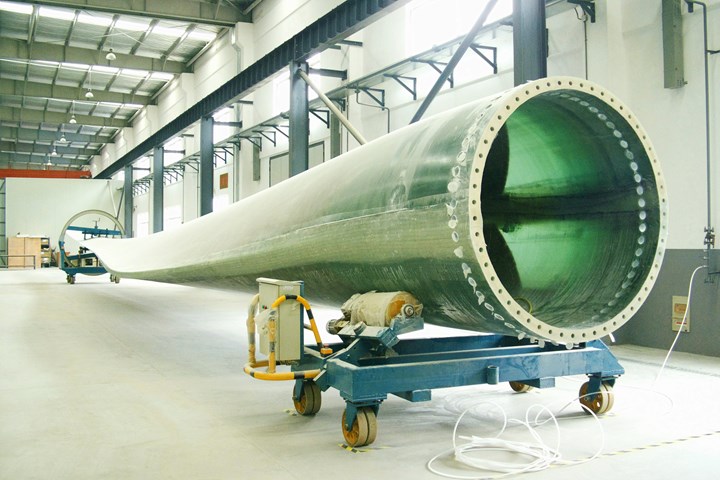
To support the development of wind turbines generating 10 megawatts (MW) of power or more, composite wind turbine blades are now able to exceed 100 meters (328 feet) in length. Increasing the size of wind blades can lead to a number of challenges in the manufacturing process, such as controlling resin flow during infusion over the length of such a large part.
According to global plastic net supplier (Hjørring, Denmark), the increasing size of wind blades — and the molds used to manufacture them — mean that a high-quality vacuum infusion process that maximizes productivity and minimizes cost is now more critical than ever. Expo-Net says customized resin mesh products can be key to maintaining control and high quality for wind blade OEMs.
The family owned business was founded more than 60 years ago, and has been supplying wind energy customers for more than 25 years with its extruded, inert thermoplastic netting. The company’s 12,000-square-meter facility, which houses offices, manufacturing, engineering, R&D and warehousing, is said to be ISO 9001:2015 and 14001:2015 certified.
According to the company, the two key functions of plastic flow mesh are to consistently ensure the rapid spread of the infusion resin throughout the composite component being molded, and to enable the efficient removal of air to avoid voids in the fiber-reinforced plastic (FRP) laminate system. To achieve this, one or more resin flow meshes are specified as part of the vacuum bagging infusion dry layup system placed in the mold tool prior to infusion (see diagram below).
Conventional flow mesh products are typically positioned in the mold tool immediately behind the vacuum bagging film and resin flow channels, which both sit on top of the disposable mesh. At the end of the infusion process, all non-integral flow mesh products are removed and, being thermoplastic, can be 100% recycled. To enable easy removal during demolding, release films and peel plies are placed beneath the flow mesh.
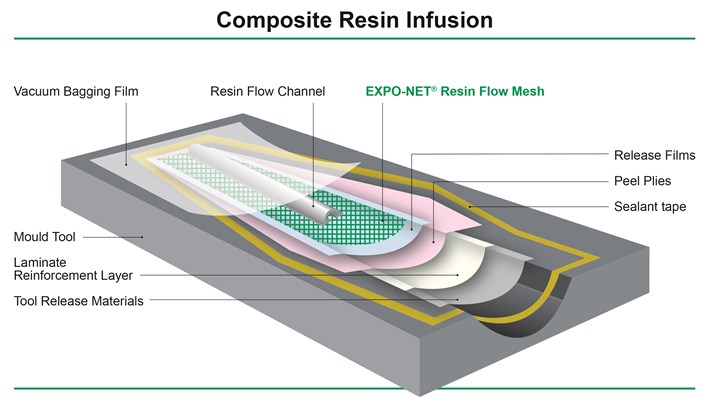
Lars Klinkby, Expo-Net managing director, explains the process: “We get involved at the early stage of an OEM’s new product development [NPD], advising their design and process engineers and developing customized Expo-Net resin flow mesh products specifically suited to the new blade size and design. A new wind blade NPD project can typically involve the Expo-Net team in several trials to modify and supply different resin flow mesh product combinations and specifications. We repeat this stage until the new blade is infused to the customer’s satisfaction. Once our resin flow mesh products are specified, we hold buffer stocks and regularly communicate with our strategic OEM and kitting customers to ensure we fulfill all order requirements.”
