Airtech Advanced Materials Group partners with CEAD
The partnership enables Airtech Advanced Materials Group to incorporate CEAD Flexbot systems into its advanced manufacturing portfolio.
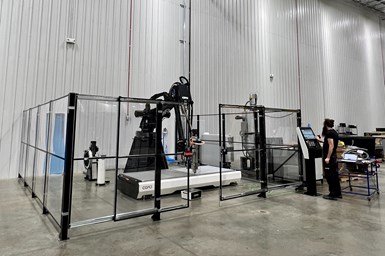
CEAD Flexbot located in Airtech’s facility. Photo Credit: Airtech
Airtech Advanced Materials Group (Huntington Beach, Calif., U.S.) has expanded its additive manufacturing (AM) capabilities through a partnership with CEAD (Delft, Netherlands). The company has integrated CEAD’s Flexbot systems into its advanced manufacturing portfolio, signifying an advancement in its technological capabilties.
CEAD’s Flexbot, a robot-based, large-format 3D printing solution, offers a 3 × 1-meter build volume, CNC milling capabilities and Dynamic Flow Control, making it an all-in-one advanced solution for precision manufacturing. The technology resides in Airtech’s Additive Manufacturing Center of Excellence in Springfield, Tenn., U.S. It plays a critical role in developing resins for 3D printing and exploring applications across diverse market segments.
“CEAD’s fully integrated, robotic printing and milling hybrid solution equips Airtech to support its continued growth in the additive manufacturing [AM] market segment, providing unparalleled support for CEAD and Airtech customers worldwide,” says Gregory Hayes, director of additive manufacturing at Airtech.
Additionally, Airtech’s AM experts are set to deepen their knowledge and expertise through daily utilization and planned developmental activities with the CEAD Flexbot. This will further improve their ability to support global customers using Airtech’s Dahltram resins with CEAD Flexbot and Robot Extruder solutions.
Related Content
-
Hybrid process marries continuous, discontinuous composites design
9T Labs and Purdue applied Additive Fusion Technology to engineer a performance- and cost-competitive aircraft bin pin bracket made from compression-molded continuous and discontinuous CFRTP.
-
Eaton developing carbon-reinforced PEKK to replace aluminum in aircraft air ducts
3D printable material will meet ESD, flammability and other requirements to allow for flexible manufacturing of ducts, without tooling needed today.
-
Industrializing additive manufacturing in the defense/aerospace sector
GA-ASI demonstrates a path forward for the use of additive technologies for composite tooling, flight-qualified parts.