
Automotive Tier 1 Katcon developed its multi-material, composites-intensive electric vehicle (EV) battery enclosure concept based on cost targets and mechanical properties required by OEMs the company works with. The result is a modular “toolbox” of process and material options. Photo Credit, all images: Katcon
As automakers dive more deeply into the electric vehicle (EV) market, fabricators and Tier suppliers continue to come up with composite solutions for protective battery enclosures. One company taking a multi-material, flexible approach to this design is automotive Tier 1 (Monterrey, Mexico).
Katcon was established in 1993 as a joint venture with General Motors Mexico (which later spun off into Delphi Automotive) and focused on exhaust systems and catalytic converters for the automotive industry. In the early 2000s, Katcon expanded, consolidating all of Delphi’s exhaust systems businesses in North America. Eventually, Katcon would also acquire Delphi’s global exhaust business, currently operating 11 manufacturing sites and five tech centers, in eight countries.
“Katcon is a family owned business founded by my father 30 years ago. Overnight, it went from being a Mexican, North America-only company to a global business,” says Eduardo Turner, new ventures director at Katcon Global. “Now, we are a world-class Tier 1 in the automotive and transportation industry.”
Over the past several years, Katcon has made efforts to diversify its capabilities beyond exhaust systems, including thermal insulation and, most recently, advanced composites technologies.
Turner explains, “We decided to invest in an Advanced Materials division five or six years ago primarily because we have a front row seat to the evolvement of the automotive industry, and we started seeing shifts both toward lightweight vehicles and toward electrification, which itself implies a need for lightweight, more complex modern materials and solutions for the industry.”
At the same time, the company has also been evolving from solely a manufacturing company to offer more engineering and design services. This combination led Katcon to identify EV battery enclosures as its initial focus for entering the automotive composites market. “We wanted to provide our customers with value-add solutions, rather than just welding or providing manufactured products,” Turner says. “Battery enclosures are complex, structurally integral parts that bond well with the problem-solving, engineering and design capabilities we have built over the past decade.”
In late 2020, Katcon began working with engineering partner (Royal Oak, Mich., U.S.) on its own battery enclosure solutions.
Developing a scalable, material-agnostic battery enclosure
Katcon started by talking with automotive OEMs, Turner explains. “The battery enclosure was designed for OEM requirements and load cases — this is not just an idea or a concept. The original goal for the project was to design, develop and manufacture a state-of-the-art product that complied with the most rigorous OEM and regulatory requirements and load cases.”
Based on these conversations, one of Katcon’s main objectives for this product has always been flexibility. “We knew we needed to make a solution that could be easily adaptable to different sizes, different regions and different requirements, and, last but not least, it also has to be cost-effective,” Turner says.
According to Juan Armendariz, general manager at Katcon Advanced Materials, the resulting solution is a multi-material, scalable “toolbox” that can be adapted based on mechanical and cost requirements, size, volume and other factors. “We knew from the beginning that we didn’t want to focus on a single product design, because the requirements and best practices for EVs and batteries keep changing. The industry doesn’t yet have a ‘best practice solution’ to follow,” he says. “We wanted to focus on building the know-how and understanding the tradeoffs and having solutions for different cases.”
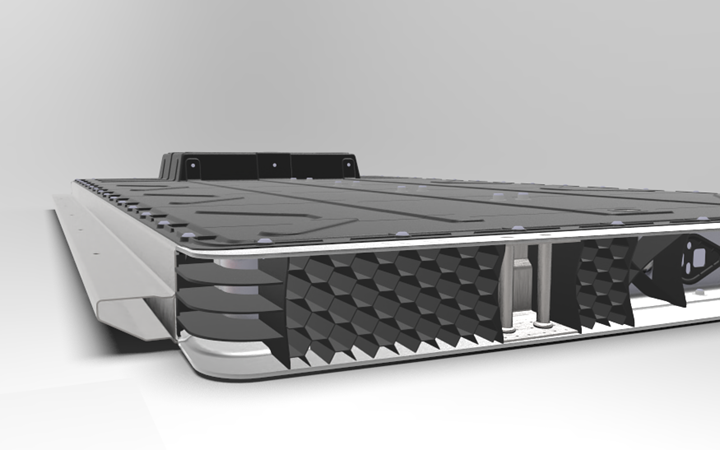
The GFRTP honeycomb shape on the front header is designed for energy absorption and optimal stiffness. In Katcon’s generic concept, this part is constructed from PA6 organosheet co-molded with steel brackets and then injection overmolded with glass fiber/PA6. The properties can be tuned by adjusting the hexagon diameter, rib thickness or the creation of patterns or zones within the structure.
The development process was a collaborative effort, Armendariz emphasizes, including expertise and cooperation from Forward Engineering, steel manufacturer (Luxembourg), materials supplier DSM Engineering Materials (Emmen, Netherlands), fastener supplier (Bloomfield Hills, Mich., U.S.), composites molding equipment specialist Engel (St. Valentin, Austria), resin supplier Hexion (Columbus, Ohio, U.S.), SMC specialist IDI Composites International (Noblesville, Ind., U.S.), adhesives supplier Sika (Madison Heights, Mich., U.S.), machine supplier (Ditzingen, Germany) and full line automation and assembly lines supplier (Zurich, Switzerland).
Almost a year of design iterations and testing followed. Testing started virtually, followed by physical testing for stiffness, fire resistance, moisture absorption, electrical conductivity/EMI shielding, pressure and crash requirements. Ultimately, Katcon and its team developed a concept demonstrator that showcases the range of material and process options that Katcon can use to design an OEM-specific battery enclosure.