He adds that the NPD mesh approval stage for a new blade design can be repeated three to five times until the infusion process is optimized for various factors like resin volume, flow rate and proper air removal from the extremities of the part. As blades get longer, accuracy of resin flow is more of a challenge to consistently achieve, he says.
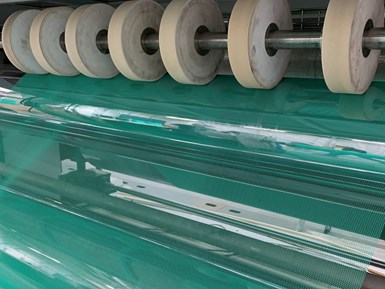
For longer blades, Expo-Net generally recommends infusing with a combination of a flat, drapable, fine net and a heavier, wide tubular net for certain sections of the blade. The tubular net accelerates resin flow, but is primarily designed to provide a rapid air release channel to speed up the removal of air from narrower laminate sections and part extremities. This tubular resin flow mesh is one of Expo-Net’s most recent product innovations, which came out of a customer project where improving productivity and reducing production costs were primary goals.
Expo-Net works both directly with OEMs and with kitting partners, such as (Nakskov, Denmark), a global outsourcing FRP composite materials kitting specialist for wind turbine blade and nacelle production. RewAir is headquartered in Denmark with production facilities in Spain, Poland and Denmark, and seeks to co-locate with supply partners to provide faster, just-in-time logistic services, cost savings and a higher degree of sustainability.
“To provide a more sustainable supply and recycling service with the lowest logistics carbon footprint possible, our strategic business model for major wind turbine blade manufacturers is to have a RewAir kitting facility co-located next door to their production operations,” notes Jens Rewers, president and CEO of RewAir Group. “Currently we have RewAir co-location facilities in Spain and Denmark, with more planned in the future.” In Denmark, RewAir and Expo-Net have worked closely together for more than 14 years.
“Expo-Net makes it easy for RewAir by providing a seamless technical and logistical cooperation together, coping with any changes in customer demand, rapidly altering flow mesh product dimensions for custom blade kits as needed, plus holding key safety stocks for OEM-specified Expo-Net mesh grades, so we avoid letting customers down,” Rewers says.
Related Content
Multi-material, self-sensing, 3D-printed scoliosis braces
Startup Fited and Brightlands Materials Center have developed a lighter weight, thinner CFRP corrective brace, including pressure sensors made from continuous carbon fibers.
Read MoreComposite materials, design enable challenging Corvette exterior components
General Motors and partners Premix-Hadlock and Albar cite creative engineering and a move toward pigmented sheet molding compound (SMC) to produce cosmetic components that met strict thermal requirements.
Read MoreSpanish startup to ramp up production of “recyclable” EV prototype
Liux’s BIG electric vehicle features multiple structural components manufactured via RTM from flax fabric and a thermoset resin said to enable the entire component to be recycled and reused again.
Read MoreCFRP planing head: 50% less mass, 1.5 times faster rotation
Novel, modular design minimizes weight for high-precision cutting tools with faster production speeds.
Read MoreRead Next
Plant tour: Daher Shap’in TechCenter and composites production plant, Saint-Aignan-de-Grandlieu, France
Co-located R&D and production advance OOA thermosets, thermoplastics, welding, recycling and digital technologies for faster processing and certification of lighter, more sustainable composites.
Read MoreVIDEO: High-volume processing for fiberglass components
Cannon Ergos, a company specializing in high-ton presses and equipment for composites fabrication and plastics processing, displayed automotive and industrial components at CAMX 2024.
Read MoreComposites end markets: New space (2025)
Composite materials — with their unmatched strength-to-weight ratio, durability in extreme environments and design versatility — are at the heart of innovations in satellites, propulsion systems and lunar exploration vehicles, propelling the space economy toward a $1.8 trillion future.
Read More