Compolift carbon fiber/epoxy telescopic masts extend to 7 meters (23 feet) and add strength and stiffness for carrying surveillance equipment on mobile border police vans. Photo Credit, all images: CompoTech
Founded in 1995, CompoTech (Sušice, Czech Republic) specializes in composite filament winding solutions, from concept design and analysis through to manufacturing. The company uses or licenses out its proprietary automated filament winding process for manufacturing cylindrical or rectangular carbon fiber/epoxy components for industry applications in aerospace, automotive, hydrogen storage, sports and leisure, marine and more. In recent years, the company has expanded into newer processes and applications, including robot-assisted filament placement, continuous fiber connection solutions called and innovative tooling and materials concepts.
One technology area the company has been working on for several years is telescopic masts — that is, a pole consisting of hollow, tubular sections that slide over each other to enable the overall structure to extend. In 2020, was formed as a separate venture specifically to produce these telescopic masts for a range of industries.
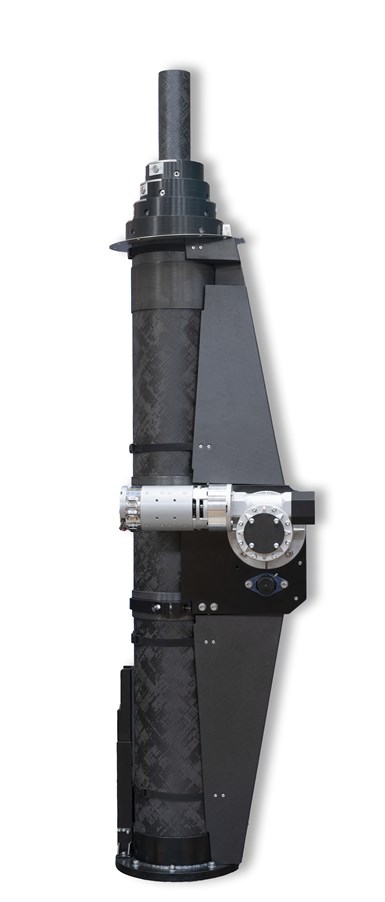
The Compolift technology stems from several telescopic projects that CompoTech had done in the past, explains Humphrey Carter, head of business development at CompoTech. For example, the company worked with a team from the University of West Bohemia (Pilsen, Czech Republic) to build an R&D demonstrator of an . In addition, telescopic masts were built as part of several marine projects, such as a proof-of-concept (POC) mast designed to carry an that can extend from 4.5 meters (14.7 feet) to 21 meters (69 feet) via a winch system. With part of the project targeting the development of wind-inflated sails to serve as auxiliary clean energy on cargo ships, a scaled-down version of the masts were designed for testing on a demonstrator yacht.
Telescopic masts for mobile surveillance units have become one key application area for the technology — and the reason for ultimately setting up Compolift as a separate entity, Carter notes. For years, CompoTech had already been producing one-piece, filament-wound aerial The telescopic technology enables extension as well as easier setup or removal of the masts.
Most recently, the Compolift telescopic mast concept was used to develop a series of 11 masts for the Czech Republic Border Police to be mounted to regional mobile police vehicles to carry visual/acoustic surveillance and radio communication equipment. The masts extend to a maximum height of 7 meters (23 feet) and provide a steady, rigid operating platform for the 16 kilograms (35 pounds) of equipment.

CompoTech designed both the mast itself and the winch mechanism used to raise and lower the mast. The mast comprises five hollow, interlocking tubes that together weigh only 17 kilograms (38 pounds), a 65% weight reduction compared to an alternative aluminum design. The overall system is extended and retracted by a 24-volt DC/750-watt electric motor, gearbox and winch unit, and the power and feed cables wind in a spiral around the exterior of the telescopic mast. Including the drive system and attached equipment, the total system weight is 64 kilograms (141 pounds).
The mast’s individual composite sections are filament wound from carbon fiber and a two-part epoxy resin system using CompoTech’s automated, robot-assisted filament winder. CompoTech’s proprietary system is designed to precisely place continuous axial fibers along the length of the mandrel, resulting in a rigid, high-strength final part. Each tube is filament wound at room temperature, followed by oven cure.
The company claims that customer testing shows that its filament winding technology results in parts that are 10-15% stiffer with up to 50% greater bending strength compared to the same part made using other filament winders. This, Carter explains, is due to the technology’s zero-degree winding capability under tension. These properties enable a fully assembled mast with the needed stability for the surveillance equipment, with little to no torsional or bending deflection.
Related Content
Composites end markets: New space (2025)
Composite materials — with their unmatched strength-to-weight ratio, durability in extreme environments and design versatility — are at the heart of innovations in satellites, propulsion systems and lunar exploration vehicles, propelling the space economy toward a $1.8 trillion future.
Read MoreThe next evolution in AFP
Automated fiber placement develops into more compact, flexible, modular and digitized systems with multi-material and process capabilities.
Read MorePost Cure: Parallel winding technique demonstrates CFRP anisogrid design optimization
Over the years, CIRA has demonstrated its patented CFRP parallel winding technique in a variety of ways for space applications. The lattice structure for the Vega-C launcher stage is a prime example.
Read MoreOptimizing robotic winding of composite tanks and pipes
Pioneer in mandrel-based reinforced rubber and composite products, TANIQ offers TaniqWindPro software and robotic winding expertise for composite pressure vessels and more.
Read MoreRead Next
Innovating composites to open new markets
From machine tools to trainer jets, CompoTech develops new design and process solutions.
Read MoreComposite T-boom accelerates industrial automation
A manufacturing method that integrates filament winding with axil winding of 0-degree fibers opens new design options in industrial automated equipment.
Read More“Structured air” TPS safeguards composite structures
Powered by an 85% air/15% pure polyimide aerogel, Blueshift’s novel material system protects structures during transient thermal events from -200°C to beyond 2400°C for rockets, battery boxes and more.
Read More