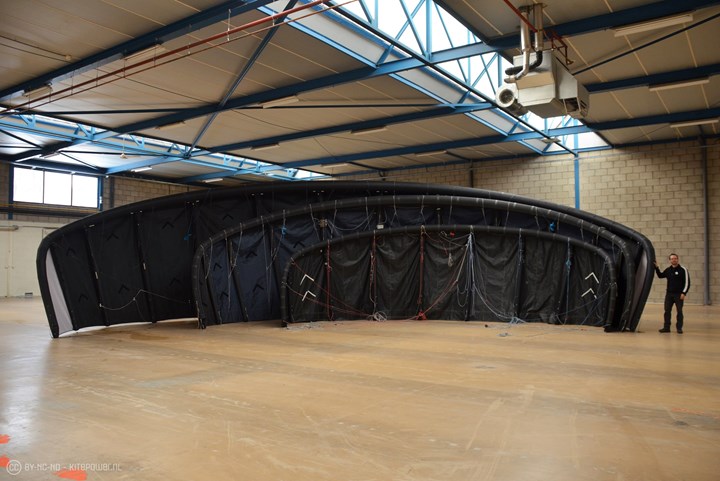
Photo Credit, all images: Kitepower
Founded by researchers at Delft University of Technology (TU Delft, Netherlands), startup company is working toward development and deployment of a kite-based, airborne wind energy (AWE) system, designed to be a mobile, low-footprint renewable energy solution.
The researchers’ first 20-kilowatt (kW) proof of concept was demonstrated in 2007, and the company was officially co-founded by researchers Johannes Peschel and Roland Schmehl in 2016. This year, Kitepower raised well over its €700,000 target in a recent crowdfunding campaign aiming to commercialize the company’s Falcon model. Falcon is a 100-kW AWE system said to be able to generate 450 megawatt-hours (MWh) of electricity per year, enough to power 150 homes.
Kitepower’s patented technology, in development at TU Delft since the 1990s, features an airborne kite and control unit that are tethered to a fixed ground station, which converts the mechanical energy of the kite into electrical power. The control unit controls the trajectory of the kite in the air — the kite is designed to fly in a figure-eight pattern to achieve maximum pulling force and mechanical energy — and the ground station also serves to reel the kite and tether in and out as needed.
The kite features an inflatable membrane wing attached to a rigid, tube-shaped fiberglass composite skeleton, a combination designed to maximize strength with light weight. According to Peschel, carbon fiber was also considered but fiberglass was chosen for more flexibility while achieving the required strength. The skeleton is made up of 12 hollow tube structures connected via custom-made aluminum connectors. The fiberglass composite tubes are designed by Kitepower, manufactured by an external partner and then assembled by the Kitepower team.
Lying flat, the fully assembled kite measures 60 square meters, and achieves an average flight speed of about 110 kilometers per hour when airborne. The kite is held aloft by a tether made from ultra-high molecular weight polyethylene (UHMWPE) Dyneema fibers.
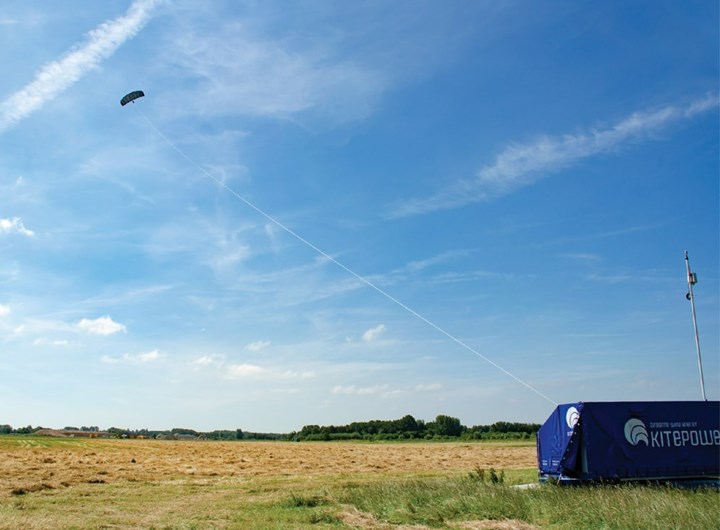
The Kitepower system is said to require only one square meter of ground space for the control unit, and can be easily integrated into existing power grids. Ultimately, the solution is designed to provide a renewable energy solution that, compared to solar or wind energy, is more easily installed and transported, uses fewer materials to manufacture and takes up less physical space. Depending on wind conditions, the system can also generate electricity day and night, regardless of weather conditions.
According to Peschel, Kitepower currently operates in shared factory space in Delft, as the team focuses on a short-term pilot project with its first Falcon model. In 2023, after achieving EU regulatory certifications for the technology, the company plans to begin scale-up of its operations in order to begin producing 100-kW Falcon models for permanent installation by third-party customers by 2024. Current energy company partners include Greener (Amsterdam, Netherlands), Enerwhere Sustainable Energy (Dubai, United Arab Emirates) and Veida Renewables (Moorabin, Australia). Once Falcon models are proven to be successful, Kitepower aims to scale up the technology further to the ultimate goal: a utility-scale, 500-kW Eagle model.
Related Content
Composites end markets: Batteries and fuel cells (2024)
As the number of battery and fuel cell electric vehicles (EVs) grows, so do the opportunities for composites in battery enclosures and components for fuel cells.
Read MorePlant tour: Hexagon Purus, Kassel, Germany
Fully automated, Industry 4.0 line for hydrogen pressure vessels advances efficiency and versatility in small footprint for next-gen, sustainable composites production.
Read MoreHonda begins production of 2025 CR-V e:FCEV with Type 4 hydrogen tanks in U.S.
Model includes new technologies produced at Performance Manufacturing Center (PMC) in Marysville, Ohio, which is part of Honda hydrogen business strategy that includes Class 8 trucks.
Read MoreSRI develops scalable, infiltration-free ceramic matrix composites
Work in two DOE projects is demonstrating C/C-SiC produced in 3-5 days with <5% shrinkage, <10% porosity and 50% the cost of conventional C/C and C/C-SiC.
Read MoreRead Next
Composites end markets: New space (2025)
Composite materials — with their unmatched strength-to-weight ratio, durability in extreme environments and design versatility — are at the heart of innovations in satellites, propulsion systems and lunar exploration vehicles, propelling the space economy toward a $1.8 trillion future.
Read More“Structured air” TPS safeguards composite structures
Powered by an 85% air/15% pure polyimide aerogel, Blueshift’s novel material system protects structures during transient thermal events from -200°C to beyond 2400°C for rockets, battery boxes and more.
Read MorePlant tour: Daher Shap’in TechCenter and composites production plant, Saint-Aignan-de-Grandlieu, France
Co-located R&D and production advance OOA thermosets, thermoplastics, welding, recycling and digital technologies for faster processing and certification of lighter, more sustainable composites.
Read More