UCalgary researchers turn Alberta oilsands bitumen into high-value carbon fibers
University spearheads three projects out of the 12 teams chosen for Phase II of the Carbon Fibre Challenge, with a new target to produce the carbon fibers from bitumen at a lab scale.
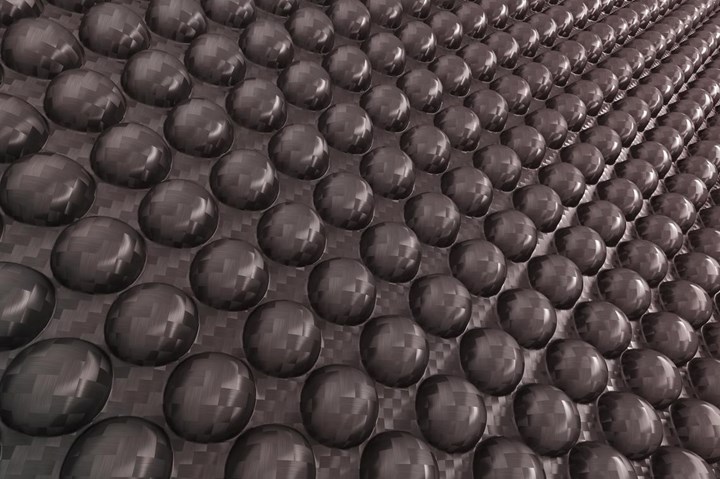
Photo Credit: Colourbox
Dr. Md Kibria, an assistant professor for the Department of Chemical and Petroleum Engineering at the Schulich School of Engineering for the University of Calgary (Calgary, Alberta, Canada), is leading one of three projects selected in the Carbon Fibre Challenge (CFGC) Phase II competition conducted by Alberta Innovates (Alberta, Canada) and the Clean Resource Innovation Network (CRIN, Canada).
The three-phase competition is aimed at accelerating the development of carbon fiber derived from Alberta’s vast supply of oilsands bitumen, a black viscous mixture of hydrocarbons obtained naturally or as a residue from petroleum distillation. Currently, Kibria and his team have been working with asphaltenes, — molecular substances found in crude oil — spinning the gooey substance together into strands finer than a human hair.
“Asphaltenes are commonly known as the ‘bottom of the barrel,’” says Kibria. “It’s the heavy fraction in bitumen which holds great promise to serve as a cheap feedstock for a wide variety of non-combustible, high-value products such as carbon fibers.”
The asphaltenes, says Kibria, are heated up to become a gel of sorts, which a spinner then winds into carbon fibers. The fibers then go through several steps to make them stronger, with some guessing and testing along the way. “We know that it’s feasible to make the fibers. Now the question is: How strong can we make it?” he questions.
Kibria hopes to create high-end carbon fibers that meet the standard for the automotive and airline industries, for which they can be used to create body components, wheels and rims, interior finishes and other products. He calls it a “win-win-win” situation because materials that don’t meet that high standard can still be used for other applications such as carbon fiber-reinforced concrete.
In addition to Dr. Md Kibria, two other Schulich professors, Dr. Simon Park, PhD, and Dr. Joanna Wong, Dr.sc.ETH — both with the Department of Mechanical and Manufacturing Engineering — are spearheading projects that also made it into the final 12 teams of the competition.
“One of the challenges associated with traditional carbon fiber-making is the high energy needed to convert polymer-based precursors to fibers,” Park says. “We are currently investigating new methods to generate carbon fibers by minimizing the energy usage through both chemical and electromagnetic treatments.”
In particular, his team is using both melt spinning and electrospinning processes to generate nano-scale and micro-scale fibers.
Wong, meanwhile, says her team’s approach “involves studying the chemical characteristics or particular fractions of different asphaltene samples. We are studying how their chemistries affect the rheology of the melts which, in turn, affects the quality of fibers that can be made.”
“ moves us closer to realizing the potential of ,” says Alberta Innovates CEO Laura Kilcrease. “Alberta’s vast reserves of bitumen are the building blocks to create new low-carbon opportunities throughout the province.”
In total, the 12 teams that moved on in the competition received a share of $5.27 million to produce the carbon fibers at a lab scale and develop a process with line of sight to a demonstration plant that can be commercially scaled.
“Our target isn’t just to make a product,” says Kibria, who received $500,000 in funding for Phase II. “We want to make a carbon fiber that the end users need for different applications.”
Park obtained $485,000 in funding and Wong secured $217,000 for the second phase of the competition, which is expected to wrap up in December 2022.
Phase III, which will see the finalists demonstrate how they can manufacture the fibers in a way to enable commercial investment, is expected to run from January 2023 to December 2024. View a list of the 12 best projects selected by Alberta Innovates and a committee of experts .
Related Content
Bladder-assisted compression molding derivative produces complex, autoclave-quality automotive parts
HP Composites’ AirPower technology enables high-rate CFRP roof production with 50% energy savings for the Maserati MC20.
Read MoreRevisiting the OceanGate Titan disaster
A year has passed since the tragic loss of the Titan submersible that claimed the lives of five people. What lessons have been learned from the disaster?
Read MorePlant tour: Airbus, Illescas, Spain
Airbus’ Illescas facility, featuring highly automated composites processes for the A350 lower wing cover and one-piece Section 19 fuselage barrels, works toward production ramp-ups and next-generation aircraft.
Read MoreLow-cost, efficient CFRP anisogrid lattice structures
CIRA uses patented parallel winding, dry fiber, silicone tooling and resin infusion to cut labor for lightweight, heavily loaded space applications.
Read MoreRead Next
All-recycled, needle-punched nonwoven CFRP slashes carbon footprint of Formula 2 seat
Dallara and Tenowo collaborate to produce a race-ready Formula 2 seat using recycled carbon fiber, reducing CO2 emissions by 97.5% compared to virgin materials.
Read MoreComposites end markets: New space (2025)
Composite materials — with their unmatched strength-to-weight ratio, durability in extreme environments and design versatility — are at the heart of innovations in satellites, propulsion systems and lunar exploration vehicles, propelling the space economy toward a $1.8 trillion future.
Read More“Structured air” TPS safeguards composite structures
Powered by an 85% air/15% pure polyimide aerogel, Blueshift’s novel material system protects structures during transient thermal events from -200°C to beyond 2400°C for rockets, battery boxes and more.
Read More