IACMI Winter 2020 Meeting
The Institute for Advanced Composites Manufacturing Innovation (IACMI) held its winter meeting in Dayton, Ohio, U.S. January 21-23, updating its membership on the public-private institute's efforts to accelerate composites design and manufacturing.
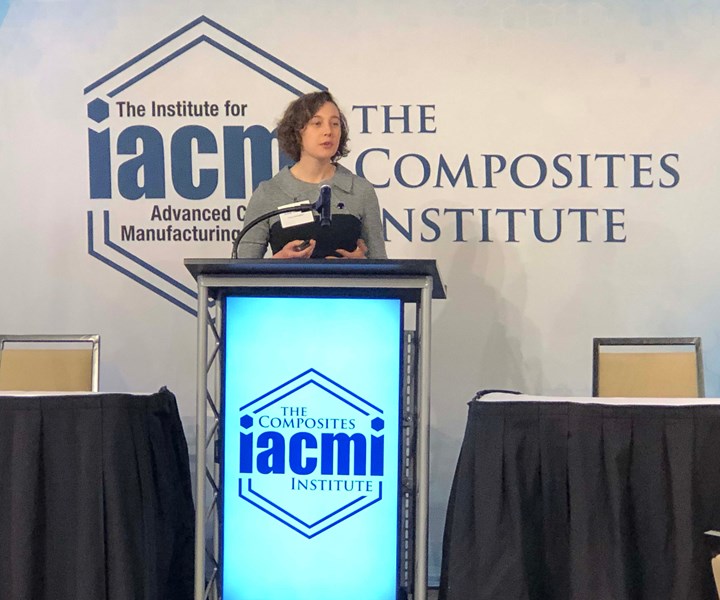
Julia Attwood, head of advanced materails a Bloomber NEF, delivered the opening keynote at IACMI’s winter meeting, addressing the role of carbon fiber in energy and transportation in the coming years with regard to capacity, pricing and demand. CW photo | Scott Francis
The Institute for Advanced Composites Manufacturing Innovation (IACMI, Knoxville, Tenn., U.S.), held its winter membership meeting in Dayton, Ohio, U.S. January 21-23 and provided an update on activities of the public-private US Department of Energy consortium, which works to accelerate material and processing technologies for composites manufacturing.
The meeting celebrated IACMI’s past successes and looked ahead to the institute’s future, encouraging collaboration between federal and state governments, research institutes and private partners. A particular focus was on Ohio, which is home to more than 20 IACMI members. Ohio Lt. Gov. Jon A. Husted addressed the importance of technology to the state of Ohio, emphasizing a need for collaboration and workforce development — a theme that ran through much of the event.
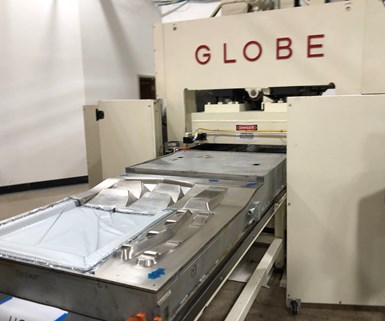
UDRI Dayton Composites Center’s next-gen Rapidclave from Globe Machine Manufacturing Co. CW photo | Scott Francis
IACMI’s event kicked off with a tour of the University of Dayton Research Institute’s (UDRI) Dayton Composites Center (Kettering, Ohio, U.S.), which is located in the building that previously served as the National Composites Center. UDRI along with its industry partners demonstrated several of the center’s capabilities including tailored fiber placement (TFP) using Tajima (Tokyo, Japan) and ZSK Stickmaschinen GmbH (ZSK, Krefeld, Germany) TFP equipment and a next-gen Rapidclave from Globe Machine Manufacturing Co. (Tacoma, Wash., U.S.). Daniel Allman director, composites business development for Globe Machine demonstrated operation of the Rapidclave with snap cure prepregs on an automotive hood mold and teased the forthcoming installment of a second, aerospace-centric machine.
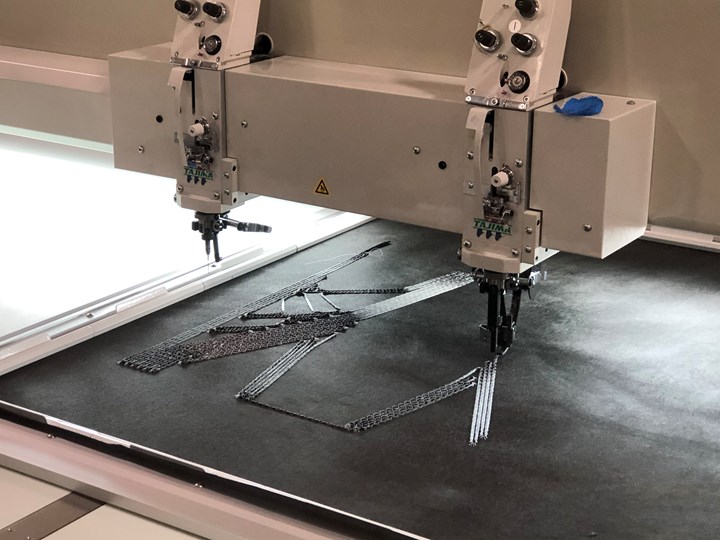
UDRI Dayton Composites Center’s capabilities include tailored fiber placement (TFP) equipment from Tajima (Tokyo, Japan) and ZSK Stickmaschinen GmbH (ZSK, Krefeld, Germany). CW photo | Scott Francis
The winter meeting’s opening keynote was delivered by Julia Attwood, head of advanced materials at Bloomberg NEF, who discussed the growing role of carbon fiber in energy and transportation. Attwood anticipates carbon fiber prices will halve by 2030 and production will double by 2025 driven by an increase in demand driven by the growing wind energy and electric vehicle (EV) markets.