The general design comprises a rigid steel ladder frame structure sealing the sides of an interior weatherproof box. In Katcon’s generic concept, the insulated box is made from glass fiber composites — specifically, a sheet molding compound (SMC) top panel and compression molded bottom panel — and the rigid outer frame is built from steel beams capped with a glass fiber-reinforced thermoplastic (GFRTP) injection overmolded organosheet front header. The GFRP box is made up of top and bottom panels and designed with fire-resistant resins; their purpose is to safely encase the batteries and protect them from the environmental conditions while containing and managing the internal enclosure environment. Steel crossmembers hold the individual batteries in place inside the box. The outer steel beams bear most of the load in a crash event, while the GFRTP header acts as an energy absorber and allows for various molded-in features as needed.
“Once we had the materials and design narrowed down, it was a matter of figuring out how to put it together, which was not easy at all,” Armendariz admits. Given the number of individual parts, and the range of materials used, joining and adequate sealing were key, and complex. Adhesive bonding, mechanical joining and welding were all evaluated and are now part of the toolbox.
The concept also showcases Katcon’s range of in-house processing capabilities, which include forming and welding metal, 3D printing metals and plastics, compression molding, high-pressure resin transfer molding (HP-RTM), organosheets hybrid molding, injection molding, spray transfer molding, reaction injection molding (RIM), thermoplastic RTM and more. “We have a good range of capabilities — that’s what we built the Santa Catarina facility for,” Armendariz says. Products can be developed and built in-house, from concept to prototypes and full production.
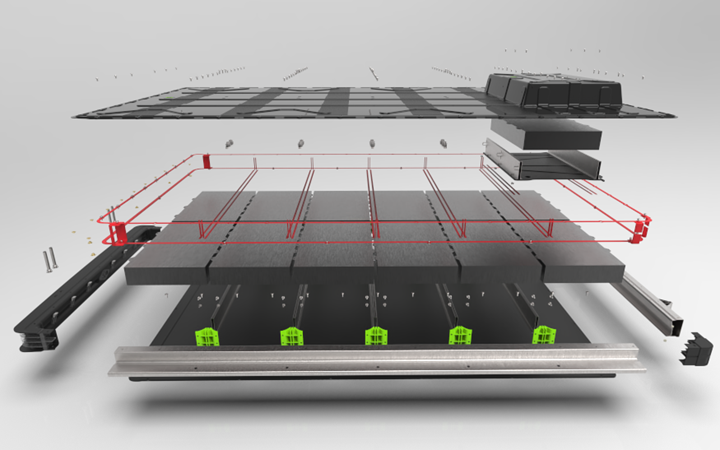
To assemble the various components involved in its battery enclosure design, Katcon says it has explored and validated joining methods including welding, adhesive bonding and mechanical joining methods.
In addition, though carbon fiber could be used in the design for lighter weight, Katcon generally favors glass fiber for battery enclosures, he notes. “The point is not to be lightweight just for the sake of lightweight,” Armendariz says. “The battery enclosure is already only a small fraction of the weight of the overall battery pack, and as battery modules are [developed to] store more energy and be denser, the weight of the battery enclosure is even less critical. What is critical is efficient use of materials for high performance that is sustainable and cost-effective.” With carbon fiber “you may save a few percentage points of weight, but it’s going to be very expensive,” he adds.
With this concept in hand, Katcon is now working with OEMs to tailor the solution it has come up with to specific applications, with anticipated volumes of up to 120,000 units per year. There are three types of customers that Katcon is working with to commercialize its battery enclosures, Turner says: Automakers looking to transition their internal combustion engine (ICE) vehicles to EVs, newer EV-native automakers and startups working in emerging markets like EV delivery vehicles or buses.
“In the end, we have a toolbox of materials, technology and know-how,” Armendariz says. “The generic concept was built to meet a range of existing requirements, and shows how we can use different materials made with different processes joined together by different joining methods, the combination of which is a big part of why this solution works.”
Related Content
ECOHYDRO project to enable recyclable composites for hydrogen storage
With the involvement of two schools from the Institut Mines-Télécom, the 4-year project aims to improve the intrinsic properties of a composite material based on Elium via four concrete demonstrators.
Read MoreBioabsorbable and degradable glass fibers, compostable composite parts
ABM Composite offers sustainable options and up to a 60% reduction in carbon footprint for glass fiber-reinforced composites.
Read MoreSyensqo becomes new Solvay specialty materials company
Syensqo represents what was Solvay Composite Materials, focused on delivering disruptive material technologies and supporting growing customer needs.
Read MoreDawn Aerospace reusable rocket-powered aircraft flies twice in one day
Eighth and ninth flights of composites-intensive Mk-II Aurora reach an altitude of 63,000 feet, demonstrates same-day reusability capability for rocket-powered systems.
Read MoreRead Next
VIDEO: High-volume processing for fiberglass components
Cannon Ergos, a company specializing in high-ton presses and equipment for composites fabrication and plastics processing, displayed automotive and industrial components at CAMX 2024.
Read MoreComposites end markets: New space (2025)
Composite materials — with their unmatched strength-to-weight ratio, durability in extreme environments and design versatility — are at the heart of innovations in satellites, propulsion systems and lunar exploration vehicles, propelling the space economy toward a $1.8 trillion future.
Read More“Structured air” TPS safeguards composite structures
Powered by an 85% air/15% pure polyimide aerogel, Blueshift’s novel material system protects structures during transient thermal events from -200°C to beyond 2400°C for rockets, battery boxes and more.
Read More