Spirit AeroSystems Europe delivers first set of A320 Family RTM spoilers
Redesigned spoilers developed via a highly automated advanced manufacturing, out-of-autoclave (OOA) process pioneered by Spirit.
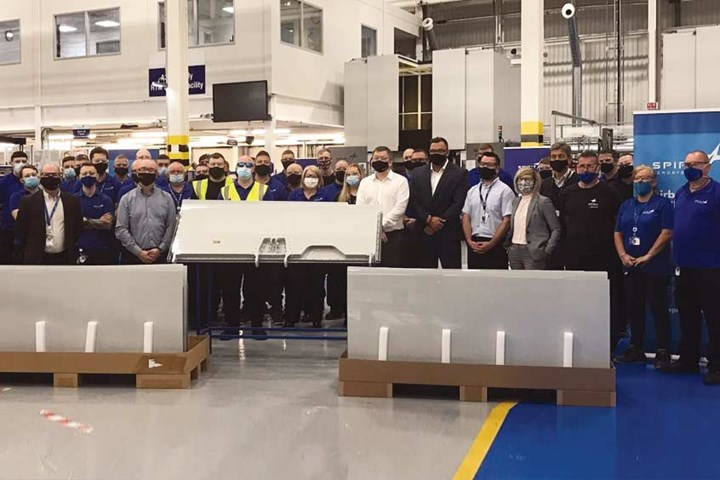
Spirit AeroSystems manufacturing facility in Prestwick celebrates the first shipment of spoilers to Airbus. Photo Credit: Spirit AeroSystems Europe
On Aug. 30 Spirit AeroSystems (Europe) Ltd. (Prestwick, Scotland), a subsidiary of Spirit AeroSystems Holdings Inc. (Wichita, Kan., U.S.) has successfully delivered the first set of new advanced composite spoilers to Airbus (Toulouse, France) for the A320 Family. The spoilers are produced using Spirit’s pioneering resin transfer molding (RTM) technology (see CW’s tour of this facility, “High-rate, automated aerospace RTM line delivers next-gen spoilers”) and are the first to feature on a flying aircraft.
The redesigned spoiler is produced using a highly automated advanced manufacturing, out-of-autoclave (OOA) process, resulting in what Spirit says are significantly improved manufacturing efficiencies, and reduced energy and costs compared to the original, more traditional design. Spirit is the first to industrialize this composite technology in the U.K. aerospace sector.
“This exciting milestone is another example of Spirit’s leadership in the development of innovative wing technologies and manufacturing processes to meet our customers’ needs,” says SVP Airbus Programs, Scott McLarty. “We remain committed to investing in the new technologies and processes required to deliver a more sustainable aerospace industry and help meet the U.K.’s net-zero goals.”
The spoilers are produced in Spirit’s world-class manufacturing facility in Prestwick, Scotland, using the latest automation and robotics, which included investment from the Scottish Government in the development of the technology. Spirit believes such cost-effective technologies and manufacturing processes will play a central role in the development of the next generation of aircraft programs, and help the company increase its competitive advantage in advanced manufacturing.
Related Content
-
Bucci Composites expands automotive production capabilities with facility addition, new high-ton presses
CW Top Shops recipient Bucci Composites shares an update on its facility expansion, automotive composites applications, sustainability, education initiatives and more.
-
Otto Aviation launches Phantom 3500 business jet with all-composite airframe from Leonardo
Promising 60% less fuel burn and 90% less emissions using SAF, the super-laminar flow design with windowless fuselage will be built using RTM in Florida facility with certification slated for 2030.
-
Ballistic protection panels manufacturer relies on automation for high throughput, efficiency
Maine-based CW Top Shops honoree Compotech Inc. recently doubled its manufacturing space and team to produce modular composite panels for defense applications via light resin transfer molding (LRTM).