
Once the new lines are fully operational, Armacell says it will produce 180,000 cubic meters of PET foams per year at the Thimister-Clermont plant. According to the company, Armacell’s patented rPET processing technology enables the firm to produce these engineered foams from 100% recycled plastics.
“With this expansion, Armacell is once again demonstrating its commitment to the company’s central production site in Thimister-Clermont, where we have been producing PET foams since 2005, as well as to the future potential of our people and products,” says Thomas Kessel, Armacell’s managing director PET Foams.
Bart Janssen, vice president of Engineered Foams and Energy, notes: “This extension is the fourth in a series of investments for the production of PET foam products. The total capacity of our six PET foaming lines will enable us to support our global customers’ growth over the long term.”
Patrick Mathieu, president and CEO of the Armacell Group, explains the significance of the company’s international growth strategy: “The expansion of our PET manufacturing footprint increases our customer service levels globally. Our strategy allows us to focus on sustainable, profitable growth and develop and manufacture products with a positive impact on our community.”
Related Content
-
JEC World 2024 highlights: Thermoplastic composites, CMC and novel processes
CW senior technical editor Ginger Gardiner discusses some of the developments and demonstrators shown at the industry’s largest composites exhibition and conference.
-
CirculinQ: Glass fiber, recycled plastic turn paving into climate solutions
Durable, modular paving system from recycled composite filters, collects, infiltrates stormwater to reduce flooding and recharge local aquifers.
-
Sulapac introduces Sulapac Flow 1.7 to replace PLA, ABS and PP in FDM, FGF
Available as filament and granules for extrusion, new wood composite matches properties yet is compostable, eliminates microplastics and reduces carbon footprint.