Fighter jet development and the "need" for the F-35
The F-35 is expensive, behind schedule and here to stay, but Textron Airland's new Scorpion might better show how a plane should be developed.

Although several years behind schedule and many billions of dollars over budget, the composites-intensive F-35 Lightning II fighter jet is expected to be a core of the U.S. and its allies' fighting arsenal for many years to come.
The Soviet Union tested its first nuclear weapon on Aug. 29, 1949, about five to 10 years before the United States expected it would. The test effectively ended the U.S. monopoly on fission-based nuclear weaponry and launched the decades-long arms race that became the hallmark of the Cold War.
The natural tendency for the Americans was to attempt to regain the upper hand, either by building more fission weapons in effort to stay ahead of the Soviets, or build a bigger weapon. The bigger weapon would be a thermonuclear or fusion-based bomb, which until 1949 existed on the drawing board only as a conceptual weapon. A thermonuclear bomb, fueled by hydrogen, would be orders of magnitude more powerful and destructive than the uranium- and plutonium-based bombs dropped on Japan at the end of World War II, but would require a significant technical effort to develop and test. President Harry Truman faced a simple question: Whether or not to try and make a thermonuclear weapon, or just build more weapons based on the “old” fission technology.
Robert Oppenheimer, physicist and “father” of the atomic bomb developed in the Manhattan Project, actually opposed development of a thermonuclear weapon. It was, he argued, not a battlefield weapon, but a tool used only for destruction of entire cities and regions. It would be, in short, too costly to develop and too destructive to apply. However, faced with the prospect that the Soviets would certainly not show similar restraint, Truman had no choice but to authorize a thermonuclear weapon development program. The U.S. successfully tested its first hydrogen bomb in 1954, followed by the first Soviet hydrogen bomb test in 1955.
There are, today, shades of some of the same “race” logic at work with the F-35 Lightning II Joint Strike Fighter, being built by Lockheed Martin for sale to the U.S. and several partner countries. The composites-intensive F-35, as has been well documented, is about seven years behind schedule and billions of dollars over budget. This has prompted calls for the program’s end, which seems unlikely given that the F-35 and its variants are in testing and early production. The argument has also been made that many of the current jet fighters in the U.S. arsenal can do what the F-35 can do.
Indeed, the U.S. and its allies have relied on fourth-generation fighters like the Boeing F/A-18E/F Super Hornet, the Eurofighter Typhoon, the Dassault Rafale and the Lockheed Martin F-22 Raptor for about 20 years. These planes have served well and continue to perform — and might be adequate for the foreseeable future. The problem is that, like it or not, other countries that may or may not be antagonistic to the U.S. and its allies are developing fifth-generation fighters on par with the F-35. These include the Russian Sukhoi PAK FA and the Chinese Chengdu J-20, so keeping up with the competition seems to demand a fighter like the F-35.
But is fighter jet development done at any cost? Had the U.S. Congress known up front what the true cost of the F-35 would be, it likely would not have authorized it. And it would be nice to think that the U.S. and its allies had gotten so good at airplane development that cost and time overruns were the exception, not the rule. But the F-35 is a complex system, and complex systems invite unpredictability.
There is hope, however, in the fighter jet development world for creativity, speed and efficiency. Witness in particular the recently debuted Scorpion, an all-composite, tandem-seat, twin tail tactical jet fighter, self-funded and developed by (Wichita, Kan.), a joint venture between Textron and Airland Enterprises. The plane went from concept to first flight in just two years, was designed and produced in secret and demonstrates clearly the potential for efficient and on-time fighter development. Scorpion is not an F-35 replacement, but it does prove what’s possible and might be more a harbinger of what’s to come.
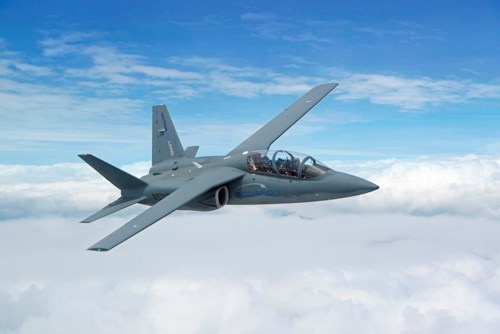
The Textron Airland LLC Scorpion fighter, which was introduced in July 2014, was self-funded and evolved from concept to first flight in just two years.
Related Content
Combining multifunctional thermoplastic composites, additive manufacturing for next-gen airframe structures
The DOMMINIO project combines AFP with 3D printed gyroid cores, embedded SHM sensors and smart materials for induction-driven disassembly of parts at end of life.
Read MoreIndustrializing additive manufacturing in the defense/aerospace sector
GA-ASI demonstrates a path forward for the use of additive technologies for composite tooling, flight-qualified parts.
Read MoreComposites manufacturing for general aviation aircraft
General aviation, certified and experimental, has increasingly embraced composites over the decades, a path further driven by leveraged innovation in materials and processes and the evolving AAM market.
Read MorePlant tour: Airbus, Illescas, Spain
Airbus’ Illescas facility, featuring highly automated composites processes for the A350 lower wing cover and one-piece Section 19 fuselage barrels, works toward production ramp-ups and next-generation aircraft.
Read MoreRead Next
All-recycled, needle-punched nonwoven CFRP slashes carbon footprint of Formula 2 seat
Dallara and Tenowo collaborate to produce a race-ready Formula 2 seat using recycled carbon fiber, reducing CO2 emissions by 97.5% compared to virgin materials.
Read More“Structured air” TPS safeguards composite structures
Powered by an 85% air/15% pure polyimide aerogel, Blueshift’s novel material system protects structures during transient thermal events from -200°C to beyond 2400°C for rockets, battery boxes and more.
Read MorePlant tour: Daher Shap’in TechCenter and composites production plant, Saint-Aignan-de-Grandlieu, France
Co-located R&D and production advance OOA thermosets, thermoplastics, welding, recycling and digital technologies for faster processing and certification of lighter, more sustainable composites.
Read More