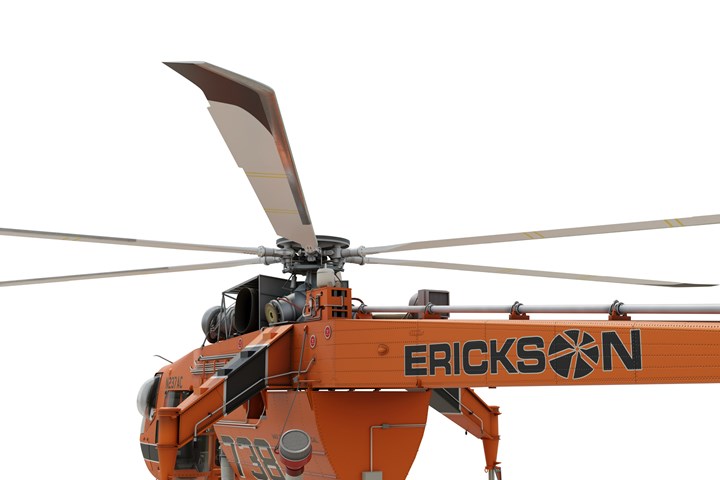
Aviation and defense OEM and services supplier .’s (Portland, Ore., U.S.) S-64 Air Crane six-blade helicopter was first certified in the 1960s and built for decades with manual, labor-intensive aluminum rotor blades. Erickson partnered with Toray Advanced Composites (Morgan Hill, Calif., U.S.) with the goal of using composites to develop a cost-effective, higher performance blade requiring lower maintenance costs.
The first challenge, according to Toray Advanced Composites, was the limited number of FAA-approved blade materials. The existing qualified materials were prohibitively expensive for Erickson, and required autoclave cure.
Over a period of several years, Toray helped Erickson identify and qualify materials and processes to develop higher-performance rotor blades with significantly reduced manufacture and maintenance costs.
According to Toray, the blade materials needed to match or exceed many of the requirements of the original aluminum blades including matching the original mass and inertial properties; primary load tensile strength and stiffness; stiffness critical for flexion and flutter; and shear strength and stiffness at the blade root.
Ultimately, Toray’s BT250E-6 epoxy prepreg was selected as the material for the blades, meeting modulus, cure, strength and stiffness requirements. Glass and carbon fiber materials using BT250E-6 were comprehensively tested and qualified as both autoclave and out-of-autoclave (OOA) capable, with a 126°C (260°F) cure, by the National Institute for Aviation Research (NIAR, Wichita, Kan., U.S.). BT250E-6 now has an FAA-accepted database on carbon IM-7 uni-directional (UD) tape, S2-glass and AS-4C plain weave. According to Toray, BT250E-6 is the only OOA, FAA-approved composite solution for rotor blades.
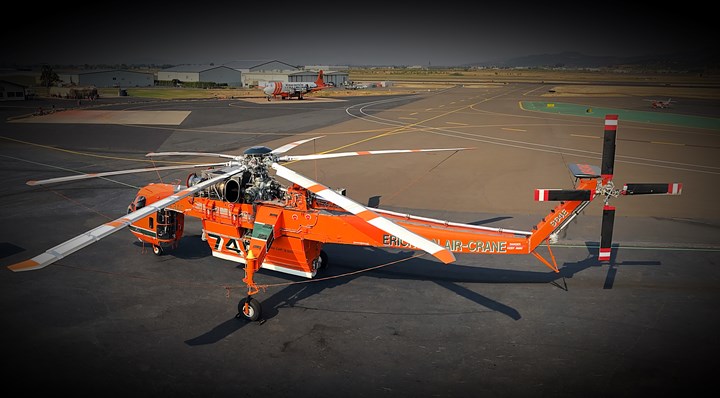
Erickson’s composite rotor blades are designed with multiple layers of composites, Toray says, with each layer applied in a specific pattern and orientation to maximize strength and to match the legacy aluminum blades’ mechanical properties. Five epoxy-based materials are used per blade: graphite UD tape, fiberglass UD tape, graphite fabric, fiberglass fabric and Toray Cetex TC235 LS material for lightning strike protection.
For each blade, Erickson lays up the material layers, consolidating OOA under vacuum in a specially built oven at Erickson’s composites manufacturing facility.
According to Toray, the new composite blades deliver an improved production cycle, reduced initial and lifecycle operating costs, fuel savings and performance gains, reduced vibration and more. The blades reportedly also reduce the amount of engine torque required to lift objects out of the water, as well.
Related Content
-
Otto Aviation launches Phantom 3500 business jet with all-composite airframe from Leonardo
Promising 60% less fuel burn and 90% less emissions using SAF, the super-laminar flow design with windowless fuselage will be built using RTM in Florida facility with certification slated for 2030.
-
Plant tour: Teijin Carbon America Inc., Greenwood, S.C., U.S.
In 2018, Teijin broke ground on a facility that is reportedly the largest capacity carbon fiber line currently in existence. The line has been fully functional for nearly two years and has plenty of room for expansion.
-
Revisiting the OceanGate Titan disaster
A year has passed since the tragic loss of the Titan submersible that claimed the lives of five people. What lessons have been learned from the disaster?