Anmet installs first recycled wind turbine blade-based pedestrian bridge
Polish recycling company Anmet and partner GP Renewables Group aim to repurpose decommissioned composite wind turbine blades for infrastructure and consumer products.
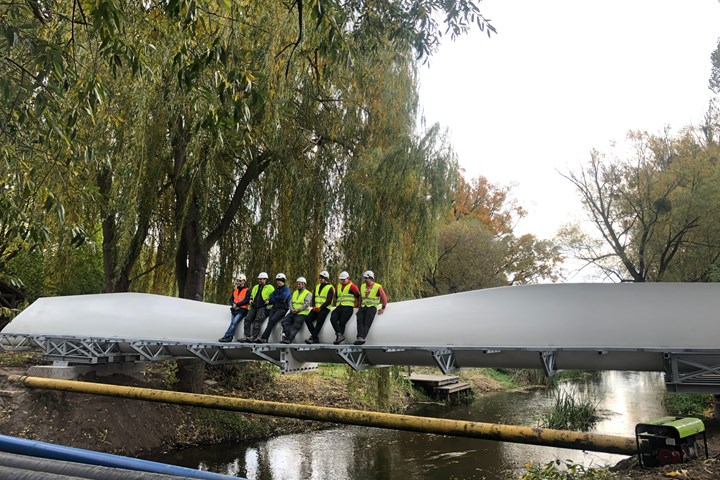
Recycling company (Szprotawa, Poland) and partner (Warsaw, Poland) announced on Oct. 21 that it has installed its first pedestrian and bicycle footbridge with girders made from repurposed composite wind turbine blades. The bridge is the culmination of three years’ research and work, and the footbridge structure has been patented with plans for commercialization.
According to Anmet, the concept is intended to serve as a solution to the problem of what to do with decommissioned turbine blades. Repurposing the blades in this way is said to serve as an alternative to either burying decommissioned blades or disposing of them using expensive or energy-consuming processes. This solution, Anmet says, gives blades a second life and avoids the raw material consumption and emissions related to production of new construction materials. The design is also intended to draw public attention to the issue of closed-loop waste management and energy transformation toward green energy.
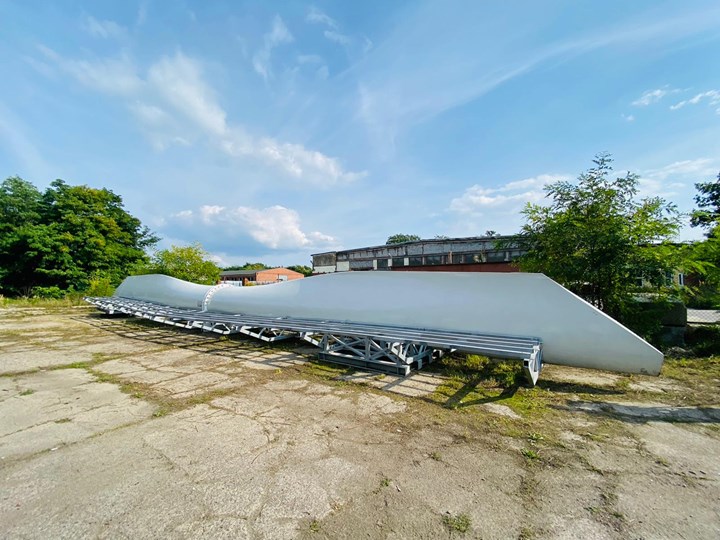
Founded by Andrzej Adamcio, Anmet has been providing services and solutions in the field of reuse and upcycling of blades for five years. It also provides blades cutting and recycling services for wind farm owners. Adamcio worked with university and industry partners like GP Renewables and the Rzeszów University of Technology (Poland) on research to confirm wind blades as viable replacement materials for wood or metal on bridge girders. Anmet now uses wind blades to build outdoor furniture (resulting in the ) as well as bridges.
The footbridge was installed on Oct. 21 on the Szprotawa River. The research for this project was funded by the European Funds – Intelligent Development from 2014-2020 through Rzeszów University of Technology.
Related Content
-
Sulapac introduces Sulapac Flow 1.7 to replace PLA, ABS and PP in FDM, FGF
Available as filament and granules for extrusion, new wood composite matches properties yet is compostable, eliminates microplastics and reduces carbon footprint.
-
The potential for thermoplastic composite nacelles
Collins Aerospace draws on global team, decades of experience to demonstrate large, curved AFP and welded structures for the next generation of aircraft.
-
Plant tour: Airbus, Illescas, Spain
Airbus’ Illescas facility, featuring highly automated composites processes for the A350 lower wing cover and one-piece Section 19 fuselage barrels, works toward production ramp-ups and next-generation aircraft.