From the CW Archives: The tale of the thermoplastic cryotank
In 2006, guest columnist Bob Hartunian related the story of his efforts two decades prior, while at McDonnell Douglas, to develop a thermoplastic composite crytank for hydrogen storage. He learned a lot of lessons.
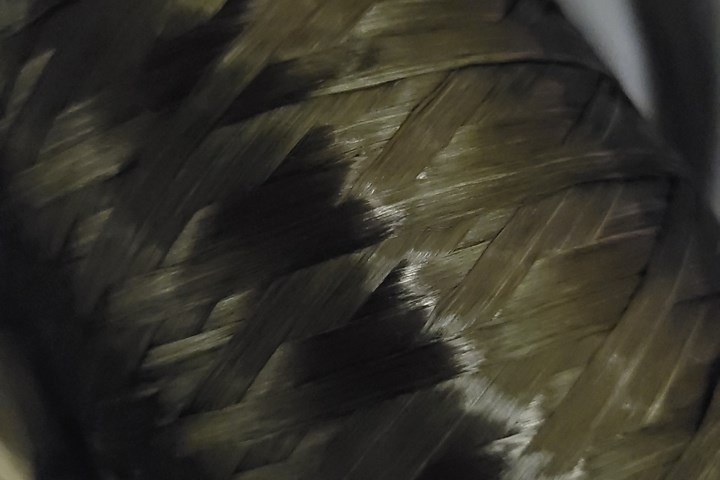
During my tenure as editor-in-chief of ÂÌñÏׯÞ, there was a handful of times when, following the publication of a story about a new material, technology or process, I’d receive an email from a reader, complimenting us on the story.
This compliment would then be followed by something along these lines: “But you know this technology isn’t really new. Back in 1983, when I was with XYZ Corp., we use that same resin, that same fiber and that same manufacturing process to make this structure that no one thought we could make. It was a monumentally huge effort and no one had done it before and no one has done it since. Why don’t you write about that?”
Sometimes we did. And sometimes we asked that emailer to write the story themselves. Such was the case with a Composites: Past, Present and Future column we published in 2006, a few months before I arrived on the CW scene: “McDonnell Douglas composite cryotanks — a personal history”
The author was Bob Hartunian, a former McDonnell Douglas and then Boeing engineer who is now a Boeing Technical Fellow (ret.). Hartunian’s story describes his role in the bold decision to develop a thermoplastic composite crytank for hydrogen storage as part of the National AeroSpace Plane (NASP) program.
What follows is the gradual realization of Hartunian and his teammates that thermoplastics were not (at the time) feasible as a material to store hydrogen at cryogenic temperatures.
Hartunian’s sense of humor is evident in his storytelling — keep an eye out for the autoclave that peeled the paint off a wall — and his tale is a reminder that innovation and creativity have long been a vital part of the composites manufacturing community.
Enjoy this jump back in time.
Related Content
-
The next evolution in AFP
Automated fiber placement develops into more compact, flexible, modular and digitized systems with multi-material and process capabilities.
-
Reinforcing hollow, 3D printed parts with continuous fiber composites
Spanish startup Reinforce3D’s continuous fiber injection process (CFIP) involves injection of fibers and liquid resin into hollow parts made from any material. Potential applications include sporting goods, aerospace and automotive components, and more.
-
A new era for ceramic matrix composites
CMC is expanding, with new fiber production in Europe, faster processes and higher temperature materials enabling applications for industry, hypersonics and New Space.