Apply Carbon establishes mass recycled carbon fiber production facility
Apply Carbon has completed the commission of a fully automated production plant for recycled carbon fibers, with an estimated capacity of 4,000 metric tons.
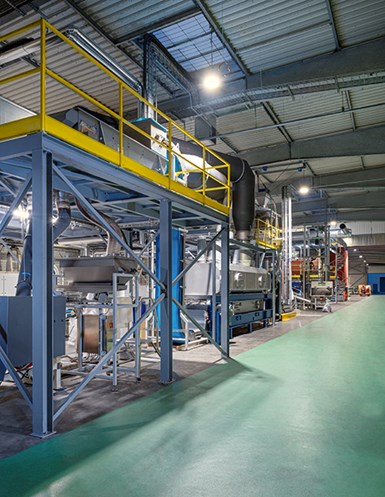
(Languidic, France) has recently established a 16,500-square-meter factory dedicated to carbon fiber recycling — alongside an acquisition of an additional 100,000 square meters of land for future expansion — to met growing demand across end markets. The factory produces close to 2,000 metric tons of recycled carbon fiber per year, with a nameplate capacity nearing 4,000 metric tons per year. It holds a stock of approximately 3,000 metric tons of raw materials, to promote high product quality, uniformity and security of supply.
Adjacent to the facility for recycled carbon fibers, Apply Carbon has also set up a dedicated production area for recycled para-aramid fibers, with an annual production capacity exceeding 700 metric tons. The additional capacity for milled and granulated aramid products aims to help meet rapidly increasing demand, whether for abrasion-resistant polymer compounds used in friction and wear applications or for aramid pulp used in low-wear and dust-free brake pads — areas that Apply Carbon has been serving for several years.
The company’s investment has also been geared toward establishing standards in terms of manufacturing and energy efficiency.
“Virtually all production processes — from the milling of raw materials to the granulation, sizing, cutting and packaging of finished products — have been automated to ensure cost-effectiveness and batch-to-batch reproducibility” says Hervé Cayuela, CEO of Apply Carbon.
Heat pumps are used to power the advanced drying ovens; a SCADA system has been implemented to minimize energy use across the entire facility; and the installation of 1-megawatts of solar power capacity will promote that more than half of the factory’s energy demand is covered by renewable energy.
The grand opening of Apply Carbon’s carbon fiber recycling facility in Plouay, France, is planned for January 2024.
Related Content
-
Hybrid process marries continuous, discontinuous composites design
9T Labs and Purdue applied Additive Fusion Technology to engineer a performance- and cost-competitive aircraft bin pin bracket made from compression-molded continuous and discontinuous CFRTP.
-
Infinite Composites: Type V tanks for space, hydrogen, automotive and more
After a decade of proving its linerless, weight-saving composite tanks with NASA and more than 30 aerospace companies, this CryoSphere pioneer is scaling for growth in commercial space and sustainable transportation on Earth.
-
From the CW Archives: Airbus A400M cargo door
The inaugural CW From the Archives revisits Sara Black’s 2007 story on out-of-autoclave infusion used to fabricate the massive composite upper cargo door for the Airbus A400M military airlifter.