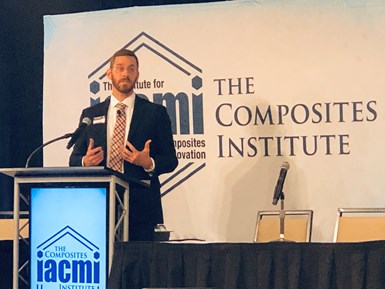
Michael Guckes, chief economist for Gardner Business Intelligence discusses the economic state of the composites industry. CW photo | Scott Francis
Michael Guckes, chief economist for Gardner Business Intelligence, delivered the second day keynote, offering economic insights into the state of the composite industry today. Guckes discussed the relative health of the aerospace industry in spite of the difficulties surrounding Boeing’s 737 Max crisis and encourages supplier and fabricators to think wholistically about their capabilities, watching the markets for new opportunities in growth sectors such as consumer electronics.
Additional sessions and workshops focused on circular economy opportunities for composites and rapid low-cost manufacturing for aerospace structures. Andrea Helbach structures manufacturing team lead at United States Air Force spoke about an emphasis on low cost attritable aircraft technology (LCAAT). The initiative will focus on utilizing low cost UAVs created using different tooling approaches with the goal of breaking the cost growth curve and fielding new systems faster. (Learn more). Soydan Ozcan of the Oak Ridge National Laboratory (ORNL), Chuck Ludwig of CHZ technologies, Mohamed Buguettaya of BASF and Jordan Harris of Vartega provided an overview of recycling efforts and opportunities in the composites industry.
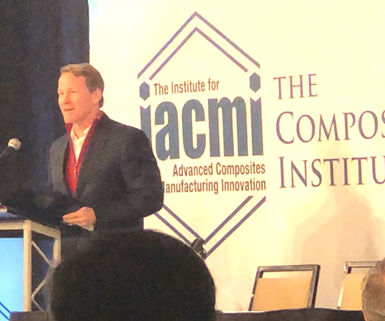
“Those who collaborate best are those who win.” Ohio Lt. Gov. Jon A. Husted delivers closing keynote at IACMI Winter 2020 Members Meeting. CW photo | Scott Francis
Ohio Lt. Gov. Jon A. Husted offered a closing keynote, addressing the importance of technology to the state of Ohio, emphasizing a need for collaboration and workforce development — a theme that ran through much of the event.
Workforce development is a large focus for IACMI. The institute was recently awarded a $5 million grant over the course of the next three years to expand a composites training program begun by (DTC; Kaysville, Utah, U.S.) to four additional locations across the U.S. (Learn more).
Related Content
Bioabsorbable and degradable glass fibers, compostable composite parts
ABM Composite offers sustainable options and up to a 60% reduction in carbon footprint for glass fiber-reinforced composites.
Read MoreLife cycle assessment in the composites industry
As companies strive to meet zero-emissions goals, evaluating a product’s carbon footprint is vital. Life cycle assessment (LCA) is one tool composites industry OEMs and Tier suppliers are using to move toward sustainability targets.
Read MoreEuropean boatbuilders lead quest to build recyclable composite boats
Marine industry constituents are looking to take composite use one step further with the production of tough and recyclable recreational boats. Some are using new infusible thermoplastic resins.
Read MorePlant tour: Arris Composites, Berkeley, Calif., U.S.
The creator of Additive Molding is leveraging automation and thermoplastics to provide high-volume, high-quality, sustainable composites manufacturing services.
Read MoreRead Next
Plant tour: Daher Shap’in TechCenter and composites production plant, Saint-Aignan-de-Grandlieu, France
Co-located R&D and production advance OOA thermosets, thermoplastics, welding, recycling and digital technologies for faster processing and certification of lighter, more sustainable composites.
Read MoreVIDEO: High-volume processing for fiberglass components
Cannon Ergos, a company specializing in high-ton presses and equipment for composites fabrication and plastics processing, displayed automotive and industrial components at CAMX 2024.
Read MoreAssembling the Multifunctional Fuselage Demonstrator: The final welds
Building the all-thermoplastic composite fuselage demonstrator comes to an end with continuous ultrasonic welding of the RH longitudinal fuselage joint and resistance welding for coupling of the fuselage frames across the upper and lower halves.
Read More