Voith updates roving applicator generation technology
Voith GmbH is featuring carbon fiber-reinforced polymer (CFRP) components such as tailored stacks for the automotive and aerospace sectors.
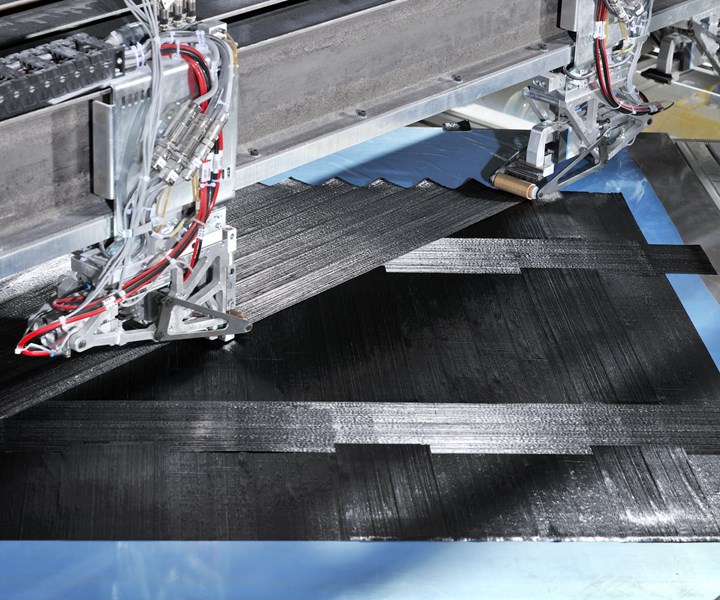
Source | Voith GmbH
Editor’s note: ÂÌñÏ×ÆÞ received several new product and technology announcements ahead of JEC World 2020, which had been scheduled for March 3-5. Although that exhibition was postponed to May, CW is now publishing the announcements we received. This is one of them.
Voith GmbH’s (Heidenheim, Germany; Hall 6, Booth U37) JEC World 2020 booth, themed “More than lightweight,” is featuring carbon fiber-reinforced polymer (CFRP) components such as tailored stacks for the automotive and aerospace sectors. The company is also presenting semi-finished products from the second Voith Roving Applicator Generation (VRA NextGen).
The first generation of VRA technology, which the company says has already been very well received in the market and honored with several awards, has been improved to now enable the direct deposition of prepreg tapes. Previously, this was only possible with dry material. Instead of applying a binder, the resin is impregnated directly into the fibers. According to Voith, this further streamlines the process chain and facilitates handling of the workpiece, especially if they are processed within the same production line. The technology is also suitable for series production of CFRP components.
Both the basic VRA technology and the further development VRA NextGen are reported to optimize fiber placement paired with Voith's innovations in fiber conditioning and tape handling. The result is customized stacks that are said to reduce waste and increase cost efficiency.
Related Content
-
Braided composites enable low-cost, high-rate fabrication
CAMX 2025: A&P Technology highlights its QISO and slit tape thermoplastic material capabilities through customer examples and industry applications.
-
Co-molding SMC with braided glass fiber demonstrates truck bed potential
Prepreg co-molding compound by IDI Composites International and A&P Technology enables new geometries and levels of strength and resiliency for automotive, mobility.
-
Aerospace prepregs with braided reinforcement demonstrate improved production rates, cost
A recent time study compares the layup of a wing spar using prepreg with A&P’s TX-45 continuous braided reinforcement versus traditional twill woven prepreg.