Lanxess launches renewable, biocomposite material
The material combines natural flax fibers with bio-based polylactic acid, which acts as the matrix, for a material that is 100% recyclable.
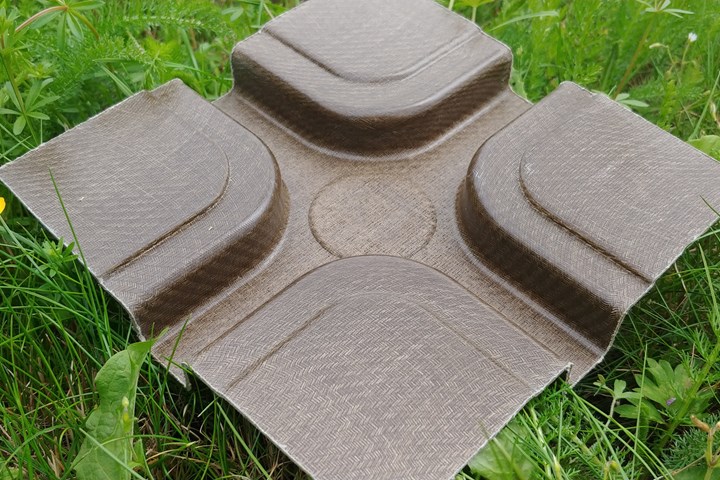
Photo Credit: Lanxess
Lanxess (Cologne, Germany) launches a new, fully biocomposite material in its Tepex range of continuous fiber-reinforced thermoplastic composites, in an effort to remove the reliance of fossil fuels from its own production processes. The material combines natural flax fibers with bio-based polylactic acid, which acts as the matrix, and can be produced on a large scale.
Lanxess’ continuous fiber-reinforced fabrics are said to be lighter in weight than glass fibers — flax fibers have a lower density — and offer mechanical performances typical of Tepex, which is based chiefly on the continuous fibers arranged in particular directions. The weight-specific stiffness of the biocomposite is also comparable to that of glass fiber-reinforced material variants. Further, designing the composite components to suit the expected loads enables most of the force to be transferred via the continuous fibers, ensuring high strength and stiffness.
In addition to sports equipment applications, the new biocomposite can reportedly be used in cars, such as for manufacturing interior parts, or in electronics for the production of housing components.
The material can also be 100% recycled. Lanxess notes that offcuts and production waste can be regranulated and easily injection molded or extruded, either alone or mixed with unreinforced or short fiber-reinforced materials.
In the medium term, Lanxess is planning to use other bio-based thermoplastics such as polyamide 11 and other natural and recycled fibers for the production of Tepex.
Related Content
-
Airbus works to improve the life cycle of composites in future aircraft
This companion article to CW's September 2024 Airbus Illescas plant tour discusses recycling, LCA, biocomposites, Fast Track technologies, qualification and more.
-
KCARBON and KIST develop lyocell/PLA/wood biocomposites
Initial demonstration in furniture shows properties two to nine times higher than plywood, OOA molding for uniquely shaped components.
-
PUR composite sandwich panels for 3D automotive parts, high-volume panels and more
At its U.S. sites, Ascorium produces glass fiber/PUR 3D parts via semi-automated molding, high-volume flat panels via a continuous line while working toward bio-based PUR and recycling.